Development of low formaldehyde emitting particle board by nano particle reinforcement
semanticscholar(2021)
摘要
The wood panel industry depends on polycondensed thermosetting resins, of which urea formaldehyde is one of the most significant (Ciraci, 2005; and Lei et al., 2008). Particle board panels are created from wood particles and are a renewable bio resource. Particle board panels are commonly used in furniture and decoration, whereas plywood panels are mostly employed for structural purposes (Azambuja et al. 2018; Hameed et al. 2019; Hernández et al. 2020; Iždinský et al. 2020, Farah et al. 2021) Formaldehyde emission is an important feature to consider when purchasing wood panels for home usage. Formaldehyde has a recognised harmful effect on human health (Roffael, 2006; Salthammer et al., 2010 and Anonymous, 2012). Wood composite panels emit formaldehyde as a result of their formaldehydebased resin content, which is a disadvantage in many applications. The current glue industry's principal goal is to meet both of these needs by developing effective urea formaldehyde resin with very low, if not nil, formaldehyde emissions. Cademartori et al., (2019) added small percentages of aluminium oxide nanoparticles into UF resin rand investigated thermomechanical properties of the composites. They reported that aluminium oxide nanoparticles were effective to reduce the formaldehyde emission (14%) from MDF based on the results of the desiccator test. pMDI may be regarded as the most obvious formaldehyde-free adhesive candidate (Solt et al. 2019). For wood composite materials, nanoscience and nanotechnology offer several benefits. The use of nanotechnology in the production of particle board panels is critical in addressing the formaldehyde emission problem (Johnes et al., 2005; and Roughley, 2005). Throughout the last two decades, nanotechnology has been used Abstract Nanoscience and nanotechnology offer a plethora of possibilities for improving the qualities of wood composites. The present study aimed to use nanotechnology to develop low formaldehyde emitting particle board as ecologically acceptable composites. Conventional urea Formaldehyde resins were prepared by the percentage of second urea at 10%. Nano-wollastonite, silica and montomorillonite with the size range of 25-100 nm were applied at 0.5-2.0% based on the weight of resin. The nano-reinforced resins were admixed with suitable hardener and the panels were made. Formaldehyde emission reduction in wood panel products is critical and it can be partially controlled by using resin modification. The effectiveness of nanoparticle addition to reducing formaldehyde emission from wood particle board was examined by the perforator method as per IS 13745 (1993). Physical and Mechanical properties were evaluated according to IS 3087 (2005). The result indicated distinctly lower water absorption and thickness swelling of panels produced with 1.5 %, 1.5 % and 2.0 % nano silica, nano montomorillinite and nano wollastonite respectively. The results showed that static bending of the produced composite varied from 21.07 to 28.86 N/mm of MOR and from 2246 3353 N/mm of MOE; while internal bond strength (IB) varied from 0.35 to 0.58 N/mm. As per IS 3087 (2005) requirements, 1.5 % nano silica and montomorillonite and 2.0 % nano wollastonite mechanically modified urea formaldehyde based agro composites gave the best results for grade II particle boards. The study concluded that nanoparticle addition reduces the formaldehyde content in the panel without affecting the strength properties.
更多查看译文
AI 理解论文
溯源树
样例
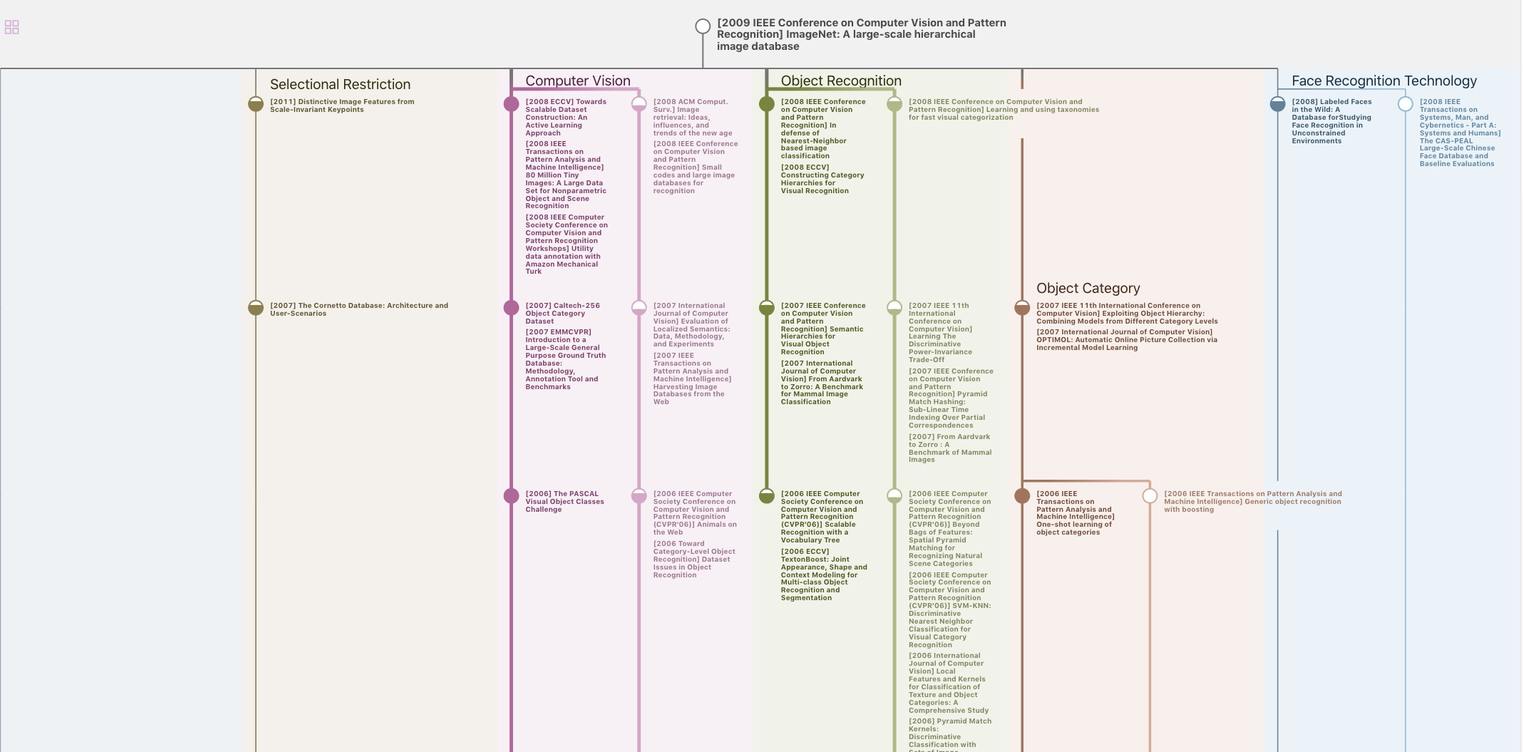
生成溯源树,研究论文发展脉络
Chat Paper
正在生成论文摘要