Failure mechanism of omega-shape 3D orthogonal woven composite component under transverse low-velocity impact and subsequent axial compression load
INTERNATIONAL JOURNAL OF DAMAGE MECHANICS(2022)
摘要
Failure mechanism of complex profile component is always different from that of conventional plate counterpart due to the coupling effect of material and structure. In this work, the low-velocity impact (LVI) and compression after impact (CAI) behaviors of omega-shape hybrid carbon/Kevlar 3 D orthogonal woven (3DOW) composite made for vehicle B-pillar were comprehensively studied by mechanical tests and mesoscale finite element (FE) analysis at component level, high-speed infrared (IR) thermal imaging, acoustic emission (AE) detection, and microscopic damage morphology characterization. It is found that a through-thickness stress concentration ring leads to high stress state and damage zone penetrating from the impact side to non-impact side along the ring path instead of at the lowest impactor position. The slope effect can not only help the stress conduction downward, but also inhibit the damage propagation from the impact side to the slope. Impact-induced cracks are concentrated around the R corners and extended along the axial direction of the specimen, forming the strip-shaped damage concentration zone along the upper eave of the slope. The Progressive Top-Down Crushing (PTDC) mode of compression after impact is due to the complex deformation process of each yarn such as squeezing, folding and eversion in the crushing process from the top of specimen. And the Middle Indentation Fracture (MIF) mode is the result of bending instability and abrupt fracture. This work presents a reference significance for the further development of composite strengthening components in vehicle bodywork.
更多查看译文
关键词
3D orthogonal woven, low-velocity impact, compression after impact, damage mechanics, finite element analysis
AI 理解论文
溯源树
样例
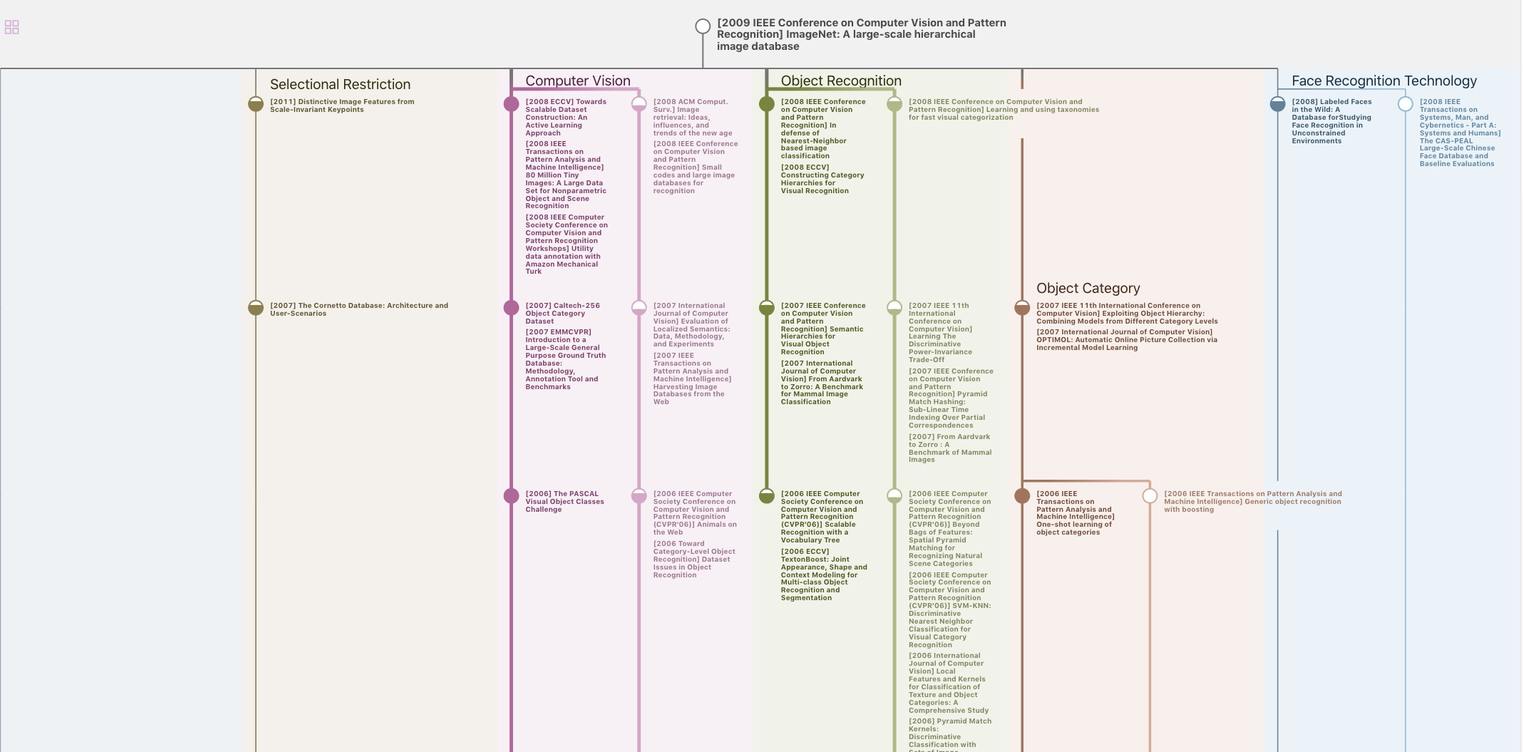
生成溯源树,研究论文发展脉络
Chat Paper
正在生成论文摘要