Identifiability of Ludwik's law parameters depending on the sample geometry via inverse identification procedure
COUPLED SYSTEMS MECHANICS(2022)
摘要
The accurate prediction of elastoplasticity under prescribed workloads is essential in the optimization of engineering structures. Mechanical experiments are carried out with the goal of obtaining reliable sets of material parameters for a chosen constitutive law via inverse identification. In this work, two sample geometries made of high strength steel plates were evaluated to determine the optimal configuration for the identification of Ludwik's nonlinear isotropic hardening law. Finite element model updating (FEMU) was used to calibrate the material parameters. FEMU computes the parameter changes based on the Hessian matrix, and the sensitivity fields that report changes of computed fields with respect to material parameter changes. A sensitivity analysis was performed to determine the influence of the sample geometry on parameter identifiability. It was concluded that the sample with thinned gauge region with a large curvature radius provided more reliable material parameters.
更多查看译文
关键词
full-field measurements, HARDOX 450, inverse identification, sample geometry, sensitivity analysis
AI 理解论文
溯源树
样例
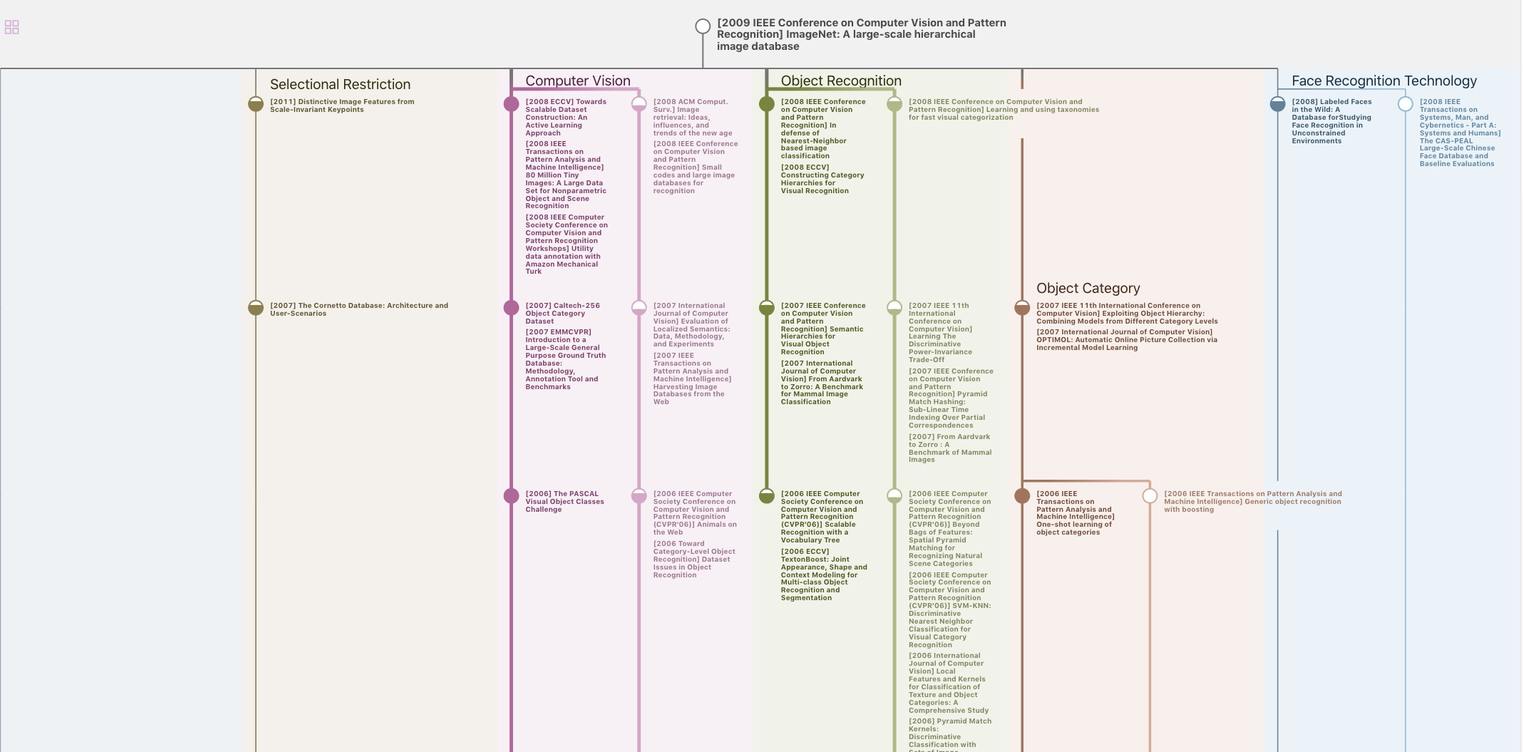
生成溯源树,研究论文发展脉络
Chat Paper
正在生成论文摘要