A Trial Toward Sub-100 Nm Motion Error Compensation Of Ultra-Precision Machine Tool Using On-Machine Metrology System With Chromatic Confocal Probe
JOURNAL OF ADVANCED MECHANICAL DESIGN SYSTEMS AND MANUFACTURING(2021)
摘要
Aspherical or free-form optical surface machining using an ultra-precision machine tool is a common and effective method used in the manufacturing of precision optics. However, this method sometimes causes waviness due to mid-spatial frequency (MSF) motion errors of the machine. This waviness lowers the quality of the optical surface. To compensate for the motion error, we use the waviness of the motion error of the axial displacement of an ultra-precision machine tool. This waviness is obtained by a non-contact on-machine metrology (OMM) system that measures an optical flat as a reference. The OMM system consists of a displacement probe and a machine tool axis position capture device. The probe system uses a chromatic confocal probe on an ultra-precision machine tool to evaluate the form deviation of the workpiece with 1-nm resolution. The axis position capture system uses a linear-scale signal branch circuit on each axis of the ultra-precision machine tool. The OMM system is tested in terms of accuracy and repeatability. Through shaper cutting experiments of an oxygen-free copper (OFC) workpiece with feed-forward motion error compensation, we reduce the peak-to-valley (p-v) profile error from 125.3 nm to 42.1 nm.
更多查看译文
关键词
On-machine measurement, Ultra-precision machine tool, Chromatic confocal probe, Feed forward compensation machining, Motion error compensation
AI 理解论文
溯源树
样例
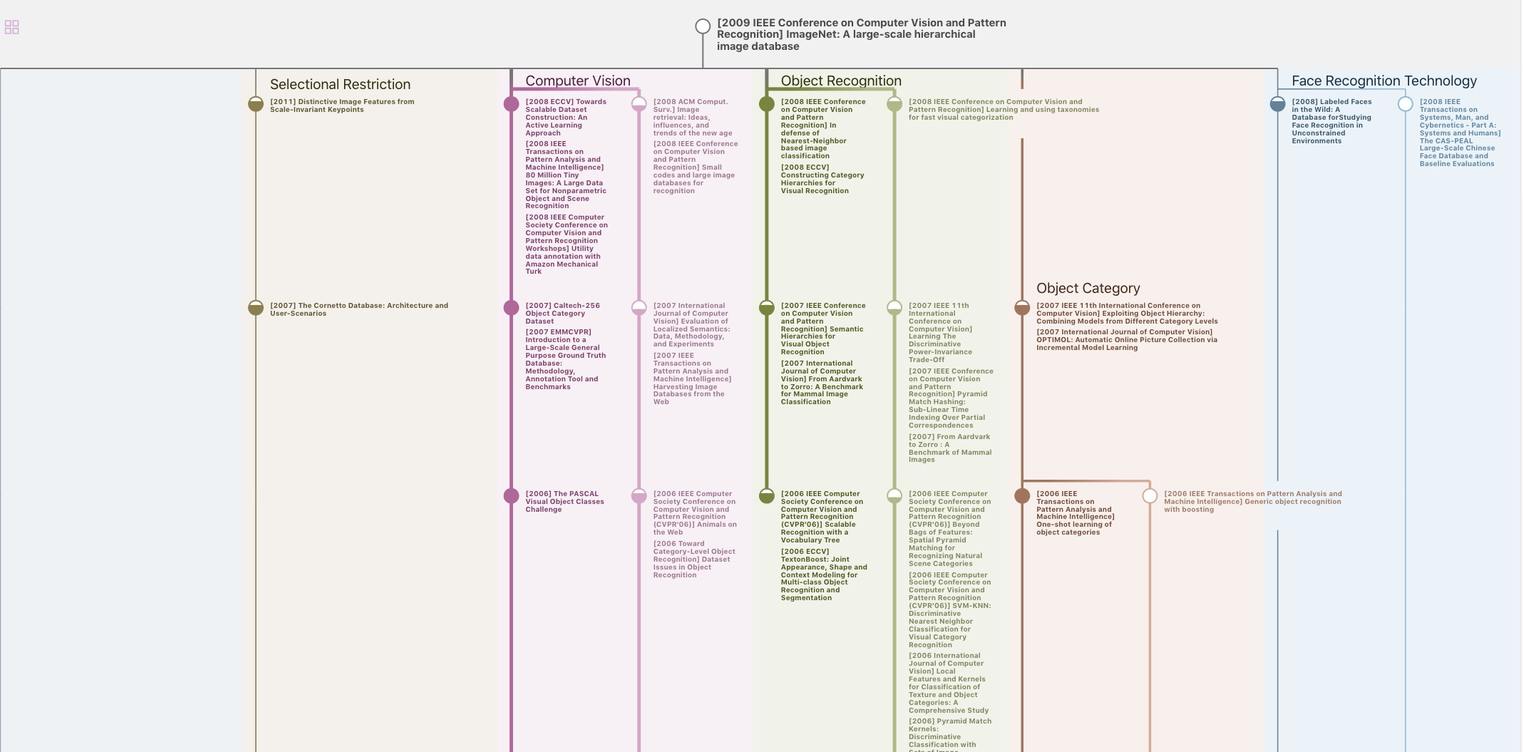
生成溯源树,研究论文发展脉络
Chat Paper
正在生成论文摘要