Practical application of six SIGMA methodology to reduce defects in a Pakistani manufacturing company
Journal of Applied Engineering Science(2022)
摘要
All over the world six sigma is being adopted as a quality improvement approach towards zero defects. Unfortunately, the adoption of six sigma methodology in manufacturing companies is very rare in developing countries due to various challenges. This study demonstrates the practical use of the six sigma Define, Measure, Analyze, Improve and Control (DMAIC) cycle by conducting a case study at a manufacturing company in Pakistan. The potential problem was the external leakage defect in the refrigerator during its production stage. The objective of this study was to improve the process by adopting six sigma DMAIC approach to identify and eliminate the root causes that produce defects in the final product. Project charter, Pie chart, Bar chart of faults, Suppliers Input Process Output (SIPOC), Voice of Customer (VOC) and flow process map were used to define the problem, its scope and process routing. Pareto chart was used to identify sub defects and sigma level was calculated for the existing process. Feed rate, capillary action of filler material, cleanliness, visual inspection and unsuitable heat input were the major causes of external leakage. Cause and effect matrix was used to rank the identified causes. Further, design of experiment (DoE) was performed to improve the process by conducting different alterations in the parameters. In order to control the process, failure mode and effect analysis (FMEA) sheet was prepared to sustain the process improvements. The FMEA control plan needed to be revised at specific time intervals to attain continuous process improvement. This six sigma DMAIC cycle produced a 30% overall reduction of external leakage defect and service call rate (SCR) was improved with lower complaints from customers.
更多查看译文
关键词
six sigma dmaic cycle,case study
AI 理解论文
溯源树
样例
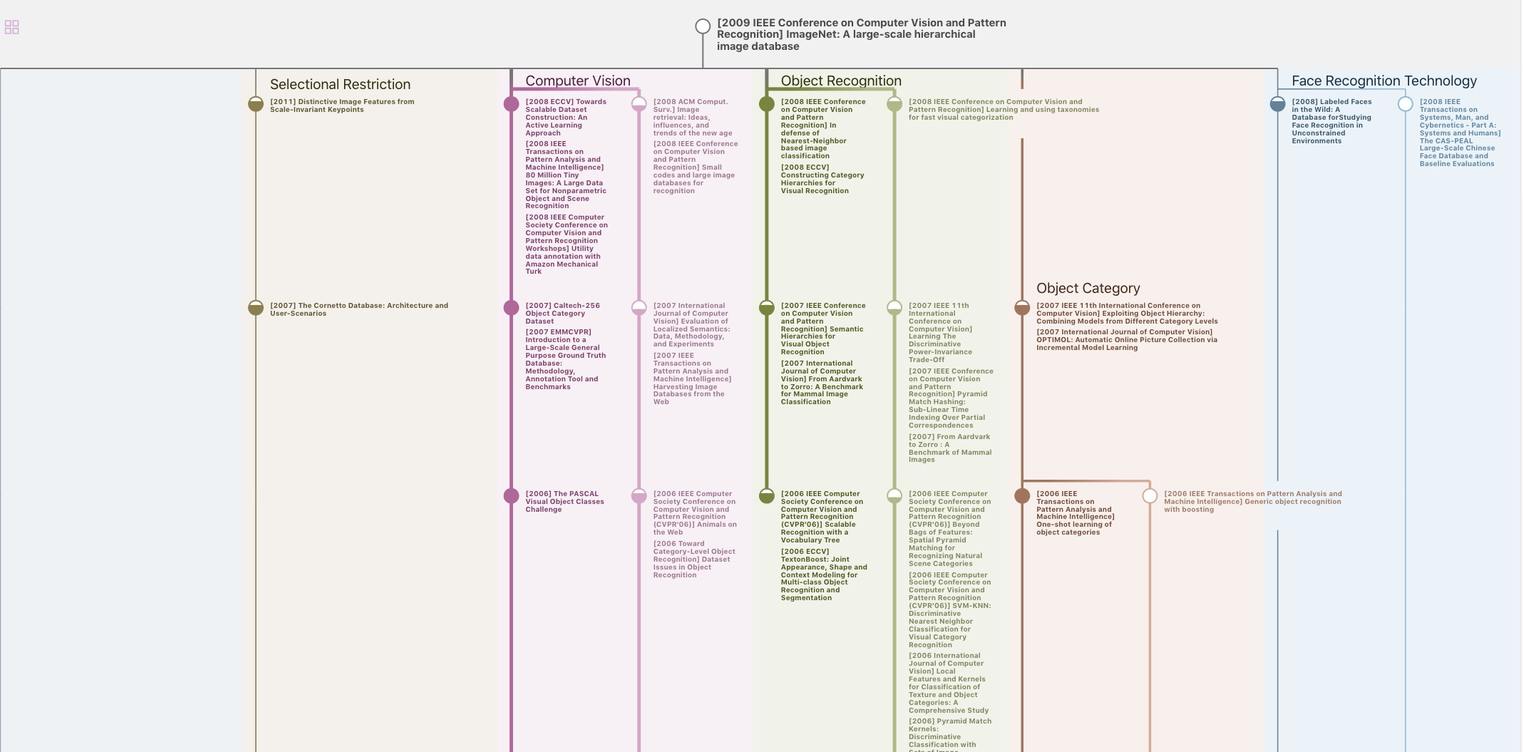
生成溯源树,研究论文发展脉络
Chat Paper
正在生成论文摘要