Numerical Study of the Percussive Riveting Process: Analysis Validation
Volume 2A: Advanced Manufacturing(2021)
摘要
Abstract This effort represents the continuation of percussive riveting work that has been performed by this University of Washington research group and presented at this event in the past. Percussive riveting is an assembly method that is used ubiquitously in the aerospace industry, especially in the fuselage final assembly phase. It is a dynamic assembly process that requires two entities operating simultaneously in order to form a rivet. One entity operates with a riveting gun on the exterior of the fuselage. The rivet gun provides the energy input to carry out the assembly process. The other entity operates with a bucking bar on the interior of the fuselage. This entity is responsible for forming the rivet from the shank end. In previous work undertaken by this research group, an axisymmetric thermomechanical finite element model (FEM) framework implementing actual boundary conditions was developed to understand the effect of geometric factors on the residual stress and strain distributions within the riveting stackup. A countersunk rivet and two skins are part of the riveting stackup. The countersunk rivet is widely used in the aerospace industry because of flushness requirements. Because no further joint finishing processes are required after the countersunk rivet has been formed, it is an economically viable final assembly method. Residual stress and strain distributions within the rivet stackup affect the fatigue performance of the assembled joint. The percussive riveting process is different from the conventional squeeze riveting process because of the dynamic and adiabatic nature of the percussive riveting process. Strain rate effects and thermal effects are negligible in the squeeze riveting process because of the low velocities and strain rates involved. But these two effects along with large strain magnitude play an influential role in the percussive riveting process. Because of the dynamic nature of the percussive assembly process, framework validation is important. A three-dimensional FEM (3DFEM) was constructed with asymmetric motion of the bucking bar, also known as the forming tool. The results of the 3DFEM simulation are compared with previously presented axisymmetric FEM and are presented in this study. Analysis validation of the axisymmetric FEM was performed and analysis results were compared with FEM results.
更多查看译文
关键词
Forming Process, Simulation
AI 理解论文
溯源树
样例
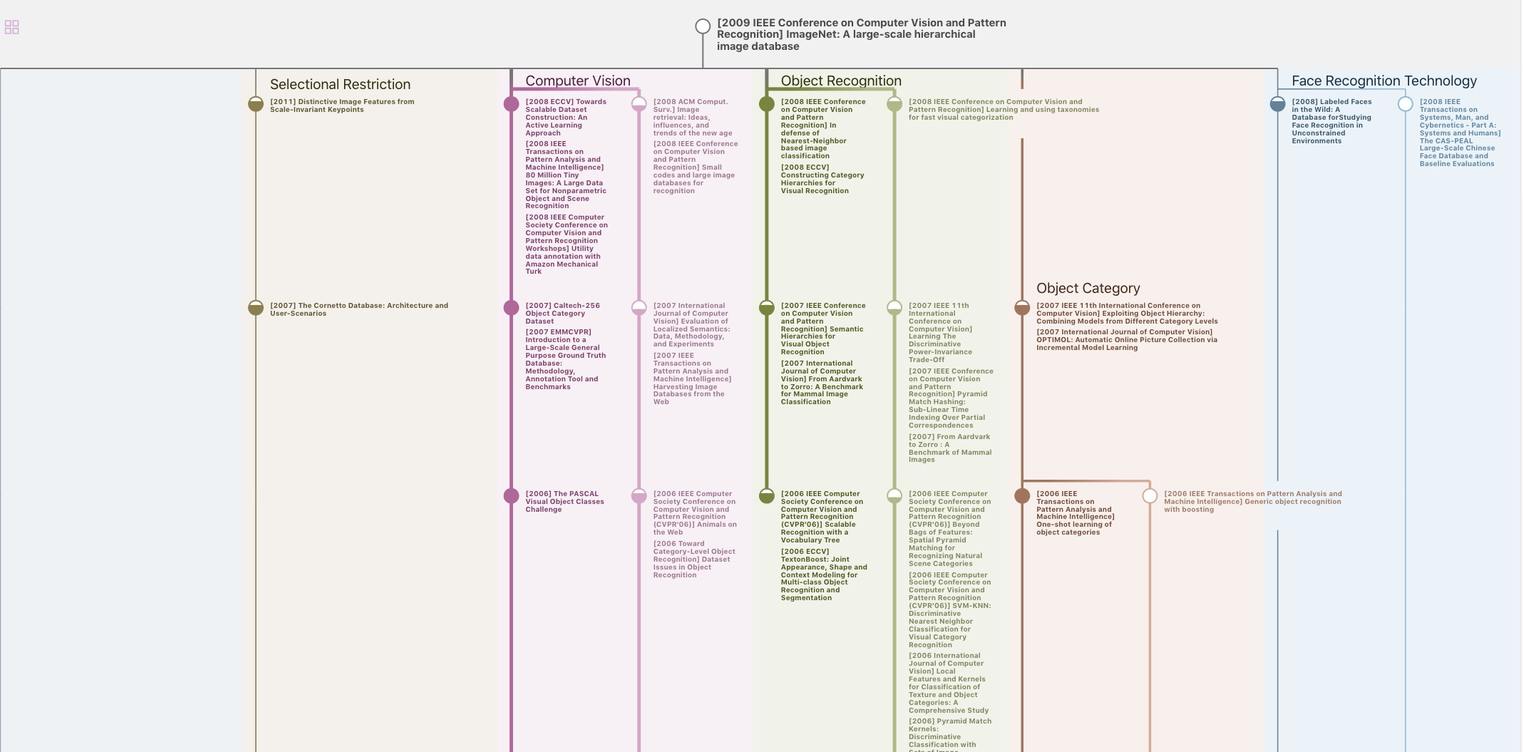
生成溯源树,研究论文发展脉络
Chat Paper
正在生成论文摘要