Modeling and compensation of joint-dependent kinematic errors in robotic manipulators
2016 International Symposium on Flexible Automation (ISFA)(2016)
摘要
Bearing systems and harmonic drives in robots introduce complex kinematic errors which result in joint kinematic errors that reduce the accuracy of their manipulators. Typical calibration methods do not consider these complex errors, thus, limiting post calibration performance. In this paper, a method of modeling and calibrating robot kinematic errors by building a joint-dependent kinematic error model is presented. Measurements are collected by a laser tracker and Active Target mounted on the end of the last robot link. A joint-dependent kinematic error model is constructed and the model parameters are identified with a mathematical algorithm based on maximum likelihood estimation. The kinematic error model is used to modify joint commands offline. Experiments are implemented on a FANUC LR Mate 200i robot. Using 250 measurements to construct the kinematic error model, the mean residual between the measured and modeled positions is reduced from 3.379 to 0.105 mm, a 96.9% reduction. Compensation is applied to an independent set of 100 measurements, and the mean residual is reduced from 3.614 to 0.131 mm, a 96.4% reduction.
更多查看译文
关键词
joint-dependent kinematic errors compensation,robotic manipulators,bearing systems,harmonic drives,robot kinematic errors modeling,robot kinematic errors calibration,joint-dependent kinematic error model,laser tracker,active target,robot link,mathematical algorithm,maximum likelihood estimation,FANUC LR Mate 200i robot,mean residual
AI 理解论文
溯源树
样例
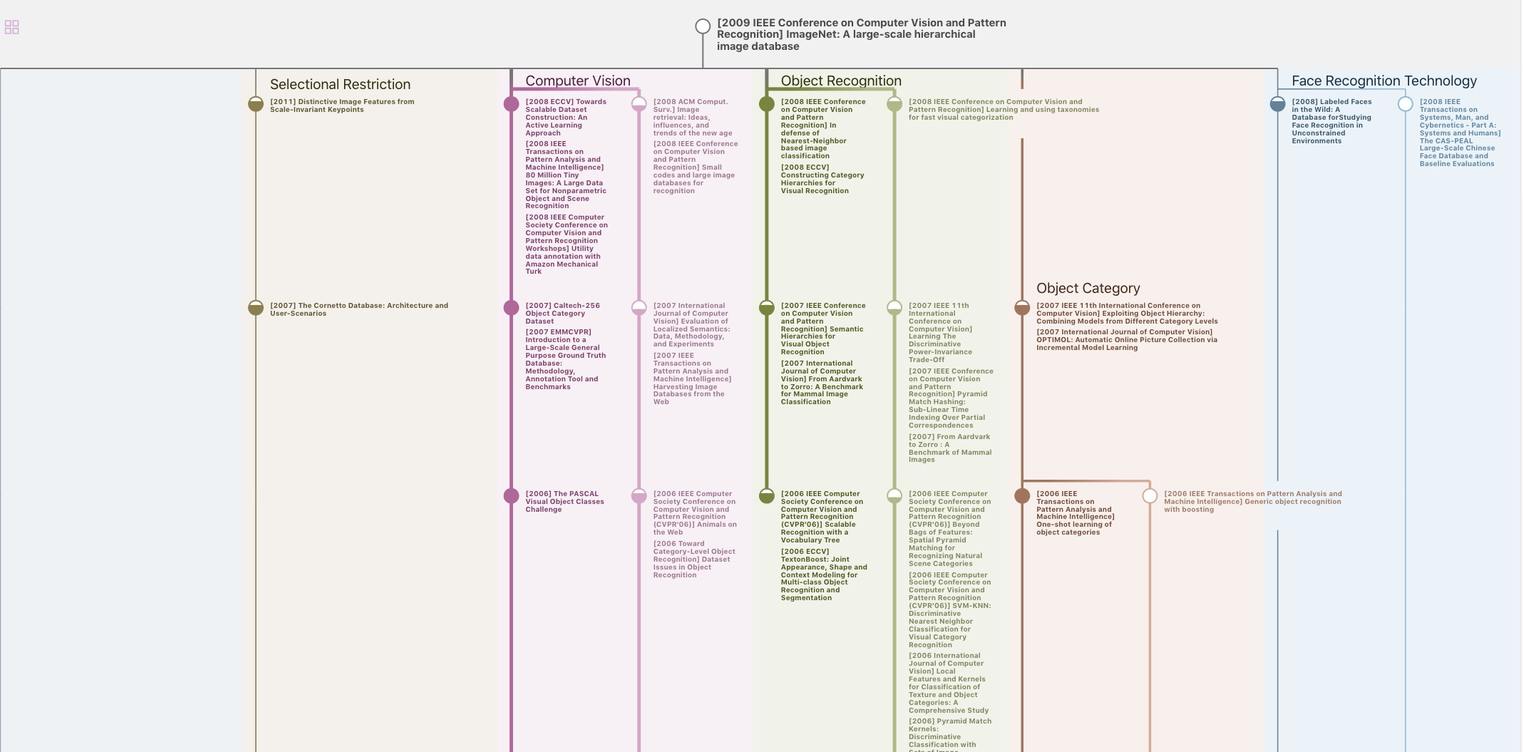
生成溯源树,研究论文发展脉络
Chat Paper
正在生成论文摘要