Testing and simulation of a composite-aluminium wingbox subcomponent subjected to thermal loading
COMPOSITE STRUCTURES(2022)
摘要
Modern aircraft designs combine carbon-aluminium assemblies mechanically joined by steel bolts. The different thermal expansion coefficient of these materials and the substantial temperature excursions during aircraft operation, lead to thermal stresses that alter the load distribution of the bolted joint. These stresses can compromise the structural integrity of large components and they are difficult to anticipate. In this paper, we present a detailed experimental and computational study of a hybrid carbon-aluminium wingbox subcomponent. Thermal tests were performed to determine the global deformation of the assembly. The numerical model is compared against the experiments and is used to extract additional information that cannot be easily measured experimentally, for instance the evolution of the bolt preload with temperature. The agreement between the experimental results and simulation instils confidence in the proposed methodology to identify, and minimise through redesign, areas prone to damage due to the combination of thermal and mechanical loads.
更多查看译文
关键词
Bolted joints, Testing, Thermal loading, Aircraft structure, Composite laminates, Finite element method
AI 理解论文
溯源树
样例
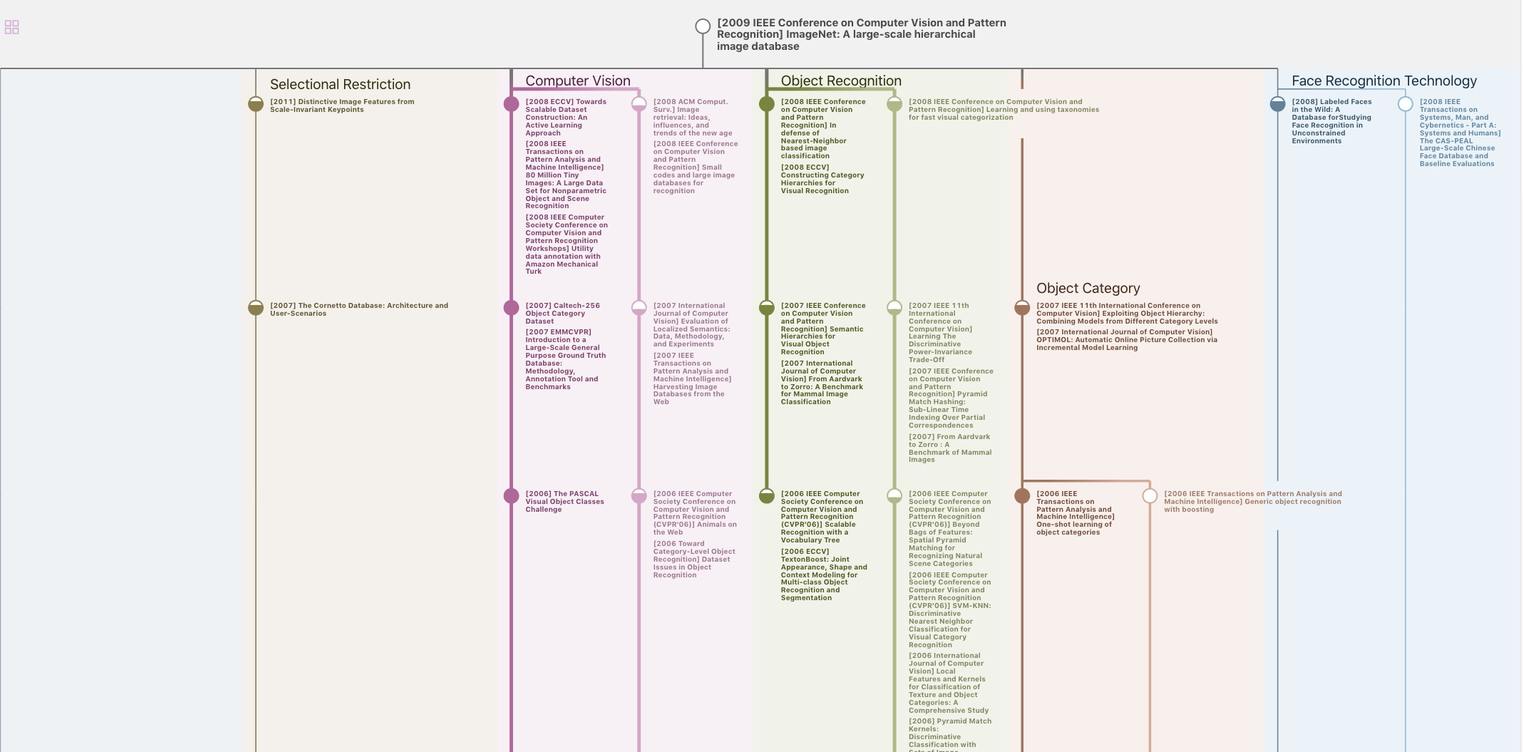
生成溯源树,研究论文发展脉络
Chat Paper
正在生成论文摘要