Identification of practical spindle-tool interface parameters using an optimization based statistical approach
SADHANA-ACADEMY PROCEEDINGS IN ENGINEERING SCIENCES(2021)
摘要
The dynamic performance of a high-speed machine tool spindle primarily depends on the rigidity between the spindle-holder couplings. The machining stability of such system is determined by the rigidity at the tapered portion of the coupled joints. This paper presents a methodology to evaluate tool-tip frequency response function (FRF) by considering the tool holder-spindle interface stiffness using finite element analysis. Furthermore, a comparative analysis is carried out on the spindle-tool system with constant contact spring stiffness and the variable structural damping factors. This approach is applied to identify the correct set of interface parameters of a practical spindle-tool unit using the experimental test data. An effective optimization strategy is used to update the finite element model with the various statistical sampling parameters to obtain the rigidity. Further, the optimal data set is identified by using single point simulated annealing (SA) and metaheuristic genetic algorithms (GA) schemes. The proposed methodology can help to standardize the tests with various spindle-holder interfaces by modeling the machine tool spindle.
更多查看译文
关键词
Joint dynamics, spring stiffness, structural damping factors, modal testing, interface parameters, non-conventional optimization
AI 理解论文
溯源树
样例
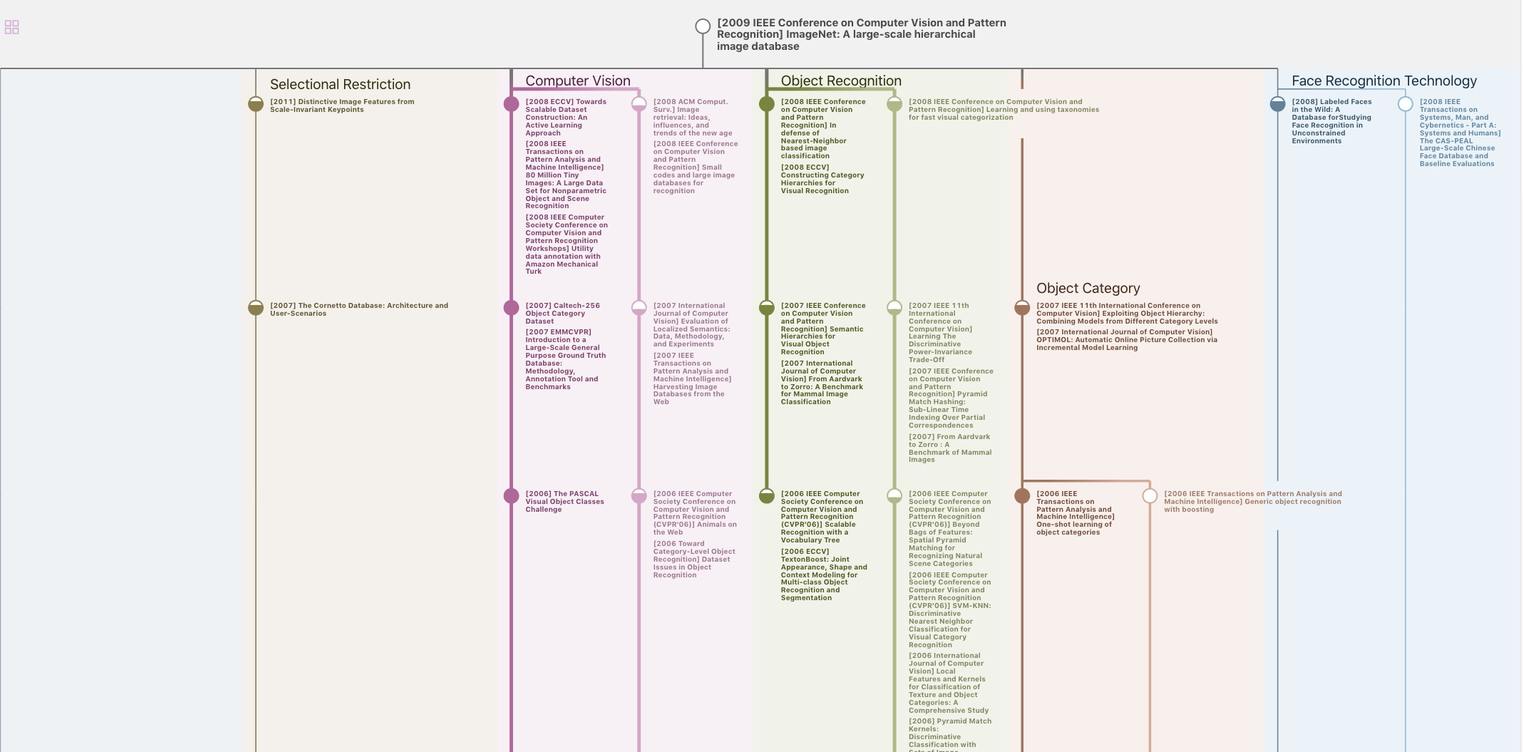
生成溯源树,研究论文发展脉络
Chat Paper
正在生成论文摘要