Load Line Displacement Partitioning in Creep Crack Growth Analyses of 316H Stainless Steel
Volume 6A: Materials and Fabrication(2018)
摘要
Accelerated creep crack growth tests in the laboratory can lead to greater levels of plasticity at the tip of a creep crack than would be experienced in service. This is problematic when trying to determine C* which is used to model the stress field ahead of a crack. Deflection partitioning methods must be used in order to determine the contribution to the load line displacement rate as a result of creep which in turn is used to calculate C*. This partitioning can lead to negative values of the creep load line displacement rate due to the high contribution from plasticity. The amount of assumed plasticity is likely to be erroneously high as it is currently assumed that the material behaviour fits a Ramberg-Osgood model, when in reality such a fit does not predict the behaviour well over a large range of stress. This work compares the load line displacement determined from solutions based on a Ramberg-Osgood model with those calculated from finite element simulations using uniaxial tensile data to model the plasticity. The simulations formulated crack growth by means of a crack length vs time criterion using experimental crack growth data. It is found that the theoretical solutions do over predict the amount of plastic deformation compared to the numerical results. It is also found that for the short term test considered, the load-line displacement due to creep deformation was small compared to that from crack growth.
更多查看译文
AI 理解论文
溯源树
样例
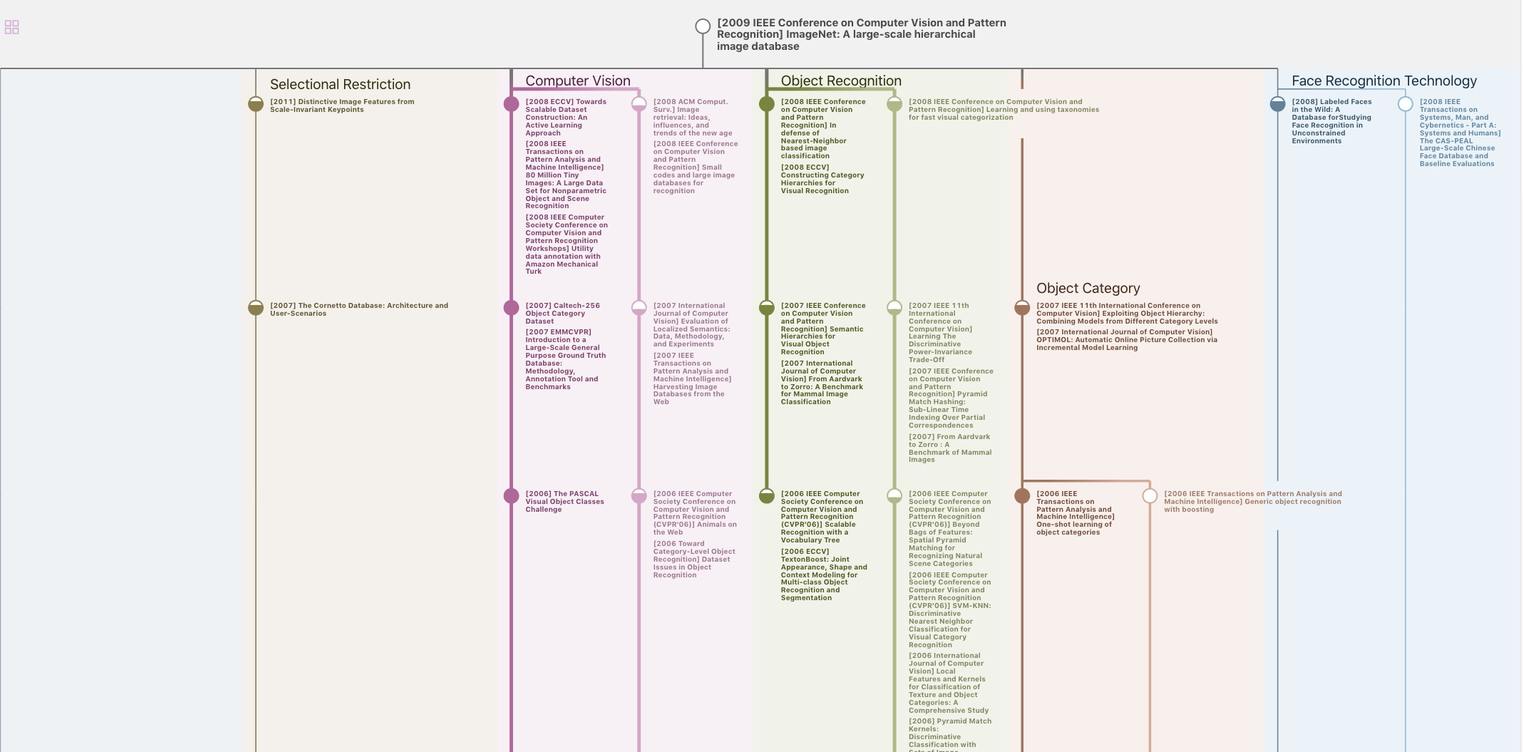
生成溯源树,研究论文发展脉络
Chat Paper
正在生成论文摘要