Hybrid microstructure-defect printability map in laser powder bed fusion additive manufacturing
Computational Materials Science(2022)
摘要
This work presents a methodology for predicting a hybrid microstructure and defect processing map for laser powder bed fusion (LPBF) additive manufacturing (AM). A finite element (FE) analysis based thermal model is coupled with a phase field model (PFM) in order to predict both defect formation and microstructure across the LPBF process parameter space. The parameter space is first categorized into defect regions such as keyholing, balling, and lack of fusion. These regions are predicted using the FE thermal model, allowing a defect map to be generated based on the geometries of the melt pools for a defined powder layer thickness. A region of the parameter space that leads to successful AM of defect-free parts is then identified. Segregation across the parameter space is predicted by an integrated computational model, which couples a finite interface dissipation PFM and the aforementioned FE thermal model. The parameter space is then separated into regions that result in cellular or planar microstructures based on the area fraction of cellular-dendritic segregation predicted within the melt pools. By merging the microstructure and defect maps, a hybrid microstructure-defect printability map is generated that distinguishes a process parameter region for fabricating defect-free parts with homogeneous microstructures. This hybrid map is validated with experimental observations for a Ni-5wt.%Nb alloy. The hybrid printability map can be used in the rapid selection and optimization of process parameters for additively manufacturing any alloy (provided models and their parameterization are available, and the alloy is printable), and can potentially help design alloys best suited for AM.
更多查看译文
关键词
Additive manufacturing,Selective laser melting,Printability map,Phase field model,Finite element
AI 理解论文
溯源树
样例
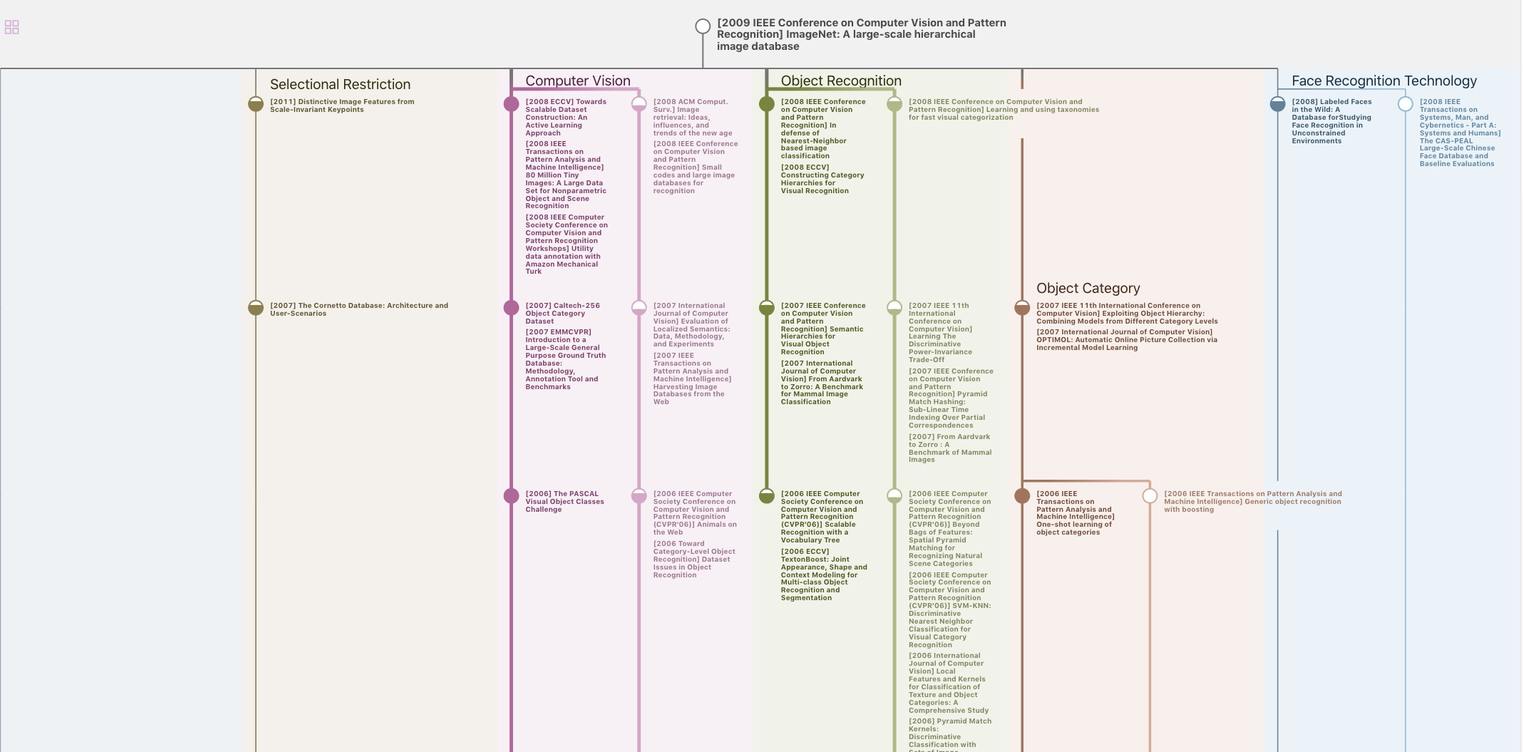
生成溯源树,研究论文发展脉络
Chat Paper
正在生成论文摘要