Numerical investigation of the influence of multiple loads on material modifications during hard milling
Procedia CIRP(2021)
摘要
Abstract Understanding the effect of finishing processes on the surface integrity of the workpiece is crucial for the creation of defined functional characteristics in workpieces. The measurement-based determination of the material loads requires a high effort and can only be done selectively. In this paper a numerical approach utilizing the FE software Abaqus according to the CEL method is presented for hard milling. Particular attention was paid to the changing geometrical conditions, contact conditions and material states as well as load distributions during each single cut. A model which represents the single cut of the cutting edge engagement with defined geometry is able to calculate equivalent internal loads. Due to the formation of an affected zone as a result of discontinuous thermo-mechanical loads, the cutting is performed in a material with changed material properties during the following cut. A correlation between previous and subsequent thermal and mechanical loads and their influence on the accumulated plastic strain and accumulated heat input into the workpiece was determined. For the discontinuous cutting edge engagements an affected zone was determined. The material loads are typically space and time dependent. The varied cutting edge acting as load in a three-dimensional FE-model was determined inversely by comparing measured and simulated material modifications. A correlation between material loads and material modifications in the form of accumulated thermally and mechanically induced strains was found, which is used to predict surface and sub-surface properties.
更多查看译文
关键词
hard milling,surface integrity,simulation
AI 理解论文
溯源树
样例
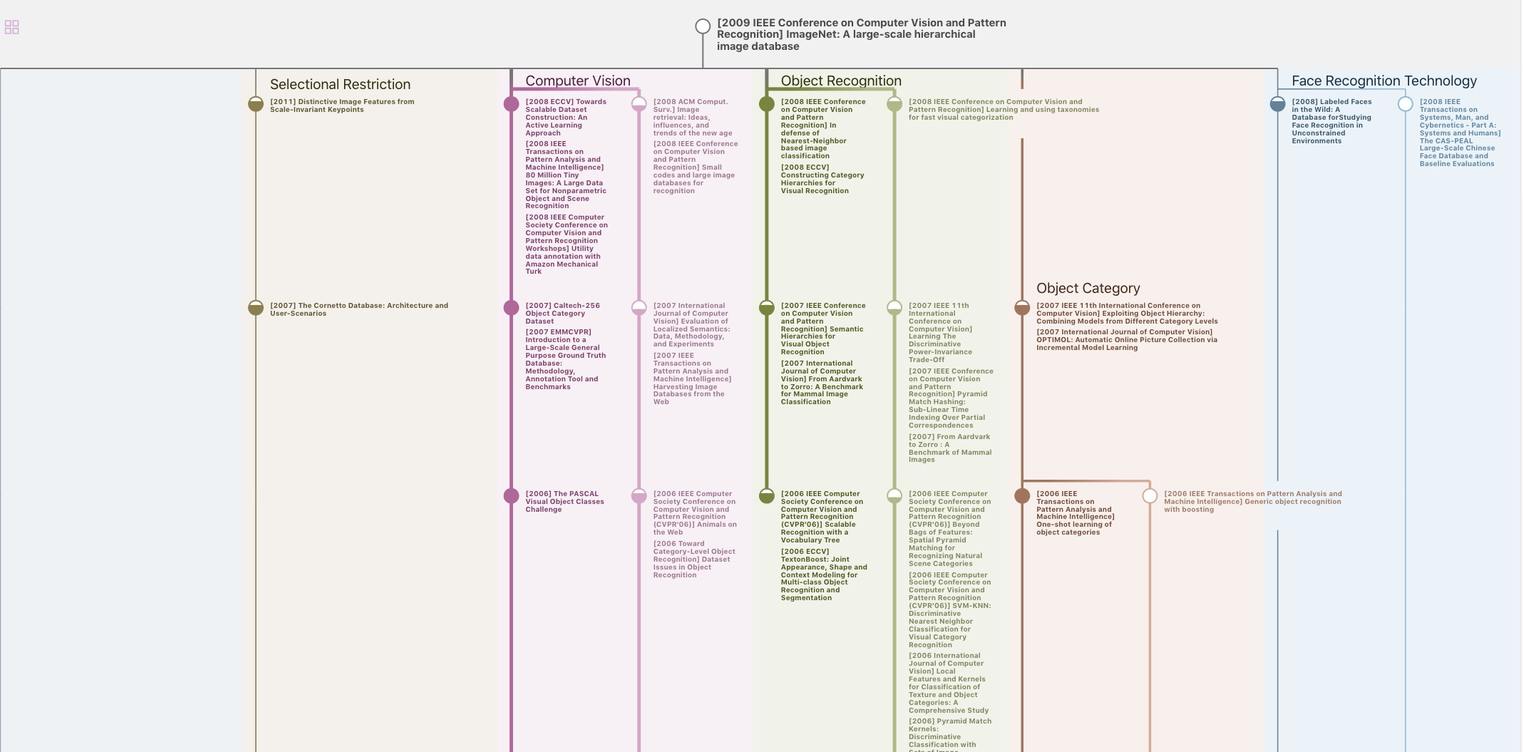
生成溯源树,研究论文发展脉络
Chat Paper
正在生成论文摘要