Life Prediction of Thermal Barrier Coated C3X Gas Turbine Blade of CMSX-4 Material
ASME 2021 Gas Turbine India Conference(2021)
摘要
Abstract The drive to higher efficient gas turbine engines and improved performance is attained by increasing turbine inlet temperature. This lead to the use of advanced material, multi-layered thermal barrier coatings (TBCs) and effective cooling technique in a gas turbine blade system. The main objective is to predict and compare the life between an uncoated blade developed by NASA named C3X and a tri-layered thermal barrier coated C3X blade working under four different high temperature operating conditions. The geometry of the uncoated blade was modelled using Catia software. Three layers of coatings i.e., top coat, bond coat and thermally grown oxide with suitable thickness were generated by the mesh offset technique which was applied to an uncoated blade to model the coated blade. Thereafter steady-state 3D conjugate heat transfer analysis (CFD) with k-ε turbulence model by Ansys Cfx was performed to obtain temperature, pressure and heat transfer coefficient distribution on the surface of the blade. Firstly, this CFD analysis was performed using stainless steel as substrate material, then validated with experimental values and lastly, the same simulation model was applied to Nickel based super-alloy CMSX-4 material. The next step was carrying out transient uncoupled heat transfer, thermal stress, mechanical stress and sequentially coupled thermo-mechanical stress analyses using Abaqus for a flight length of 5000 seconds. At last, the creep-fatigue interaction life of the blade was computed by ductility exhaustion concept with morrow mean stress correction method using Fesafe/Turbolife software. After carrying out above mentioned processes for both uncoated and coated blade, an effective comparison was made. A significant decrease in Temperature (up to 127 K) and Thermo-Mechanical Stress (up to 263 MPa) and a significant increase in Fatigue-Creep Life (up to 16.5 times) was observed when TBCs were applied. The result shows that the thermal load was more severe than the mechanical load. The maximum thermo-mechanical stress was found at the trailing edge and fixed portion of the blade.
更多查看译文
关键词
C3X Turbine Blade,CMSX-4,CFD,FEM,Thermal Barrier Coating,Thermo-Mechanical
AI 理解论文
溯源树
样例
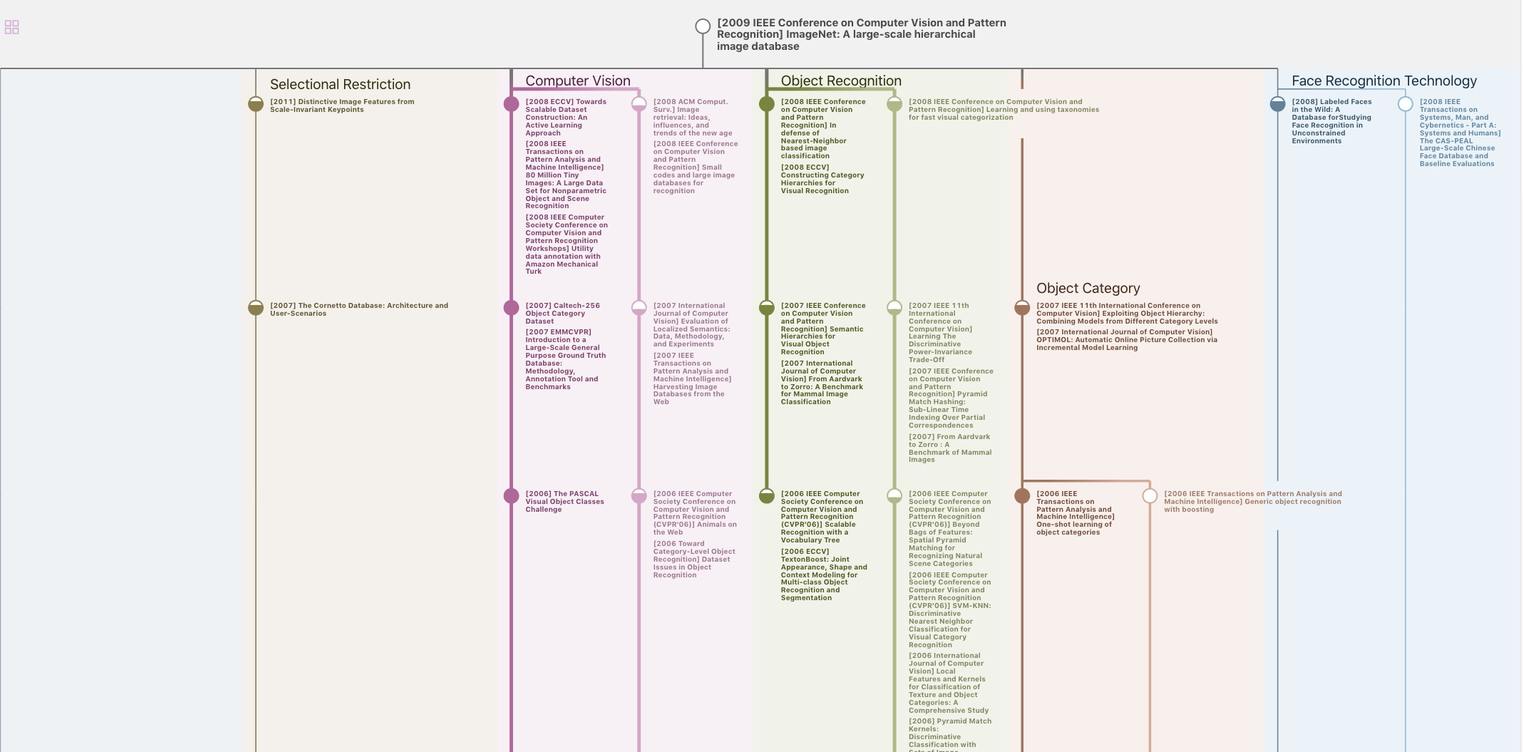
生成溯源树,研究论文发展脉络
Chat Paper
正在生成论文摘要