Enhancement Modelling Based on Electrical Discharge Machining Successive Discharges
ADVANCES IN MATERIALS SCIENCE AND ENGINEERING(2022)
摘要
The surface roughness of Inconel 718 is predicted using a sequential discharge model for electrical discharge machining (EDM). To begin with, the EDM single pulse discharge machining process was accurately simulated using the finite-element method (FEM). The surface topography under various discharge settings, the size, and the characteristic parameters of a single-pulse crater are simulated. Second, the material defines the discharge position as the minimum gap width between the work piece's starting surface and the electrode in the removal model. The simulation shows that the magnitude of the single-pulse discharge energy influences the crater's form and size. A difference in discharge energy causes a divergence in the increasing crater radius, depth, and flanging height trends. On the other hand, the ultimate surface morphology of an EDM machined surface is determined by the distribution of discharge locations around the parts in the workpiece; finally, machined surfaces are inspected using the same discharge parameters. The EDM work piece's surface morphology matches the material removal. Between simulation and experiment, there is a relative error in surface roughness around 8.26%, and there is a relative error in surface roughness.
更多查看译文
关键词
discharges,modelling,enhancement
AI 理解论文
溯源树
样例
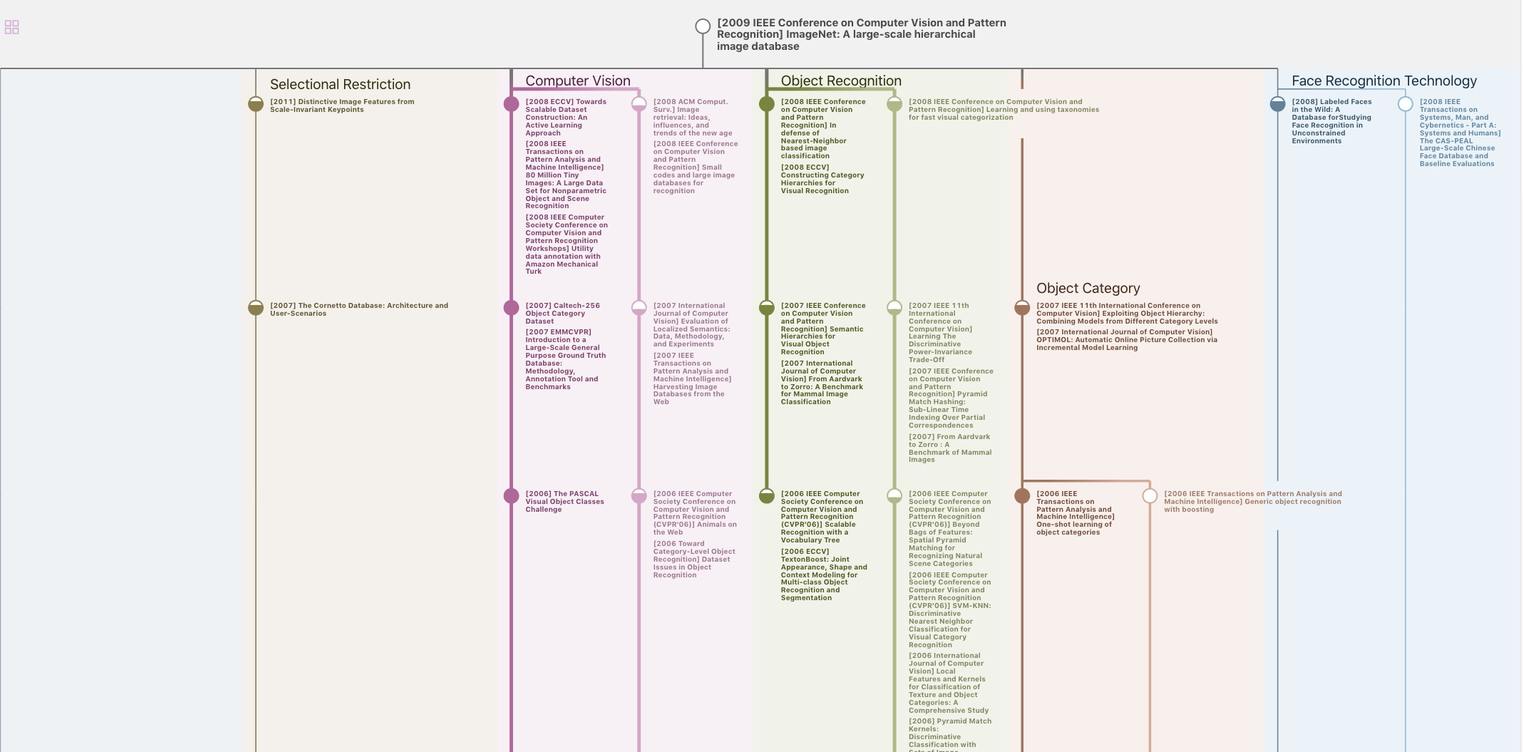
生成溯源树,研究论文发展脉络
Chat Paper
正在生成论文摘要