Mechanical and Thermal Properties of Glass Reinforced Composites
IEEE TRANSACTIONS ON APPLIED SUPERCONDUCTIVITY(2022)
摘要
In our Pulsed Field Facility, we use epoxy fillers to create smooth, strong winding transitions between layers of coils in our consumable pulsed magnets. For structural support, we often use materials like G10, a high-pressure fiberglass laminate consisting of multiple glass layer cloths soaked in epoxy. In liquid nitrogen, such materials have good mechanical and dielectric strength. To accommodate gaps at transitions, epoxy fillers typically have complex shapes, which render their fabrication expensive and time-consuming. In addition, the machining of epoxies like G10 can be hazardous. In this study, we replaced machining with 3D printing, using thermo-plastic, strengthened by glass fiber, as the raw material. Polyether Ether Ketone (PEEK) material as well as nylon material were used as the matrix. The strengthening components were chopped E-glass fibers or beads. We found that 3D printing can significantly reduce manufacturing cost for our magnets. Because our magnets must operate between 77 K and 295 K, we measured mechanical and thermal properties for both the nylon and the PEEK composites at both temperatures. The measured direction of the samples was parallel to the printing direction. The measured maximum compressive strength was about 258 MPa. Although the strength is lower than G10, the techniques we developed in this study would apply to 3D printing technology for various cryogenic applications like winding transition or experimental probes that are not exposed to very high stress in high field magnets.
更多查看译文
关键词
Thermal expansion, Magnetic resonance imaging, Glass, Magnetomechanical effects, Testing, Superconducting magnets, Image coding, Cryogenic, mechanical strength, polymers, pulsed magnets, thermal contraction
AI 理解论文
溯源树
样例
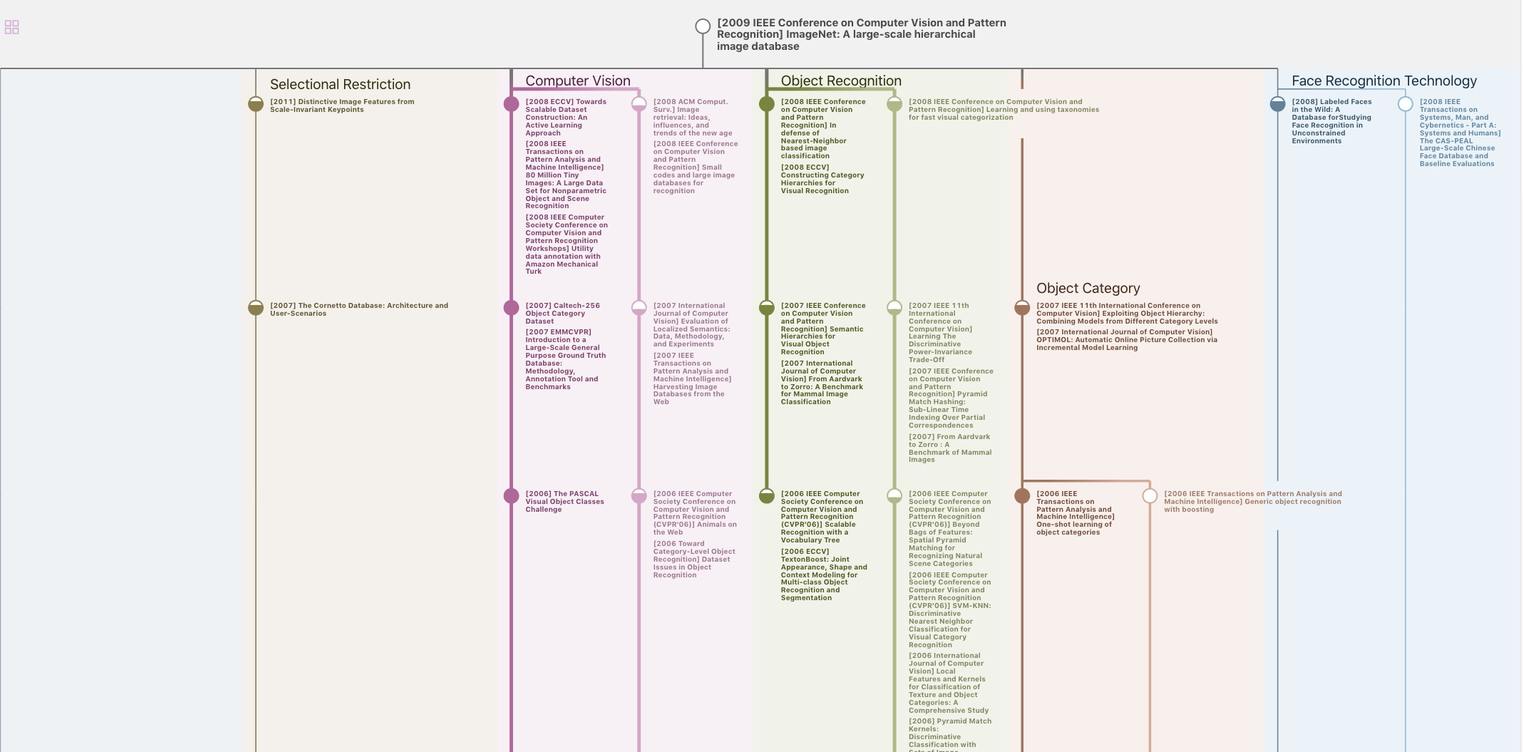
生成溯源树,研究论文发展脉络
Chat Paper
正在生成论文摘要