Evaporative Cooling for Polymer Electrolyte Fuel Cells – a Model Based System Level Analysis
ECS Meeting Abstracts(2021)
摘要
Polymer electrolyte fuel cells (PEFC) are a promising alternative to conventional propulsion systems since they reach peak system efficiencies above 60 % [1] and power densities of more than 640 W/L [2]. State-of-the-art PEFC system power densities are almost in accordance with U.S. Department of Energy 2020 targets (650 W/L), however, to reach the ultimate target of 850 W/L, a substantial decrease in system volume is required [3].In a conventional PEFC, the cooling system contributes significantly to stack and system volume. The state-of-the-art cooling solution aims at transferring the waste heat to a liquid coolant that flows through separate cooling channels in the bipolar plates. Therefore, a complex multi-layer design of bipolar plates is required [4] which contributes to about 75 % of stack volume and approximately 80 % of its mass [5]. The coolant is subsequently chilled in an external heat exchanger which requires a high surface area due to the small temperature gradient and thus shows a high volume demand.In order to facilitate the heat transfer, high stack operating temperatures are necessary. However, to ensure a proper humidification and thus ionic conductivity of the proton exchange membrane [6] at elevated temperatures, an external humidifier is often required which contributes substantially to the system volume.As an auspicious alternative, evaporative cooling can contribute to reach the ultimate power density target, since it shows the potential to reduce the stack volume, mass, complexity and cost up to 30 % by simplifying the design of bipolar plates [7]. Additionally, it allows a better internal humidification which enables higher operating temperatures without an external humidifier.In our concept, liquid water is fed to each cell through dedicated water channels in the anode flow-field. Subsequently, the water is distributed in a specially designed gas diffusion layer with a mixed hydrophilic and hydrophobic pattern (Figure 1) [8]. Once in contact with the gas flow, the water in the hydrophilic lines evaporates, cools the cell by taking up the heat of evaporation and is eventually released as vapor with the exhaust gases.Our previous work [9] has proven, that sufficient cooling power can be provided by evaporative cooling. Main findings showed, that the evaporation rate and thus the cooling power increases with temperature as well as cathode stoichiometry and decreases with system pressure (Figure 2). On the other hand, operating conditions show a significant impact on stack performance and power consumption of balance of plant (BoP).Therefore, a zero-dimensional fuel cell system model has been developed in the present work to analyze interactions between BoP and the fuel cell stack in an evaporatively cooled system. From the analysis of the power demand of the air compressor and the stack power, optimal operating conditions are elaborated in order to maximize the net system power. Simulation results show that the temperature has only limited impact at low current densities, whereas the peak system power decreases with temperature. Acomparison between conventional and evaporative cooling shows no significant performance difference at 70 °C but a slight decrease in peak power for evaporative cooling at 90 °C. However, since the heat rejection of conventional cooling systems is typically limited to about 1.45 kW/K [3], evaporative cooling shows the additional benefit of an increased peak power (Figure 3).In addition, a system efficiency map for evaporative cooling has been calculated (Figure 4) which shows that the highest efficiencies can be reached at low pressure (1 to 1.5 bar), medium to high temperature (70 °C to 90 °C) and low cathode stoichiometry (2 to 3), similar to a conventionally cooled system.Further, the water balance of an evaporatively cooled fuel cell system has been investigated and main findings show, that a sufficient amount of water can be retained from the exhaust gas at condenser outlet temperatures below 60 °C to supply sufficient water to the stack.References:[1] M. Matsunaga, et al., Honda R&D Technical Review 21 (2009), 1, 7[2] J. Juriga, presentation, Hydrogen and Fuel Cells Technical Advisory Committee Meeting, 2012[3] U.S. Department of Energy, Multi-Year Research, Development, and Demonstration Plan, Fuel Cells, 2017[4] G. Zhang, S.G. Kandlikar, Int J Hydrogen Energ 37 (2012), 2412[5] A De las Heras, et al., Renew Sust Energ Rev, 96 (2018), 29[6] A. Kusoglu, A.Z. Weber, Chem Rev 117 (2017), 987[7] A. Fly, R.H. Thring, Int J Hydrogen Energ 41 (2016), 14217[8] M. Cochet, et al., Fuel Cells 18 (2018), 5, 619[9] M. Striednig et al., presentation, European Fuel Cell Forum, Lucerne, Switzerland, 2019Figure 1
更多查看译文
AI 理解论文
溯源树
样例
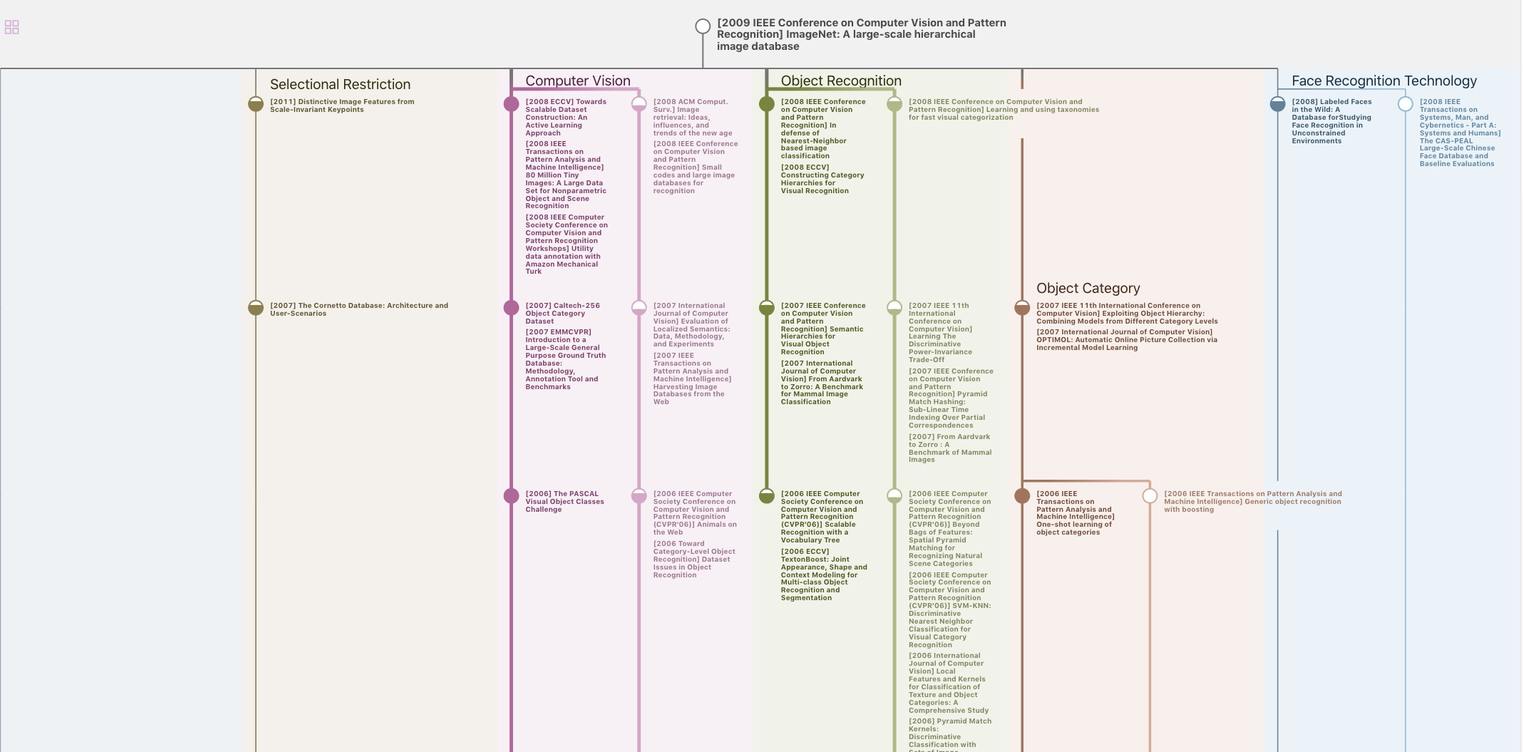
生成溯源树,研究论文发展脉络
Chat Paper
正在生成论文摘要