An experimental investigation into influences of build orientation and specimen thickness on quasi-static and dynamic mechanical responses of Selective Laser Melting 316L Stainless Steel
Materials Science and Engineering: A(2022)
摘要
Additive Layer Manufacturing (ALM) processes like Selective Laser Melting (SLM) enable the conception of complex designs with a high precision and equal or enhanced mechanical properties compared to Conventionally Manufactured (CM) structures. Nevertheless, this process, which consists in melting metallic powders layer by layer with a laser beam, greatly influences the microstructure and therefore the mechanical properties. While some studies have considered the effects of the thickness and/or the building direction of 316L Stainless Steel (SS) specimens produced by SLM on the quasi-static mechanical behavior, the strain rate effect for crash or impact applications on these two parameters has not been fully investigated. To complete the actual knowledge, the present work proposes to analyze the mechanical behavior of 316L SS tensile specimens produced by SLM with different build orientations (0°, 45° and 90°) and thicknesses (0.5, 0.75, 1 mm) and submitted to dynamic loadings at various strain rates up to 103 s−1. In addition, the microstructure and the fracture surfaces are analyzed to give a more detailed comprehension of the mechanical tests. It results that the SLM 316L SS achieves better Yield Stress (YS), similar Ultimate Tensile Stress (UTS) and equal or lower failure strain compared to the CM material. This is mainly a result of microstructure refinement. Anisotropy is observed at the macroscopic level with higher tensile stress and lower failure strain for horizontal specimens, which is explained by the different shapes, orientation and size of the grains at the microscopic level. The mechanical properties greatly decrease as the thickness reduces from 1 to 0.5 mm, by 14% for the YS and 16% for the UTS for a quasi-static loading. A minimum thickness of 0.75 mm is advised to at least recover the mechanical properties of the CM 316L SS. A positive strain rate sensitivity, higher than the CM material, is observed for all configurations, with the exception of 0.5 mm thickness. For strain rates ranging from to 10−3 to 103 s−1, there is an increase of 20% of the UTS. The material anisotropy is not affected by the strain rate sensitivity whereas the latter increases with the thickness.
更多查看译文
关键词
Additive manufacturing,Stainless steel,Dynamic behavior,SEM analysis
AI 理解论文
溯源树
样例
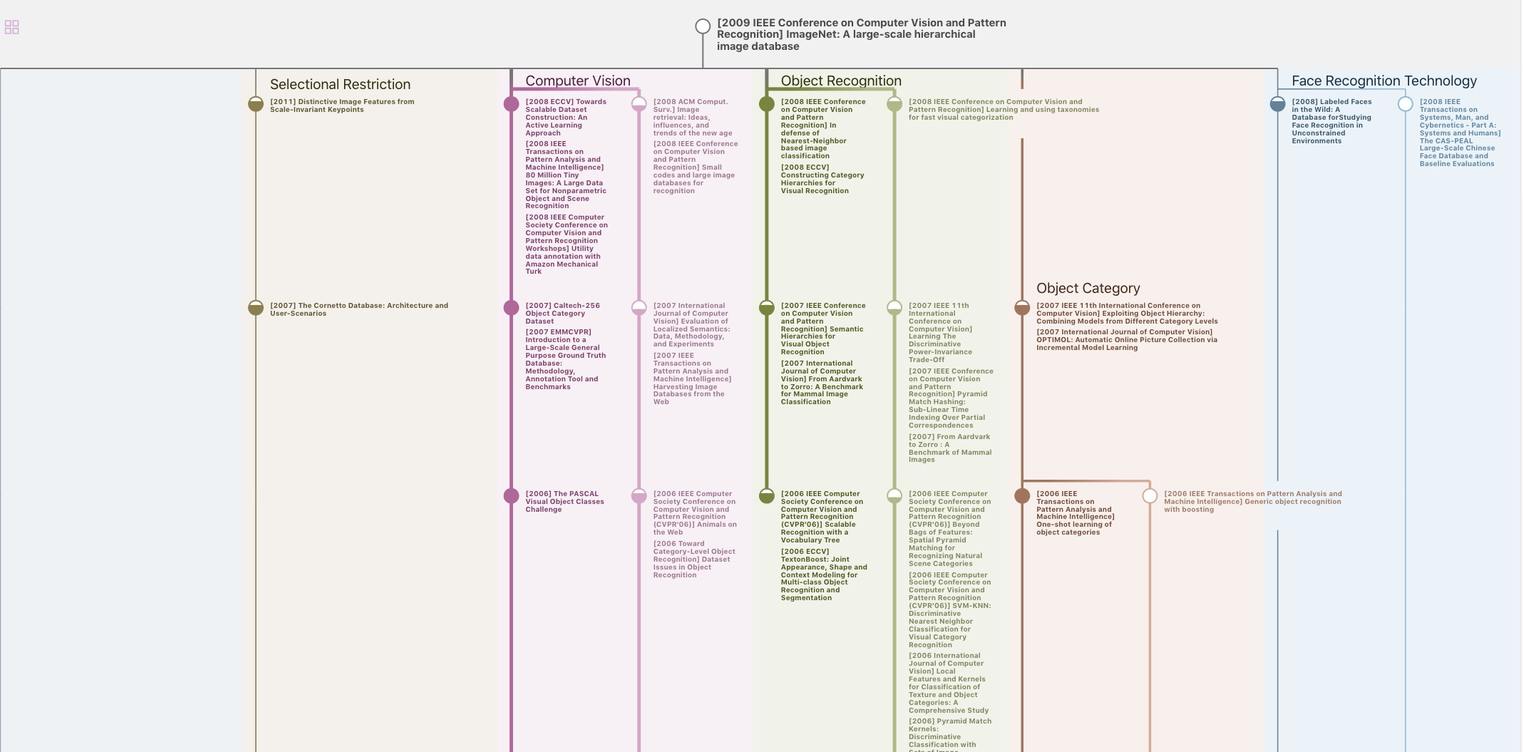
生成溯源树,研究论文发展脉络
Chat Paper
正在生成论文摘要