Ti–6Al–4V microstructural functionally graded material by additive manufacturing: Experiment and computational modelling
Materials Science and Engineering: A(2021)
摘要
In this study, a functionally graded material (FGM) was fabricated using a powder bed fusion additive manufacturing technique. The FGM evaluated was Ti–6Al–4V, due to its importance in the medical device and aerospace sectors. The microstructure at selected build locations was analysed using both scanning electron microscopy (SEM) and electron backscatter diffraction (EBSD) techniques, where a gradient was observed both in terms of grain morphology and texture intensity. In addition, nanoindentation on the FGM sample shows a near quadratic shaped smooth gradient elastic modulus profile, with peak values at the midpoint of the gauge length. A tensile test to failure was conducted on the FGM sample with the aid of digital image correlation for surface strain analysis. Results show a gradient of local maximum principal strain in the highly {0001} textured section, while the reference sample in the control group shows a near-uniform strain distribution throughout the whole gauge length. A crystal plasticity finite element (CPFE) model was developed to explain the effect of texture on the mechanical properties adopting the microscopy-informed texture intensity gradient. Despite exhibiting higher elastic modulus (in the transverse direction, as measured via nanoindentation) the mid-section of the gauge length had a higher concentration of strain when loaded in the axial tensile direction, corresponding to build direction. The microscopy and computational modelling show that this apparent contradiction was explained via a high intensity of {0001} texture in the mid-section, leading to favourable conditions for axial strain accumulation.
更多查看译文
关键词
Functionally graded material,Ti–6Al–4V,Powder bed fusion,Electron backscatter diffraction,Crystal plasticity finite element model
AI 理解论文
溯源树
样例
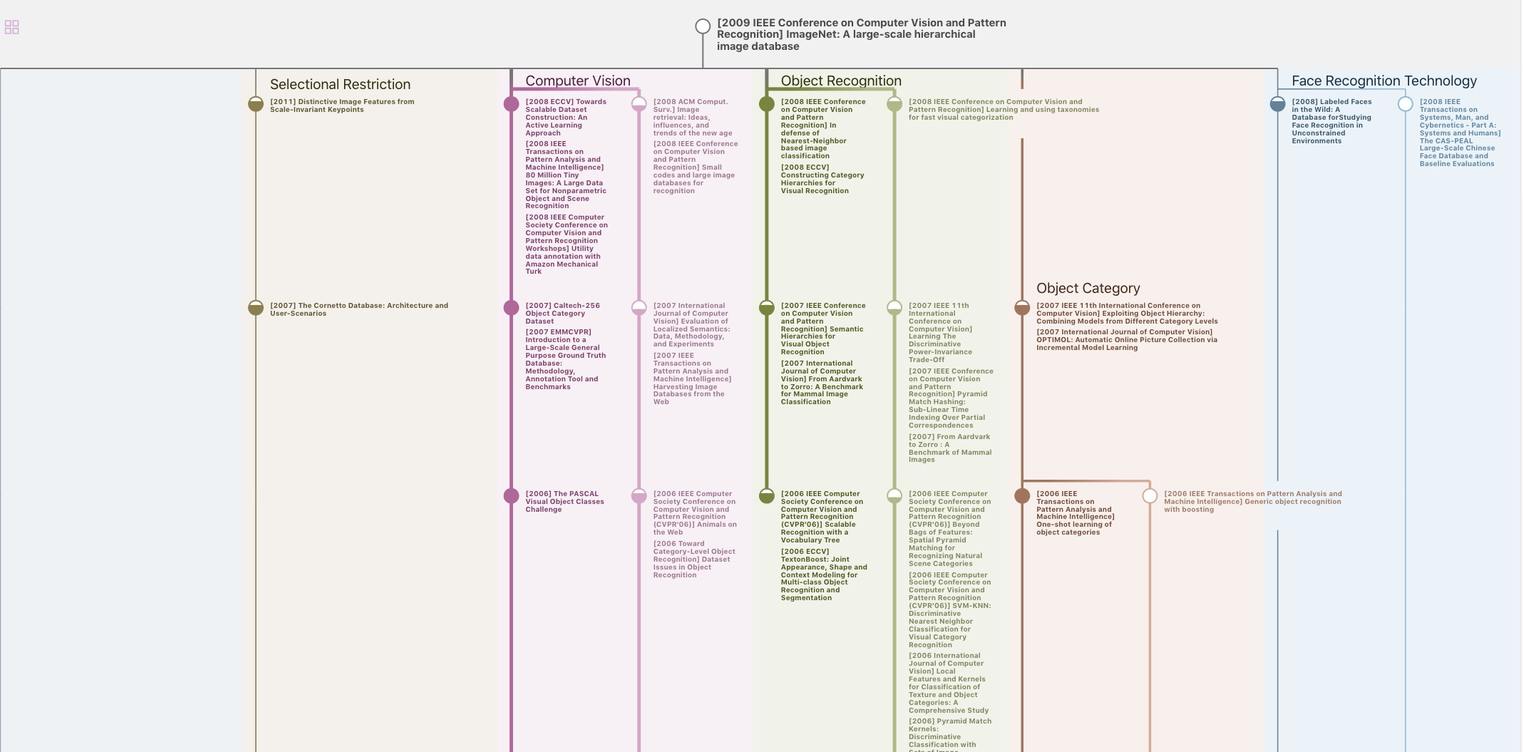
生成溯源树,研究论文发展脉络
Chat Paper
正在生成论文摘要