Analysis of the interdependent relationship between porosity, deformation, and crack growth during compression loading of LPBF AlSi10Mg
Materials Science and Engineering: A(2022)
摘要
For parts loaded in tension and shear, it is clear that voids created during manufacturing generally decrease part strength and ductility. This study examines how these manufacturing defects affect the mechanical performance of laser powder bed fusion (LPBF) AlSi10Mg specimens loaded in compression. Cylindrical samples of LPBF AlSi10Mg with varying levels of porosity and different microstructures were loaded in-situ in compression and characterized using X-ray computed tomography (XCT). Bulk porosity influenced the mechanical behavior of LPBF AlSi10Mg parts loaded in compression, with increasing porosity leading to decreasing yield strength, ultimate strength, and part ductility. However, bulk porosity did not influence the failure mode of the material during compression. Instead, microstructural changes caused by different heat treatments were the determining factor as to whether a part would fail via a critical shear crack or slowly collapse during loading. Data suggests that as bulk porosity increased, the strain required to propagate a crack from nucleation to catastrophic part failure also increased. Based on observations from XCT data, we hypothesize that large pores in the microstructure blunted the growing crack. These results suggest that, by increasing the resilience of LPBF AlSi10Mg parts loaded in compression, porosity may enhance certain desirable properties of LPBF parts during compressive loading.
更多查看译文
关键词
Additive manufacturing,Laser powder bed fusion,AlSi10Mg,Porosity,Failure mechanisms,Shear cracking,Compression,Microstructure,Heat treatment
AI 理解论文
溯源树
样例
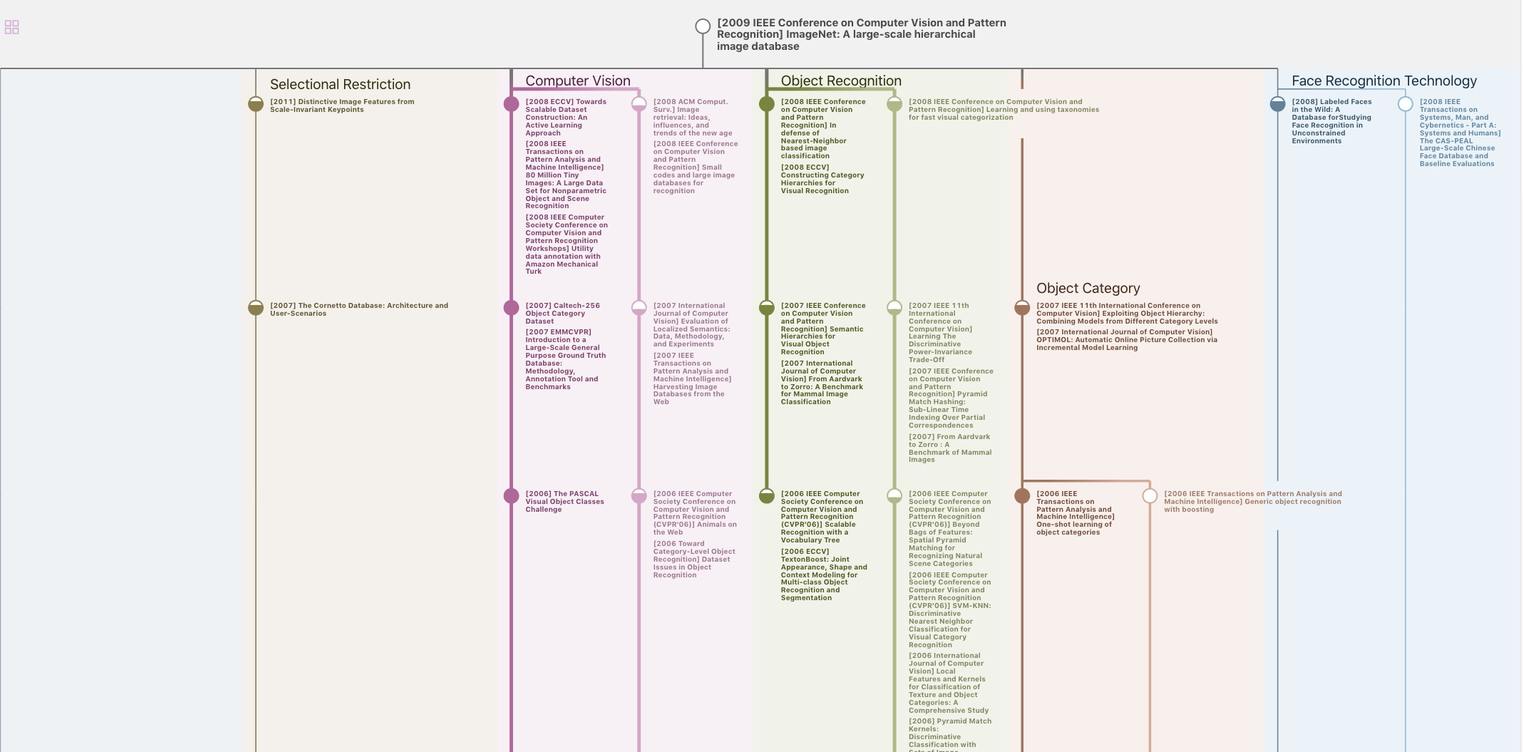
生成溯源树,研究论文发展脉络
Chat Paper
正在生成论文摘要