Evaluating interlayer gaps in friction stir spot welds for rapid tooling applications
IISE TRANSACTIONS(2023)
摘要
Potential for a rapid hybrid additive/subtractive manufacturing technique capable of generating large aluminum components with deep geometrical features exists if, for example, layers of aluminum plates can be deposited and held in place using friction stir welding followed by machining. However, when plates of aluminum are friction stir spot welded together, adjacent material can deform causing a gap between layers. This research investigates how friction stir tool geometry affects the formation of interlayer gaps and the lap shear strength of the weld. For this purpose, residual stresses and microhardness were measured to characterize the weld formation process. While friction stir welding of 6061 aluminum bar stock was carried out on a machining center with three different pin diameters (5.7, 6.4, 7.0 mm) and two pin lengths (8.9, 10.2 mm). In general, outcomes of the research show that lap shear strength trends upward with increasing pin diameter but does not show a strong relation to the pin length. Interlayer gap size increases with pin length, but does not show a dear trend with pin diameter. Compressive residual stresses were observed on the weld shoulder with no significant variations occurring among the studied stir tool geometries. No significant change was measured in microhardness values when the pin length or shoulder diameter were changed, suggesting that the increase in lap shear strength is due to a change in weld cross-section instead of a material property change. This research will guide friction stir tool geometry selection for this hybrid manufacturing process and can be applied more broadly to any application where material deformation around a weld is undesirable.
更多查看译文
关键词
Friction stir spot welding,rapid tooling,additive manufacturing,CNC machining,hybrid manufacturing,residual stresses,solid state processing
AI 理解论文
溯源树
样例
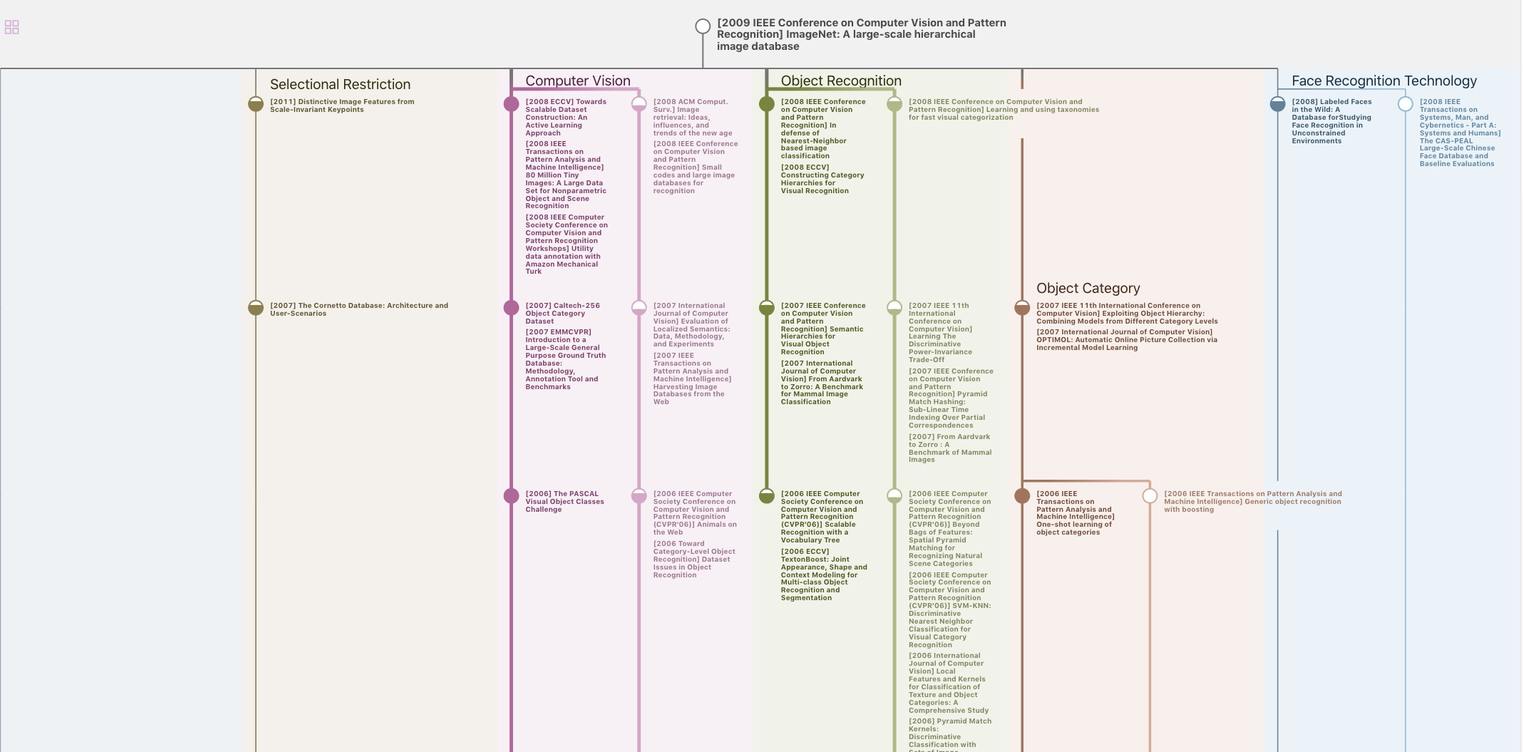
生成溯源树,研究论文发展脉络
Chat Paper
正在生成论文摘要