Laser polishing of additively manufactured 316L stainless steel with different construction angles
The International Journal of Advanced Manufacturing Technology(2022)
摘要
Laser polishing process is a promising technology for post-processing of complex parts prepared by additive manufacturing. In this study, the nanosecond laser polishing process was employed to improve a surface roughness of SLM (selective laser melting) prepared 316 L stainless steel with different part orientation (0°, 15°, 45°, 75° and 90°) during construction. Afterwards, the changes of surface topography, morphology and the cross-sectional microstructure before and after laser polishing were investigated. Additionally, the study also focusses on the process of 3D printing, especially on material porosity after sintering process. The results obtained from computer tomography showed that the samples were well prepared, with porosity below 0.019%. After laser polishing, surface roughness represented by S a and S z values was reduced for all printed samples regardless to their construction angle with similar laser and scanning parameters. The maximum roughness reduction reaches more than 90% (from S a = 9.8 µm to S a = 0.77 µm). Moreover that, other surface analysis established the best conditions for laser polishing. Finally, from the cross-section, the microstructure analysis was done and thickness of melted layer, heat-affected zone followed by microhardness measurement was estimated. Except of one applied condition, all samples were very homogenic with no damages in intersection layer. Simultaneously, there were no changes in microhardness after laser process observed.
更多查看译文
关键词
Laser polishing,SLM,Construction angle,Surface roughness,316L
AI 理解论文
溯源树
样例
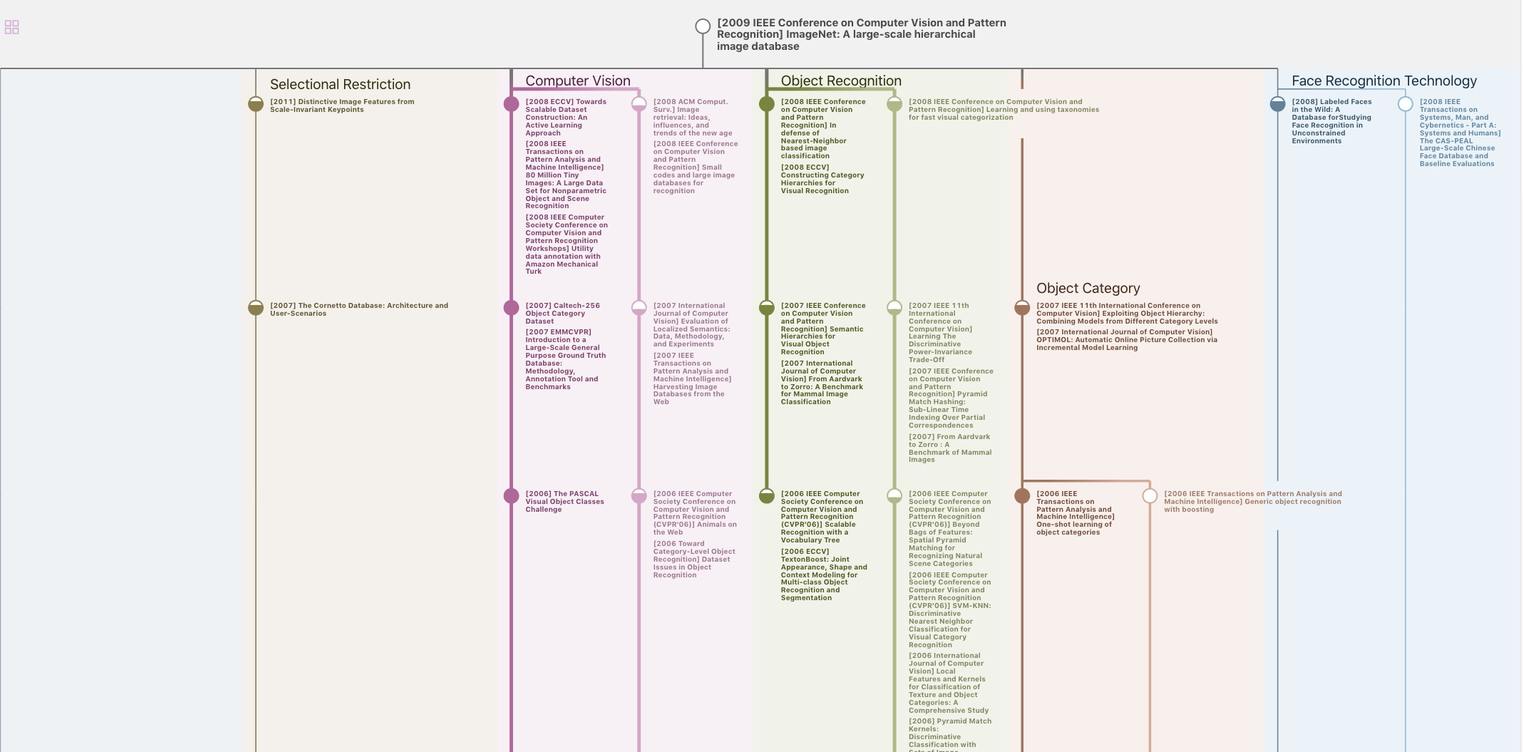
生成溯源树,研究论文发展脉络
Chat Paper
正在生成论文摘要