Incorporating Tool Contact Considerations in Tool-Path Planning for Robotic Operations
Volume 1: Additive Manufacturing; Advanced Materials Manufacturing; Biomanufacturing; Life Cycle Engineering; Manufacturing Equipment and Automation(2021)
摘要
Abstract Tool-Path planning is the foundation for automating many manufacturing processes. Robotic manipulators are increasingly being considered to automate tasks that require complex tool motions. Robotic manipulators provide extra degrees of freedom and are more flexible than traditional automation technologies. However, a tool-path needs to be planned and given to the manipulator trajectory generator as input. The traditional tool-path planning considers the tool to have one contact point, known as the Tool Center Point (TCP). This underutilizes the available flexibility of the manipulator. To make use of the manipulator’s flexibility, multiple contact points or multiple TCPs can be considered. These tool contact considerations make the tool path planning problem complex and computationally challenging. In this paper, we present a novel tool path planning algorithm. Our algorithm incorporates the multiple tool contact points consideration during tool-path planning in an efficient manner to generate a high-quality tool-path in a reasonable amount of run time. We evaluated our algorithm on four different test cases. The test cases include the parts with complex geometry and tools which can have surface area for establishing contacts with the part. In these test cases, a traditional single contact tool-path will not work due to geometric constraints, and multiple tool contacts make the problem challenging. Our algorithm was able to generate tool-paths for these four test cases successfully.
更多查看译文
AI 理解论文
溯源树
样例
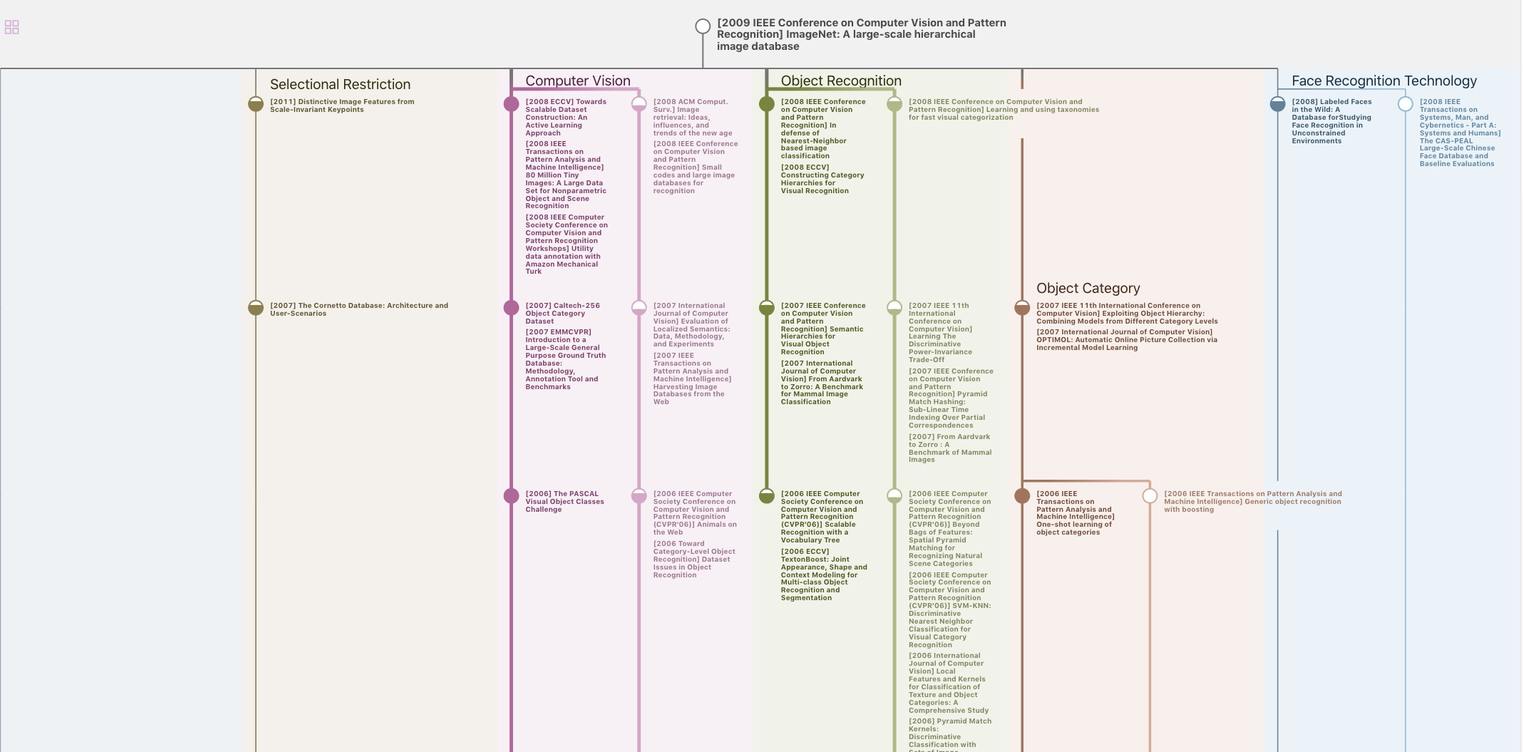
生成溯源树,研究论文发展脉络
Chat Paper
正在生成论文摘要