Towards the sustainable synthesis of microporous and layered titanosilicates: mechanochemical pre-treatment reduces the water amount
Green Chemistry(2022)
摘要
There has been growing awareness of the importance of developing environmentally friendly chemical processes. In this context, the synthesis of materials by mechanical grinding or milling holds much promise. Microporous zeolitic materials are well-known for their importance as catalysts, ion exchangers, and in gas separation and storage. Here, the incorporation of a mechanosynthesis (ball milling) step in the preparation of an important class of zeolite-type materials, microporous titanosilicates, is shown to reduce by one to two orders of magnitude the amount of water used, as compared with the conventional hydrothermal synthesis. Accordingly, no water was added to the reagents in the synthesis of the small-pore synthetic analogue of minerals sitinakite (Na2Ti2O3SiO4·2H2O), now a commercial Cs+ ion exchanger, and ivanyukite-K (also known as GTS-1, HK3Ti4O4(SiO4)·4H2O). The preparation of the important microporous titanosilicate ETS-10 ((Na,K)2TiSi5O13·nH2O), microporous AM-2 (K2TiSi3O9·H2O), and the analogue of the layered mineral natisite (Na2TiO(SiO4)) required only the addition of a very small amount of water. The increased reactivity of the ball-milled reaction mixture is ascribed to the reduction of the precipitated silica particle size (ETS-10 synthesis) and the increased number of silica nanoparticle silanol groups (ETS-10 and sitinakite synthesis). Moreover, in general, the ball milling step also decreased the synthesis time considerably, in most cases resulting in significant energy saving (3–34 times) over conventional hydrothermal synthesis. This work shows that mechanosynthesis enables the preparation of microporous (and layered) titanosilicates by a process that is more sustainable than the conventional hydrothermal synthesis and is also amenable for upscaling.
更多查看译文
AI 理解论文
溯源树
样例
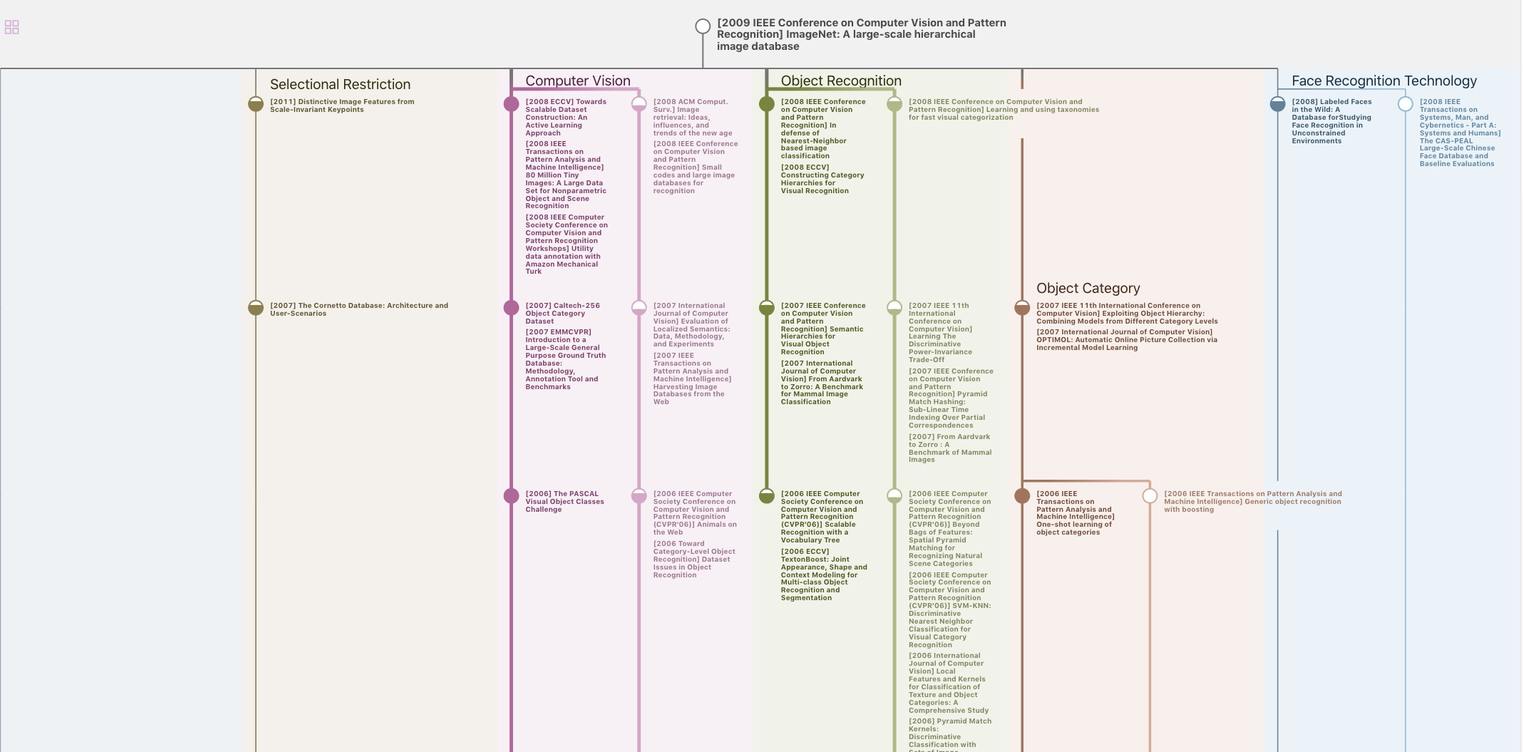
生成溯源树,研究论文发展脉络
Chat Paper
正在生成论文摘要