Laser Powder Feeding Additive Manufacturing of Ternary Blade with Abnormity Base Plane
Chinese Journal of Lasers(2022)
摘要
Objective Ternary blades are used in the impellers of aerospace turbojet engines, large-scale marine gas turbines, and automotive advanced turbine engines. The joints connecting the ternary blades to the impeller base are irregularly shaped surfaces. The ternary blade has special, complex, and spatial structure with a large inclination angle, large distortion, and other characteristics that conform to the ternary flow design theory; this design reduces energy loss when fluid travels through the impeller and improves its efficiency. Thus, ternary blade manufacturing has received considerable attention, and its unique structure imposes severe processing requirements. However, ternary blades are mainly processed by Computerized Numerical Control Electrical Discharge Machining (CNC EDM) and CNC milling; the number of materials eliminated during the processing is enormous, and the processing cycle is extensive. Laser additive manufacturing, a revolutionary type of forming technique, was proposed in the 1990s, which is used for efficient and moldless manufacturing of complicated structural elements. The research on laser additive manufacturing of ternary blades has significant practical applications. Currently, most multi-twisted blade formation, both home and abroad, is performed on a flat or cylindrical generatrix, and there are few reports on laser powder feeding additive manufacturing ternary blades on special-shaped base surfaces. The technique of streamline layering is proposed in this study, and the cladding formation of the ternary blade is effectively accomplished; this is based on the optical inner powder feeding cladding nozzle produced independently in the laboratory. Methods The three-element blades described in this study are curved in the flow direction and are three-dimensionally twisted, with complex twisting and tilting characteristics. The blade stacking substrate is a concave curved surface rather than a standard horizontal substrate. However, it is challenging to obtain information on each unit' s location and direction. The bottom of the three-element blade is an arc main base surface on the special-shaped base surface. Thus, this study proposes the following streamlined layering methods: first, the primary base surface is divided evenly in the radial direction to obtain circular arc slices perpendicular to the radial direction; second, the arc slices are divided equidistantly along the scanning direction to obtain the division unit; lastly, the vector formed by the centerline of the upper and lower planes of the division unit is used to determine the height and deflection direction. Further, when stacking, the nozzle' s axis aligns with the dividing unit' s direction; the cladding nozzle moves according to the division unit' s position and direction, and the final splicing obtains the formed part of the ternary blade. Results and Discussions To obtain segmentation units with varied structural characteristics, the streamline layering technique is developed for stacking the ternary blade' s forming parts [ Fig. 4 ( f )] . The homogeneous transformation matrix of each segmentation unit relative to the base coordinate system is determined through translation and rotation calculation, thus, determining the positional and directional information of each segmentation unit [Fig. 5( c) ] . Further, the laser cladding nozzle in this study is an optical internal powder-feeding nozzle, which is independently developed in the laboratory; the cladding nozzle is installed on a six-axis robotic arm. During cladding, the axis of the cladding nozzle aligns with the dividing unit's direction and fits along the curve. The single-layer arc slice cladding is completed by splicing the trajectory of each segmentation unit, and the multilayer arc slice overlaps to generate the ternary blade laser cladding, forming a portion with an enormous inclination, complex bending, and torsion structure (Fig. 7). Conclusions The streamline layering technique is proposed in this study to tackle the ternary blade laser cladding formation trajectory problem. The main base surface is evenly spaced along the radial direction to obtain arc slices perpendicular to the radial direction, which are then evenly spaced along the scanning direction to obtain the segmentation unit. The streamlined layering technique is proposed in this study to solve the problem of ternary blade structural parts layering, bending, and inclination, and to accomplish the accumulation of ternary blade forming parts. The inspection results of the formed parts are as follows: the surface of the ternary blade-formed parts is smooth, and the average surface roughness value is less than 4.065 mu m, which effectively reduces the step effect; it achieves a good metallurgical combination with the irregular base surface, and the average thickness of the formed parts is 5.97 mm. The relative errors of thickness and torsion angle are from -1. 4% to 1. 03% and - 4. 67% , respectively. The forming accuracy is high. The heat accumulation at the laser molten pool is evident as the height of the formed part increases. Further, the microhardness reduces as the microstructure increases; the microhardness of the formed part ranges from 348. 3 to 360. 4 HV, and the metallographic structure is uniformly dense with no evident holes or cracks.
更多查看译文
关键词
laser technique, inside-laser powder feeding, streamline layering, ternary blade
AI 理解论文
溯源树
样例
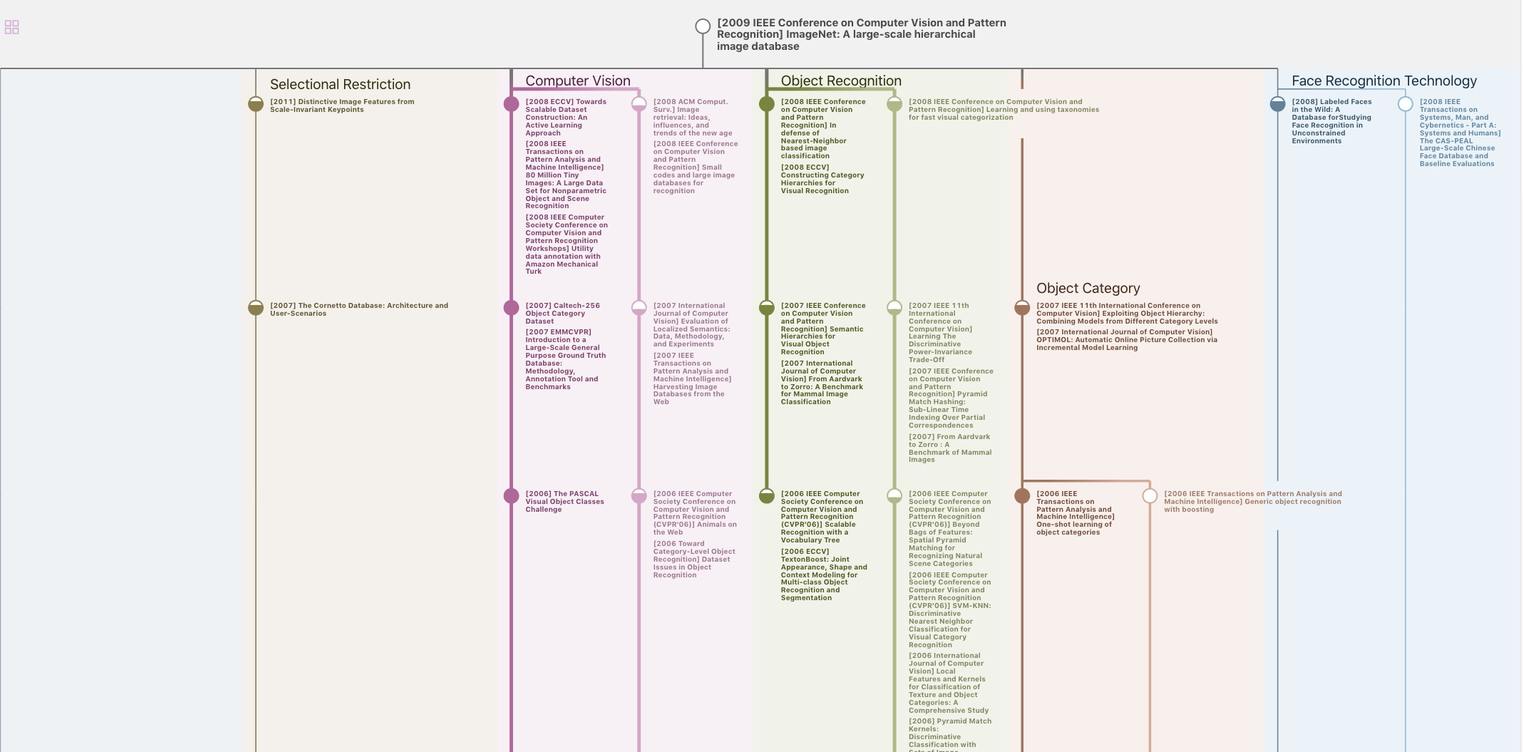
生成溯源树,研究论文发展脉络
Chat Paper
正在生成论文摘要