Flat Plate Pulsating Heat Pipes: A Review On The Thermohydraulic Principles, Thermal Performances And Open Issues
APPLIED THERMAL ENGINEERING(2021)
摘要
Thermal management of modern micro- and high-power electronic systems has become a progressively challenging problem due to current trends in miniaturization and increased heat generation. Conventional cooling methods, such as natural and force convection, have become insufficient to meet new challenges in electronics industries, transport and space applications where thermal management system size, mass, autonomy, high density and overall system reliability play a crucial role. Unlike active technologies, heat pipes are passive heat transfer devices without moving mechanisms which lead to greater reliability, even though they are limited by capillary, viscous and/or gravity factors. In contrast, the Pulsating Heat Pipe (also called Oscillating Heat Pipe) has recently become a source of increasing interest: first, due to fascination for the complexity of the internal two-phase phenomena; and secondly, due to novel applications, which are rapidly increasing the Technology Readiness Level of this device, for both ground and space environments. Pulsating heat pipe manufacturing can be divided into two categories: the classical tubular pulsating heat pipe, and the flat plate pulsating heat pipe. While the former is manufactured and developed from a single tube enrolled like a serpentine around heat and cold sources, the latter is obtained from a metallic plate including an engraved serpentine single channel, and hermetically closed on its top side by a second plate. These two manufacturing concepts lead to differences in operating behavior that are worth noting in order to better understand the functioning of the devices. This paper presents a review of recent scientific experimental studies on thermal and flow behaviors of flat plate pulsating heat pipes, which present particular interest due to their structural dissimilarity compared to classical tubular pipes, leading to different thermo-hydrodynamic behaviors. The dissimilarities can be largely explained by the square or rectangular channels, leading to capillary pumping in the corners, and to the thermal spreading effect associated with the geometrical continuity of the plate. Local studies of self-induced evaporation have demonstrated the faster evaporation process in square channels versus circular ones, which was confirmed later by comparison tests of channel shapes in FPPHPs. Furthermore, FPPHPs tested in horizontal orientation are more often subject to dry-out of the evaporator zone than tubular ones. Based on these considerations, a literature overview of local hydrodynamic visualizations and physical analyses is presented first in order to fully understand the phenomenological aspects, which will help to analyze the following sections on: the most influential parameters (channel dimension, fluid/material, geometrical aspects, operating conditions); thermal performances and attempts at significant improvements and, finally, the potentially promising fields of application and the processes applied in manufacture of flat plate pulsating heat pipes. Synthesis in appendix highlights the behavior of effective thermal conductivities of many papers with parameters such as the heat flux applied at the evaporator, figures of Merit from the literature or hydraulic-diameter-to-capillary-length ratio, showing its increasing trend with heat flux and diameter. Lastly, a table gathers all available material and geometrical characteristics and operating conditions of all devices tested in the presented literature.
更多查看译文
关键词
Flat Plate Pulsating Heat Pipes, Experimental, Slug flow, Annular flow, Heat transfer performances
AI 理解论文
溯源树
样例
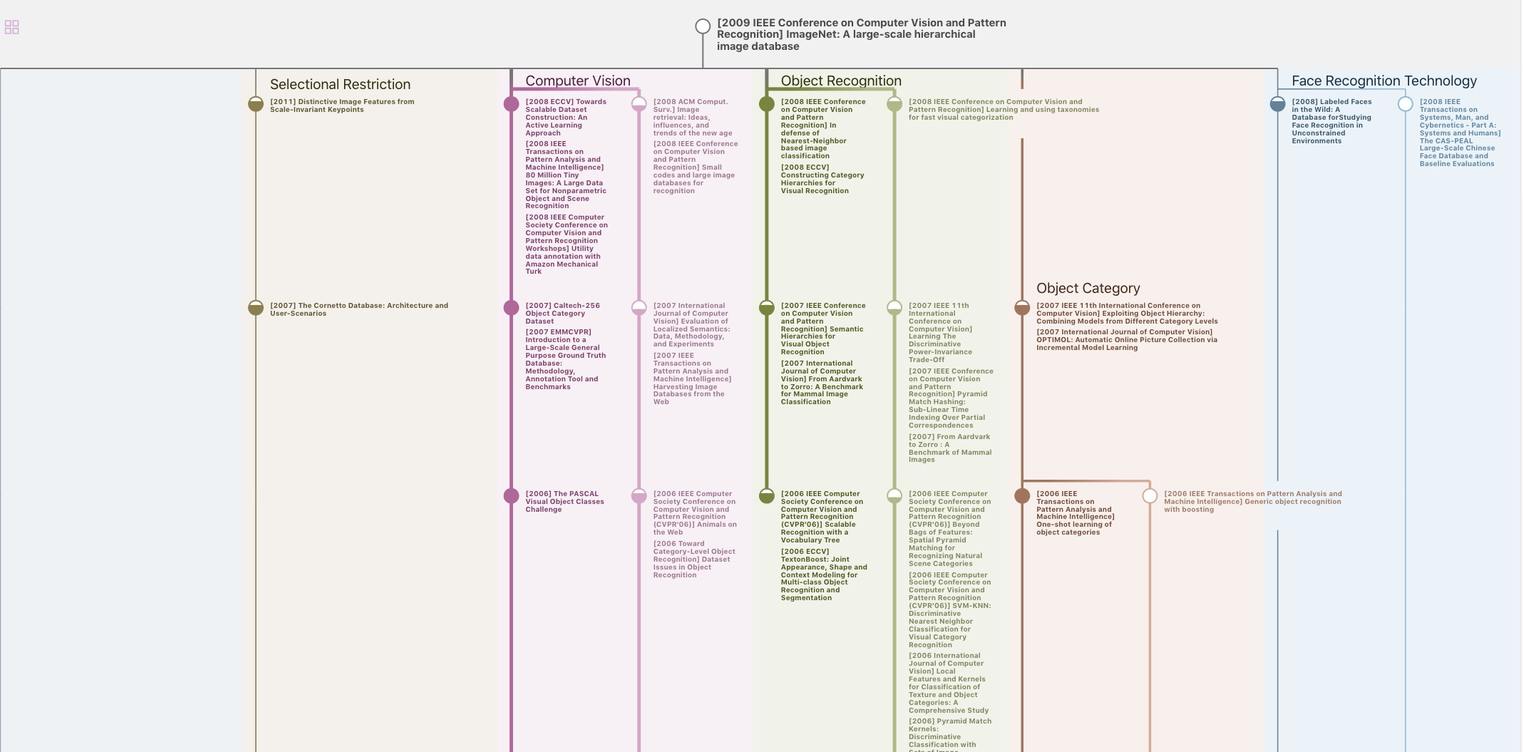
生成溯源树,研究论文发展脉络
Chat Paper
正在生成论文摘要