On the Morphological Deviation in Additive Manufacturing of Porous Ti6Al4V Scaffold: A Design Consideration
MATERIALS(2022)
摘要
Additively manufactured Ti scaffolds have been used for bone replacement and orthopaedic applications. In these applications, both morphological and mechanical properties are important for their in vivo performance. Additively manufactured Ti6Al4V triply periodic minimal surface (TPMS) scaffolds with diamond and gyroid structures are known to have high stiffness and high osseointegration properties, respectively. However, morphological deviations between the as-designed and as-built types of these scaffolds have not been studied before. In this study, the morphological and mechanical properties of diamond and gyroid scaffolds at macro and microscales were examined. The results demonstrated that the mean printed strut thickness was greater than the designed target value. For diamond scaffolds, the deviation increased from 7.5 mu m (2.5% excess) for vertical struts to 105.4 mu m (35.1% excess) for horizontal struts. For the gyroid design, the corresponding deviations were larger, ranging from 12.6 mu m (4.2% excess) to 198.6 mu m (66.2% excess). The mean printed pore size was less than the designed target value. For diamonds, the deviation of the mean pore size from the designed value increased from 33.1 mu m (-3.0% excess) for vertical struts to 92.8 mu m (-8.4% excess) for horizontal struts. The corresponding deviation for gyroids was larger, ranging from 23.8 mu m (-3.0% excess) to 168.7 mu m (-21.1% excess). Compressive Young's modulus of the bulk sample, gyroid and diamond scaffolds was calculated to be 35.8 GPa, 6.81 GPa and 7.59 GPa, respectively, via the global compression method. The corresponding yield strength of the samples was measured to be 1012, 108 and 134 MPa. Average microhardness and Young's modulus from alpha and beta phases of Ti6Al4V from scaffold struts were calculated to be 4.1 GPa and 131 GPa, respectively. The extracted morphology and mechanical properties in this study could help understand the deviation between the as-design and as-built matrices, which could help develop a design compensation strategy before the fabrication of the scaffolds.
更多查看译文
关键词
additive manufacturing, geometry deviation, mechanical properties, nanoindentation, surface roughness, Ti6Al4V scaffolds, bone scaffolds
AI 理解论文
溯源树
样例
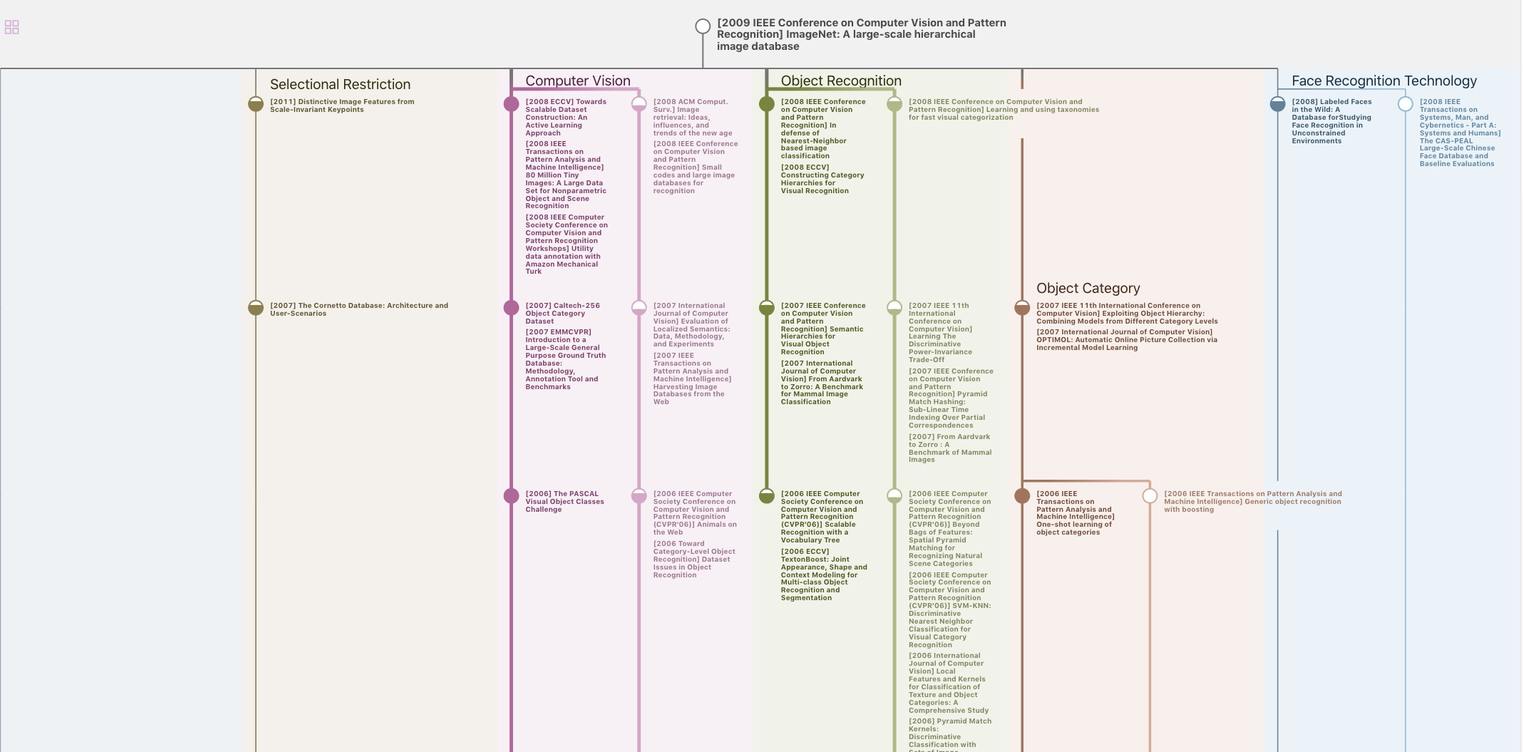
生成溯源树,研究论文发展脉络
Chat Paper
正在生成论文摘要