In situ tomographic study of a 3D-woven SiC/SiC composite part subjected to severe thermo-mechanical loads
JOURNAL OF SYNCHROTRON RADIATION(2022)
摘要
A high-temperature multi-axial test is carried out to characterize the thermomechanical behaviour of a 3D-woven SiC/SiC composite aeronautical part under loads representative of operating conditions. The sample is L-shaped and cut out from the part. It is subjected to severe thermal gradients and a superimposed mechanical load that progressively increases up to the first damage. The sample shape and its associated microstructure, the heterogeneity of the stress field and the limited accessibility to regions susceptible to damage require non-contact imaging modalities. An in situ experiment, conducted with a dedicated testing machine at the SOLEIL synchrotron facility, provides the sample microstructure from computed micro-tomographic imaging and thermal loads from infrared thermography. Experimental constraints lead to non-ideal acquisition conditions for both measurement modalities. This article details the procedure of correcting artefacts to use the volumes for quantitative exploitation (i.e. full-field measurement, model validation and identification). After proper processing, despite its complexity, the in situ experiment provides high-quality data about a part under realistic operating conditions. The influence of the mesostructure on fracture phenomena can be inferred from the tomography in the damaged state. Experiments show that the localization of damage initiation is driven by the geometry, while the woven structure moderates the crack propagation. This study widens the scope of in situ thermomechanical experiments to more complex loading states, closer to in-service conditions.
更多查看译文
关键词
X-ray micro-tomography, image processing, ceramic matrix composite (CMC), thermo-mechanical loading, multi-axial loading
AI 理解论文
溯源树
样例
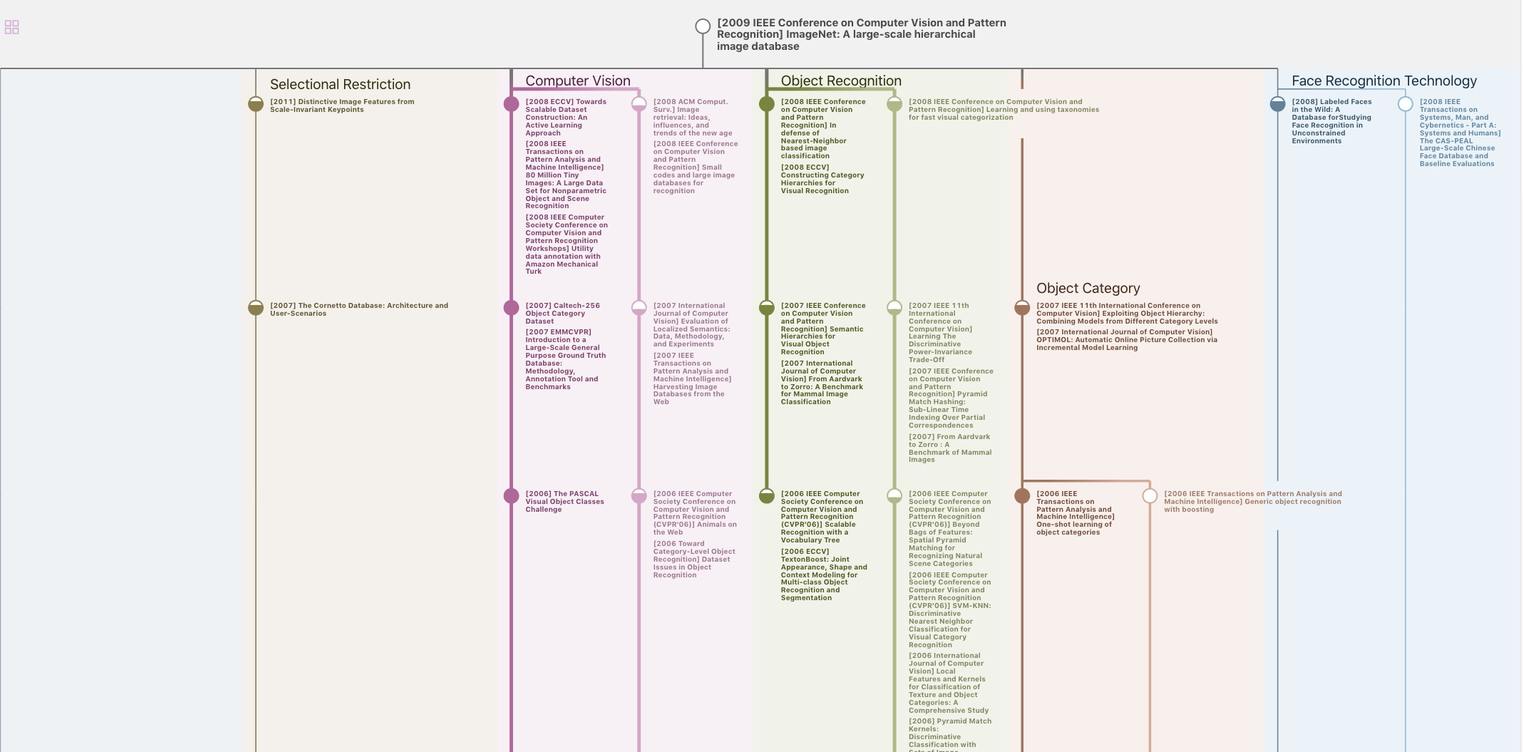
生成溯源树,研究论文发展脉络
Chat Paper
正在生成论文摘要