Development of Localized Compressive Hydrostatic Pressure-assisted Cutting Method: Cutting Experiment and Molecular Dynamics Simulation using Sliding Element
semanticscholar(2017)
摘要
Improving machined surface integrity is one of the most important issues in the precision machining. This study is aiming at developing a cutting tool, which enables to generate a localized compressive hydrostatic stress field around the cutting point to improve machined surface integrity without causing unnecessary plastic deformation. In this report, a cutting tool equipped with a sliding element for giving a localized hydrostatic pressure field was fabricated using information obtained through the previously performed molecular dynamics simulation, and a turning experiment was conducted on a pure aluminum workpiece. As a result, reduction in burr formation around the cutting groove shoulder was confirmed as observed in the molecular dynamics simulation result. Introduction In the metal cutting processes, unnecessary deformations such as the burr formation occurs in the machined surface and subsurface, because such a process is mainly achieved by the plastic deformations, and it also leads to the source of the residual stresses. Therefore, suppression of such unnecessary plastic deformations is considerable importantance. By the way, it is known that hydrostatic pressure does not concern the plastic deformations [1], although it affects the deformation behaviors of metals. The yield stress and the ductility of metals increase under a high compressive hydrostatic pressure [2]. A high compressive hydrostatic pressure also reduces the density of lattice defect such as voids and cracks, and inactivates the mobility of workpiece atoms [3]. These characteristics are expected to improve the machined surface qualities. Hence, some papers have reported that an improvement in the machined surface integrity can be realized when the cutting is conducted under a high compressive hydrostatic pressure [4, 5]. However, relatively large equipment should be utilized to give such a high pressure to the workpiece, and it has been an issue for practical use. Under such circumstances, a cutting method by making use of localized hydrostatic stress has been developed by just using a simple cutting tool attached with a planer jig using the molecular dynamics simulation (MD) [6 8]. In this report, an actual cutting tool was developed and a turning experiment was conducted on a pure aluminum workpiece. A molecular dynamics simulation was also performed for comparison. Localized Compressive Hydrostatic Pressure-assisted Cutting Experiment Developed Cutting Model and Experimental Procedure. Figures 1(a) and (b) illustrate the cross-sectional view of proposed cutting process and the Mohr's stress circle describing inner stress condition when using the proposed cutting tool, respectively [7]. The cutting tool shown in Fig. 1(a) is intended to introduce a high compressive hydrostatic stress field around the cutting point easily by 293 Proceedings of the 20th International Symposium on Advances in Abrasive Technology 3-6 December, Okinawa, Japan
更多查看译文
AI 理解论文
溯源树
样例
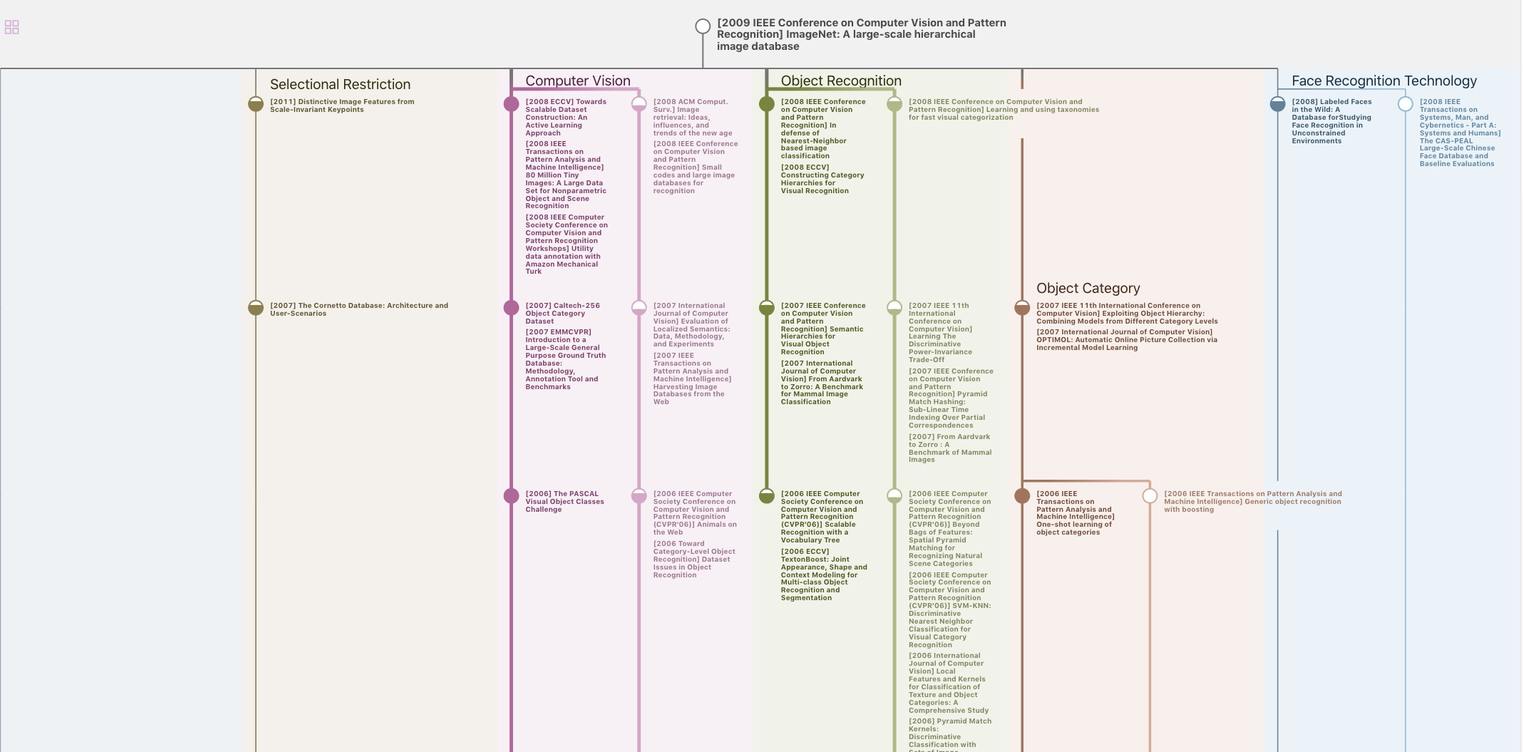
生成溯源树,研究论文发展脉络
Chat Paper
正在生成论文摘要