Optimal Task-Space Tracking With Minimum Manipulator Reconfiguration
IEEE ROBOTICS AND AUTOMATION LETTERS(2022)
摘要
An optimal solution to the task-space tracking problem using a non-redundant manipulator is proposed. This is a recurring occurrence in automated manufacturing settings, e.g. welding, deburring, painting, or quality control inspections. Given a pre-defined path for the end-effector to follow, there may not exist a joint-space continuous solution for task-space tracking when the non-linear manipulator kinematics and collision avoidance with obstacles in the workcell are considered. This introduces undesirable manipulator reconfigurations where the end-effector is required to deviate temporarily from the pre-defined path. The unwanted motion results in pausing task-space tracking, often incurring not only ineffective time and energy demands but potentially compromising the quality of the task at hand due to the additional discontinuities. An algorithm is proposed that provides a globally optimal perspective to the choice of suitable joint-space connected segments so that the minimum number of manipulator reconfigurations during task-space tracking is guaranteed. By carefully selecting the inverse kinematic solutions, all sequences ensuring minimum reconfigurability are proven collected by Dynamic Programming. Moreover, a faster greedy strategy is suggested to increase the computational efficiency of the tracker whilst still preserving global optimality and completeness. The effectiveness of the proposed algorithm is validated against traditional sampling-based solvers in simulation and illustrated on challenging real-world tracking experimentation with a Universal Robotics manipulator and a curved-surface object, depicted also in an accompanying video. An open-source implementation has also been provided for the benefit of the robotics community.
更多查看译文
关键词
Intergrated planning and control, motion control, manipulation planning
AI 理解论文
溯源树
样例
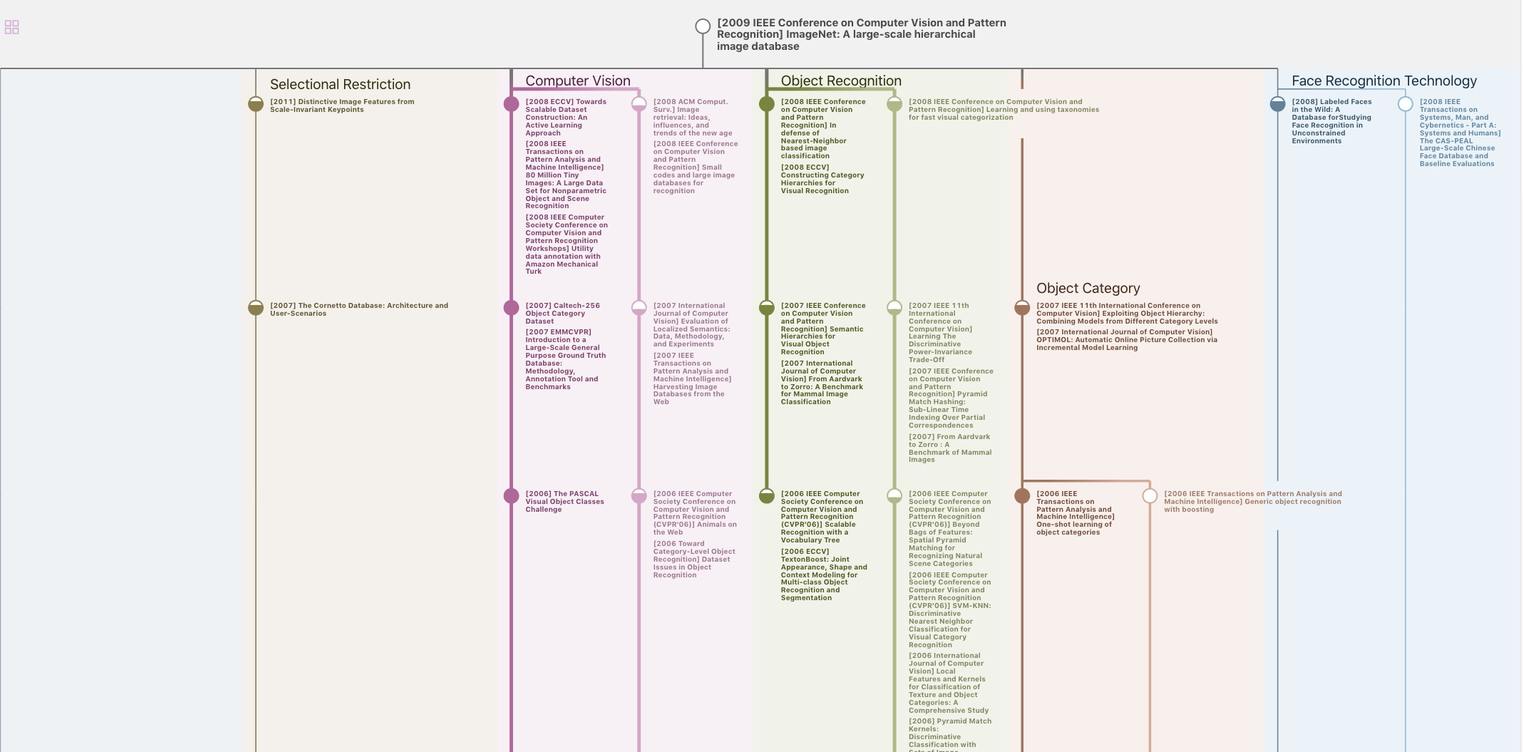
生成溯源树,研究论文发展脉络
Chat Paper
正在生成论文摘要