Additive Manufactured 316l Stainless-Steel Samples: Microstructure, Residual Stress And Corrosion Characteristics After Post-Processing
METALS(2021)
摘要
Additive manufacturing (AM) is a relatively new manufacturing method that can produce complex geometries and optimized shapes with less process steps. In addition to distinct microstructural features, residual stresses and their formation are also inherent to AM components. AM components require several post-processing steps before they are ready for use. To change the traditional manufacturing method to AM, comprehensive characterization is needed to verify the suitability of AM components. On very demanding corrosion atmospheres, the question is does AM lower or eliminate the risk of stress corrosion cracking (SCC) compared to welded 316L components? This work concentrates on post-processing and its influence on the microstructure and surface and subsurface residual stresses. The shot peening (SP) post-processing levelled out the residual stress differences, producing compressive residual stresses of more than -400 MPa in the AM samples and the effect exceeded an over 100 mu m layer below the surface. Post-processing caused grain refinement and low-angle boundary formation on the sample surface layer and silicon carbide (SiC) residue adhesion, which should be taken into account when using the components. Immersion tests with four-point-bending in the heated 80 degrees C magnesium chloride solution for SCC showed no difference between AM and reference samples even after a 674 h immersion.
更多查看译文
关键词
powder methods, additive manufacturing (AM), post-processing, residual stresses, 316L stainless-steel, electron microscopy
AI 理解论文
溯源树
样例
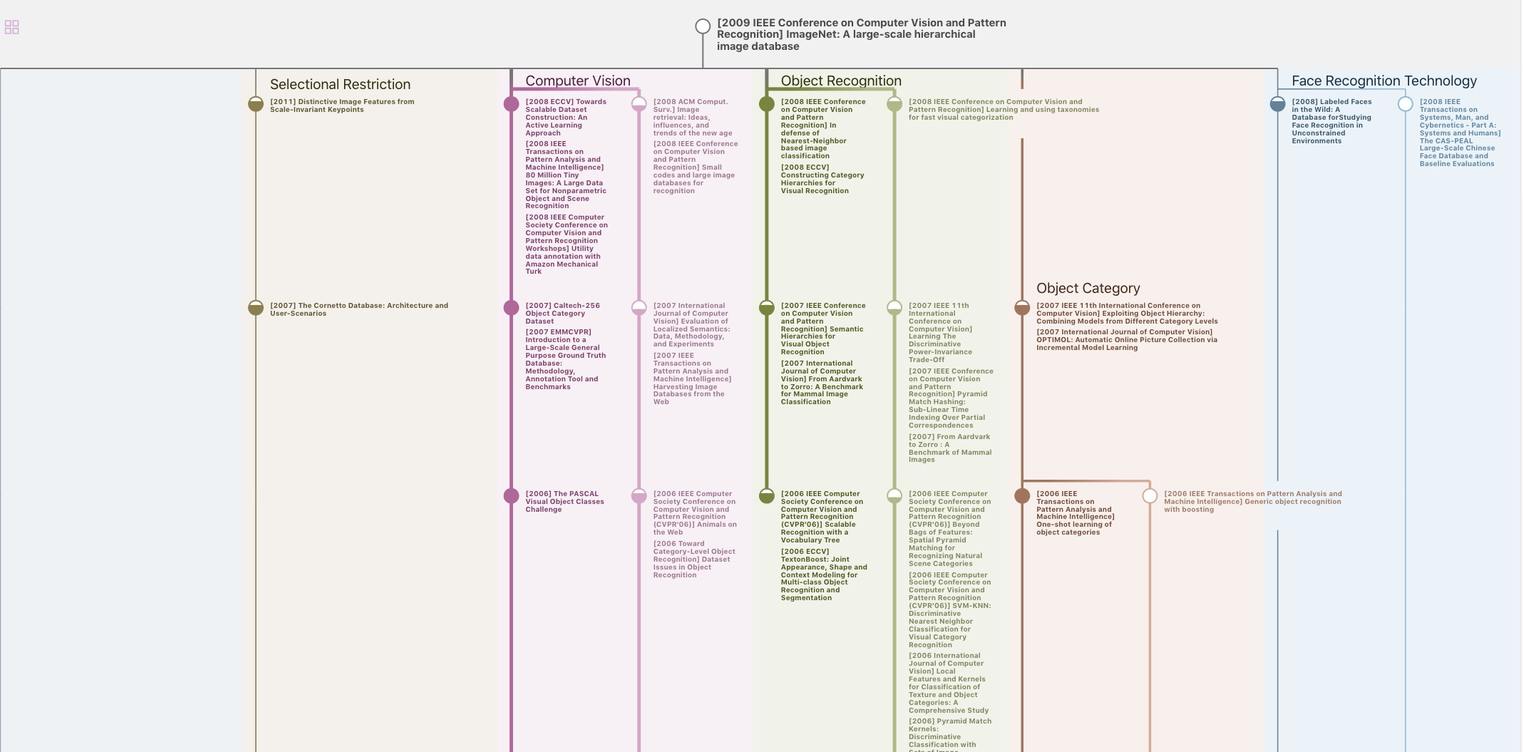
生成溯源树,研究论文发展脉络
Chat Paper
正在生成论文摘要