Advancing Automation in Early-Stage Navy Ship System Design
Day 3 Tue, June 28, 2022(2022)
摘要
Ship systems, such as the electrical distribution and thermal management systems, are larger, more complex, and more integrated than ever before due to the radical increase in electrical power used by new sensor and weapons systems, the resulting large thermal load placed on cooling systems, and the advances in integration of ship, mission and machinery control systems. Thus, there is a significant need for greater detail in ship system design to be provided earlier in the ship design process. Advances in computing capability over recent years allow an increase in detail of early-stage ship designs along with a simultaneous increase in the number of ship designs explored, facilitating design processes such as set-based design. This paper describes a body of work that provides a methodology for semi-automated design of ship systems, allowing the programmatic creation and analysis of ship systems under the guidance of the user, assembled from pre-designed templates and tailored to the ship design. We refer to this overall methodology as Templating. The ultimate goal is a software tool which takes as input a set of pre-designed system segments, termed templates, and integrates them into a fully functioning system model in a ship design, with all components appropriately sized and located. The resultant system model provides metrics such as size, weight and complexity. Further, the model is available for system simulation under various operational conditions to provide metrics such as efficiency and survivability while also allowing exploration of reconfigurability, reliability, maintainability, and a host of other “ilities.” The Templating process and software is fully integrated into the U.S. Navy’s early-stage design tool suite. The process for creating a fully functional ship system from templates requires several steps: Assembly of the templates into a logically connected system by copying relevant templates into the ship design and connecting them appropriately to one another. This yields a logically appropriate one-line diagram with components placed in an approximate geographic position within the ship. Determination of the capacity of each component. Since the templating capability facilitates the creation of ship systems from an assembly of parts or system sub-sections, it is not possible to determine the required capacity of each element of a system until the system is fully assembled with all loads and sources connected and placed in three-dimensional space. An algorithm has been developed to determine the maximum amount of energy handled by each component given any possible alignment of the system. Dimensioning of each component based on the capacity required. Physics-based sizing algorithms for a variety of component types are under exploration. Final placement of the components in three-dimensional space. A methodology for automatically arranging components in a ship design in a manner that eliminates overlaps, provides spacing between components, and minimizes connection length has been developed. This paper provides an overview of the templating process and the algorithms underlying each step, provides examples to elucidate the methodologies, and demonstrates that the functionality brought about by Templating advances automated system design in the early-stage ship design process.
更多查看译文
AI 理解论文
溯源树
样例
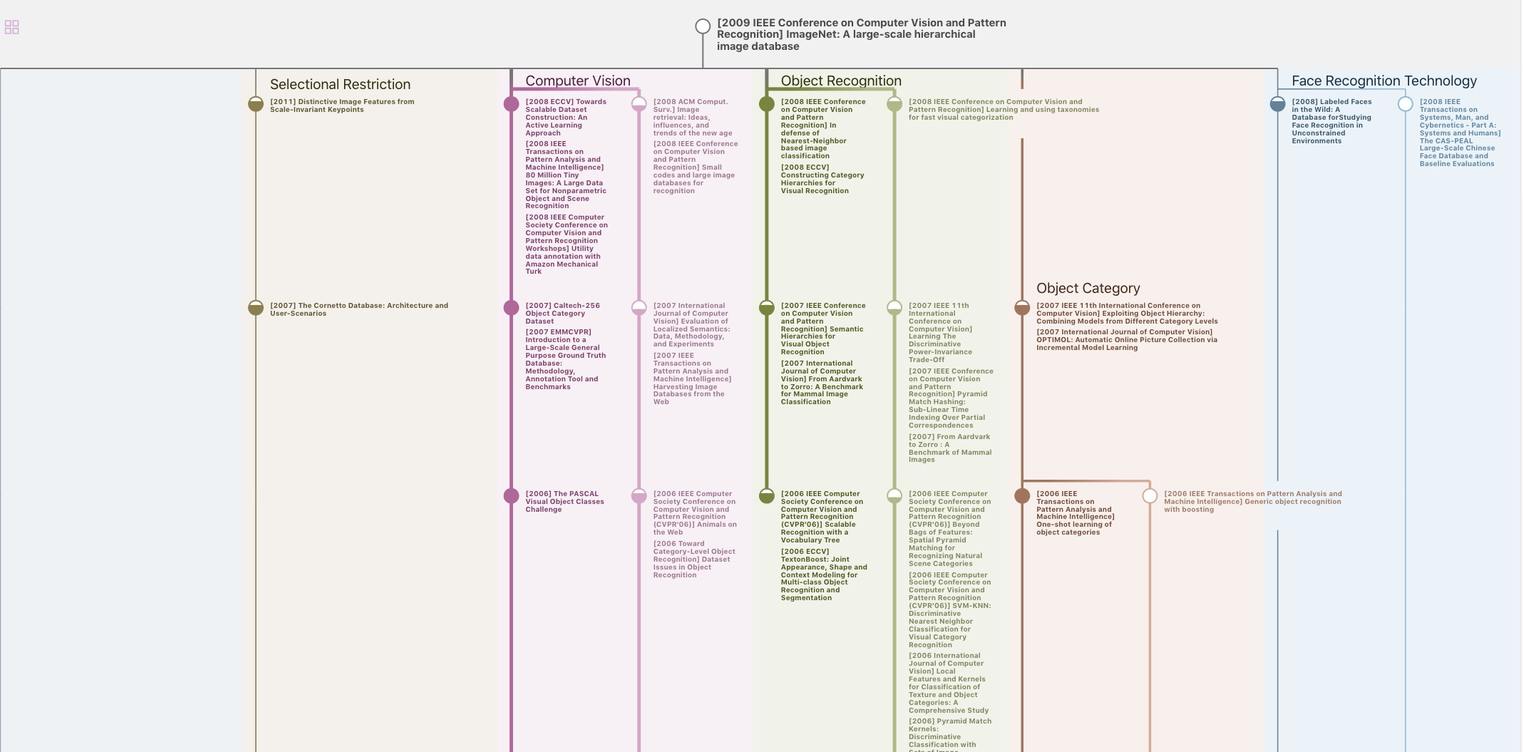
生成溯源树,研究论文发展脉络
Chat Paper
正在生成论文摘要