Multiphysics Modeling and Experimental Investigation of the Deposition Process in Fused Filament Fabrication Method, under High-Viscosity and Non-Newtonian Material Flow
JOURNAL OF MATERIALS ENGINEERING AND PERFORMANCE(2021)
摘要
In this study, the process of thermoplastic material deposition during 3D printing has been investigated via a multiphysics approach, using numerical and experimental tools. Namely, through computational fluid dynamics modeling, details of the flow structure and heat transfer process of the deposited material from the nozzle head onto the bed have been investigated. Experimental trials were conducted to validate the results of the computational model, and a good conformity between the results was obtained, with error less than 8%. Both curling and fluid mechanical swing machine print patterns were captured, especially given the high-viscosity and non-Newtonian characteristics of the flow. In particular, in the conducted case on ABS, results indicated that the ratio of the extrudate diameter to the nozzle diameter is around 12%. At feed rates lower than 100 mm/min, the curling takes place, where the extruded material bends up against the direction of the injection at the nozzle. It was observed that the fluid mechanical swing machine pattern takes place at the feed rate-to-moving bed speed ratios higher than 1.0, and depending on the nozzle to bed gap. High fidelity numerical platforms are deemed critical to better comprehend and predict complex local phenomena taking place during fused filament fabrication, and accordingly to more reliably optimize the process parameters.
更多查看译文
关键词
additive manufacturing,computational fluid dynamics,flow curling,fluid mechanical swing machine,modeling and simulation,thermomechanical processing
AI 理解论文
溯源树
样例
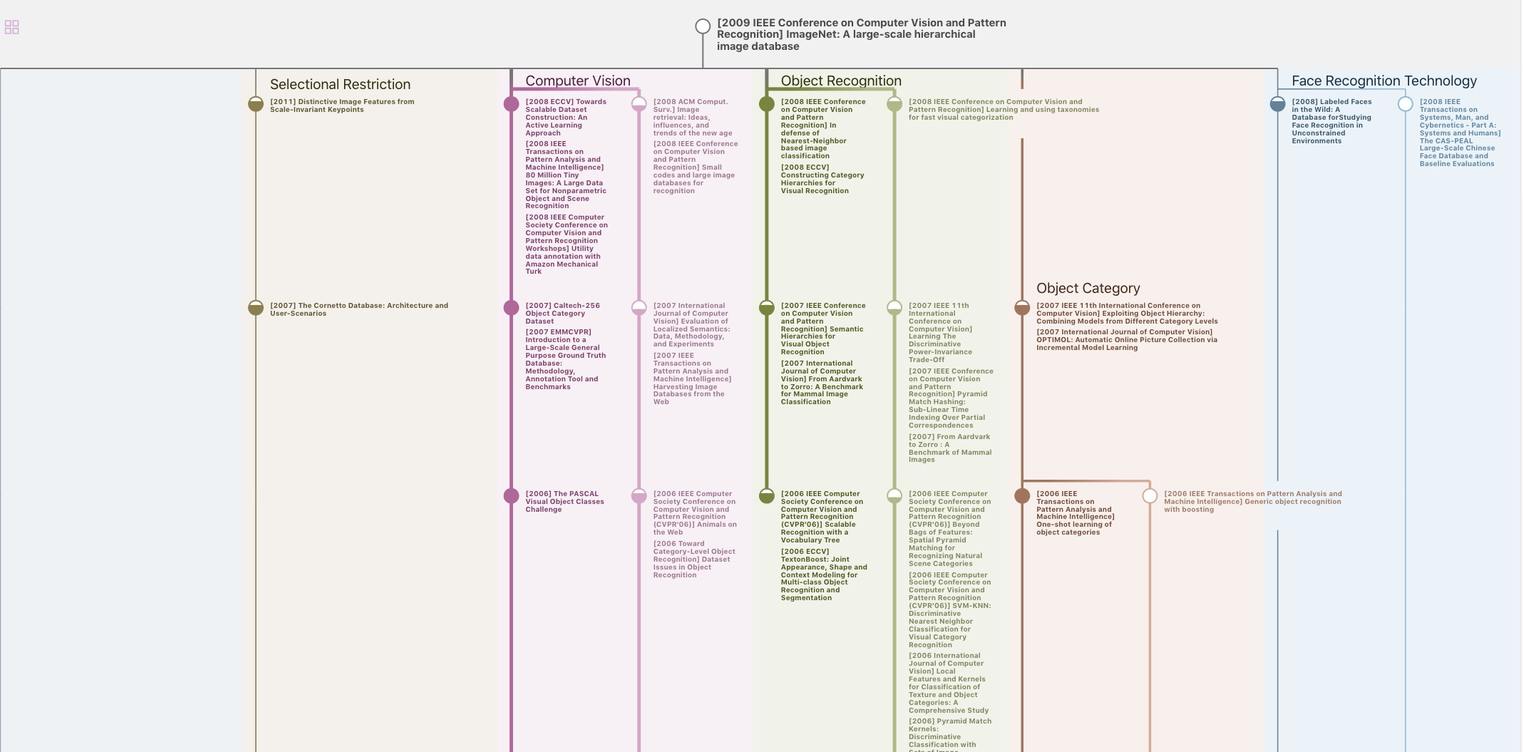
生成溯源树,研究论文发展脉络
Chat Paper
正在生成论文摘要