Improving the Corrosion Resistance of 6061 Aluminum Alloy Using Anodization and Nickel-Cobalt based Sealing Treatment
INTERNATIONAL JOURNAL OF ELECTROCHEMICAL SCIENCE(2021)
摘要
In this study, 6061 aluminum alloy was used as the substrate to form the oxide layer using room temperature and low temperature anodization treatment. The adhesion, corrosion resistance, micro structure, and mechanical properties of the oxide layer are studied. After anodization treatment, the hardness of the oxide layers are greater than 450 Hv, the highest hardness occurred at the oxide layer after nickel- cobalt sealing which hardness can reach 536 Hv. The thickness of the oxide layer formed by low temperature anodizing is about 45-50 mu m, and the thickness of the oxide layer formed by room temperature anodizing is only about 5-10 mu m. All aluminum anodization layers have contact angles above 60 degrees, and have high hardness, good hydrophobicity and high corrosion resistance. SEM, XPS, and TEM were used to analyze the chemical composition and microstructure of aluminum anodization layers prepared from different ratios of nickel and cobalt in the mixing solutions. The results show that when the ratio of nickel and cobalt is 8:2 in the mixing solutions, the aluminum anodization layer has the best sealing effect. When the substrates was carried out with anodization treatment and then sealed with the ratio of nickel- cobalt is 8:2, the lowest corrosion current density is 4.26 X 10(-9) A/cm(2). The corrosion current density of the substrates that was carried out with anodization treatment and then only sealed by boiling water is 3.55 X 10(-8) A/cm(2). When the substrates is only treated with anodization without sealing, its corrosion current density is only 5.8 X 10(-7) A/cm(2).
更多查看译文
关键词
6061 aluminum alloy, nickel-cobalt sealing, corrosion resistance
AI 理解论文
溯源树
样例
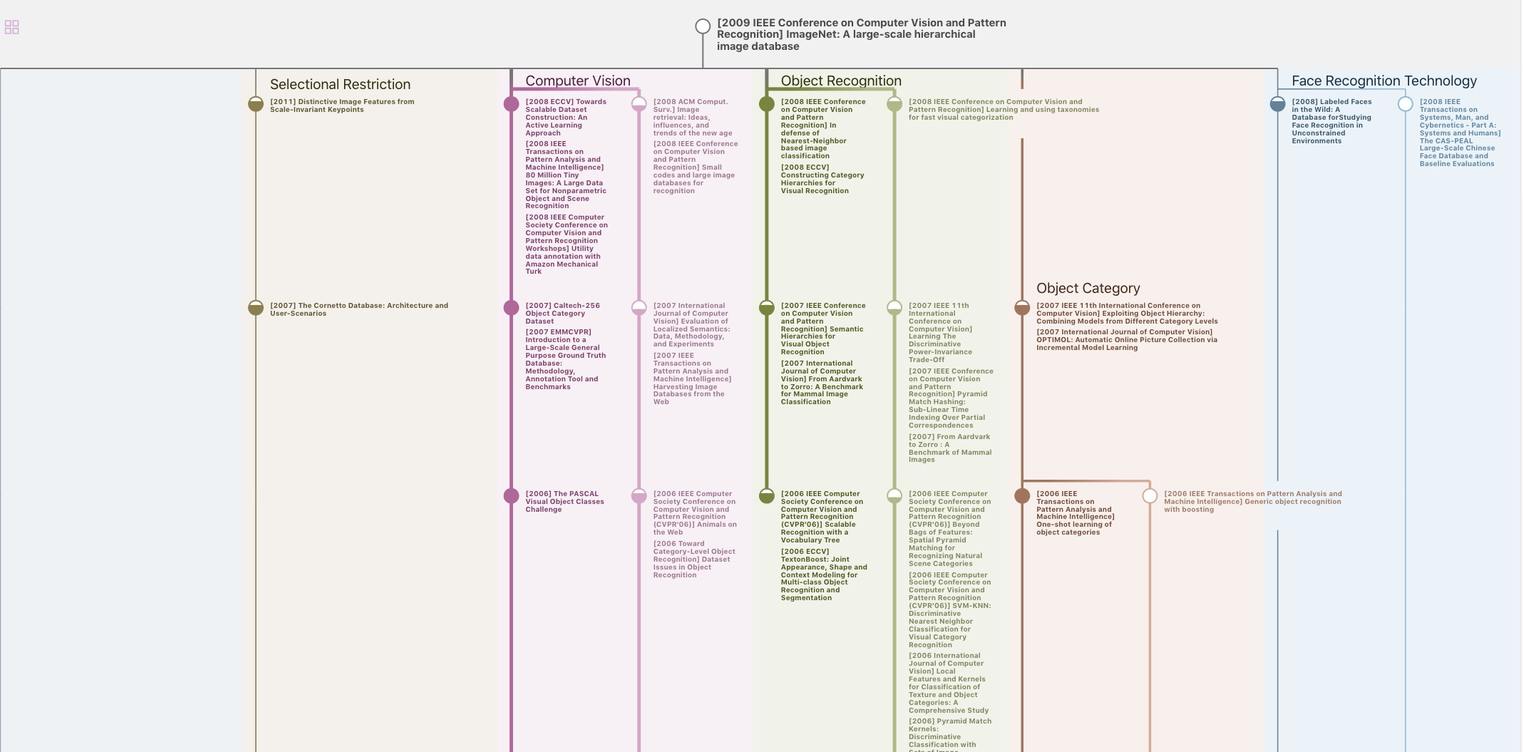
生成溯源树,研究论文发展脉络
Chat Paper
正在生成论文摘要