Interpolation and Extrapolation of Optimally Fitted Kinematic Error Model for Five-Axis Machine Tools
JOURNAL OF MANUFACTURING SCIENCE AND ENGINEERING-TRANSACTIONS OF THE ASME(2022)
摘要
Machine tool geometric errors are frequently corrected by populating compensation tables that contain position-dependent offsets to each commanded axis position. While each offset can be determined by directly measuring the individual geometric error at that location, it is often more efficient to compute the compensation using a volumetric error model derived from measurements across the entire axis space. However, interpolation and extrapolation of measurements, once explicit in direct measurement methods, become implicit and obfuscated in the curve-fitting process of volumetric error methods. The drive to maximize model accuracy while minimizing measurement sets can lead to significant model errors in workspace regions at or beyond the range of the metrology equipment. In this paper, a method of constructing machine tool volumetric error models is presented in which the characteristics of the interpolation and extrapolation errors are constrained. Using a typical five-axis machine tool compensation methodology, a constraint bounding the tool tip modeled error slope is added to the error model identification process. By including this constraint over the entire space, the geometric errors over the interpolation space are still well identified. Also, the model performance over the extrapolation space is consistent with the behavior of the geometric error model over the interpolation space. The methodology is applied to an industrial five-axis machine tool. In the experimental implementation, for measurements outside of the measured region, an unconstrained model increases the mean residual by 40% while the constrained model reduces the mean residual by 40%.
更多查看译文
关键词
control and automation
AI 理解论文
溯源树
样例
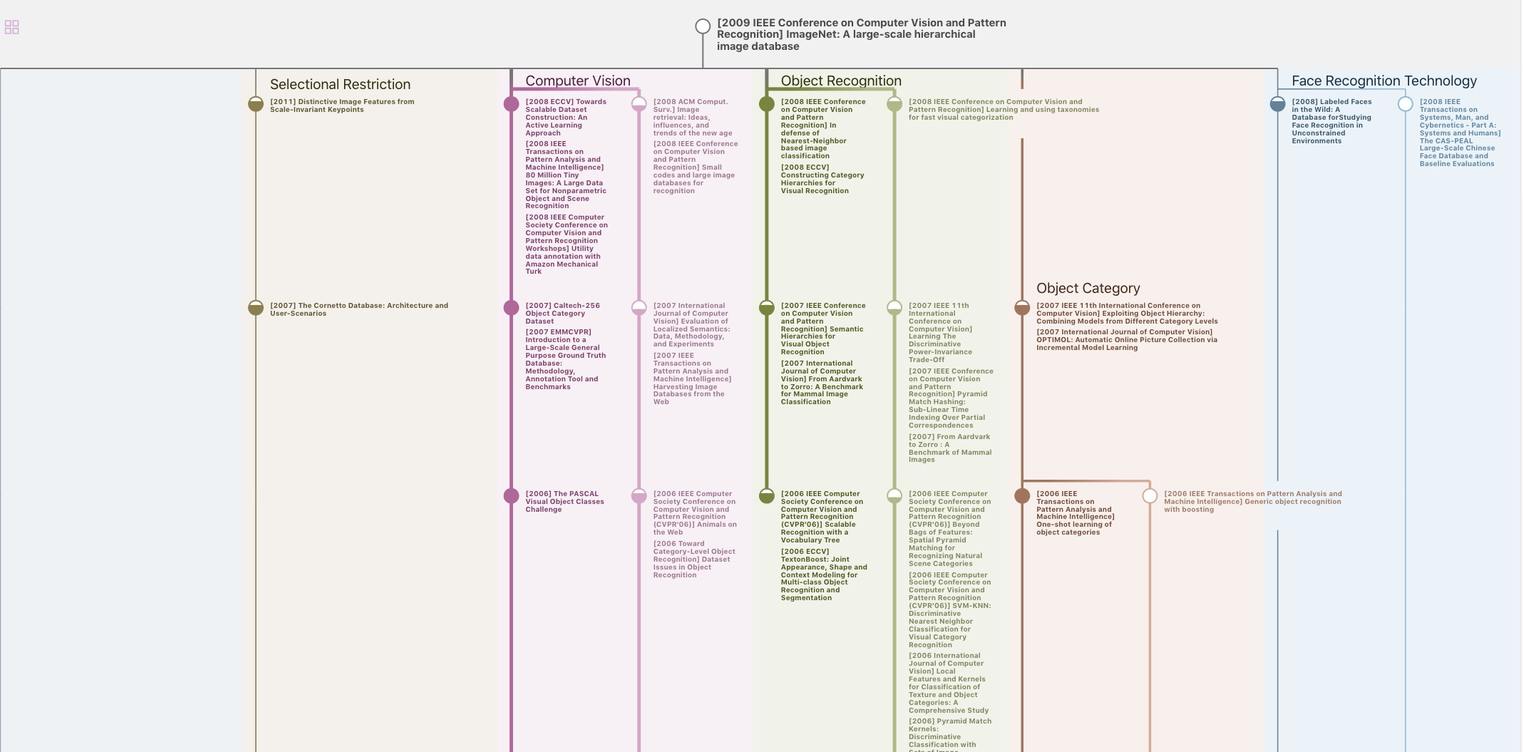
生成溯源树,研究论文发展脉络
Chat Paper
正在生成论文摘要