Investigation on the kerf and surface formation in the magnetic field-assisted WEDM-LS based on successive discharges
The International Journal of Advanced Manufacturing Technology(2021)
摘要
Magnetic field-assisted low-speed wire electrical discharge machining (MF-assisted WEDM-LS) is an effective technique to improve the surface quality of the workpiece. This paper presents a successive removing model to predict kerf width and the surface topography of nickel–titanium (Nitinol) shape memory alloy in different parameters. Firstly, the motion of an electron was calculated in the magnetic field. It could be obtained that if the length of the discharge channel path was the same with the condition that in traditional WEDM-LS, the width of the discharge gap was decreased because of the deflection of the electron trajectory caused by the magnetic field. Then, a modified gauss heat source equation was derived by calculating the incident angle of the discharge channel. Based on the principle of conservation of energy, the shape of the crater in different parameters was emulated. Moreover, an electrothermal coupling model was established to investigate the surface formation in the successive discharges process. The simulation results show that the average value of the surface roughness of the workpiece in WEDM-LS with magnetic field assisted was decreased by 12.3% compared with that in traditional WEDM-LS. Eventually, experiments of kerf and surface quality were carried out respectively. The experimental results showed that the kerf decreased from 376.2 to 361.7 μm in the magnetic field intensity of 0.4 T. The surface topographies of the workpieces showed good agreement with the simulation results, and the average relative error of surface roughness between simulated results and experimental results is 8.7%.
更多查看译文
关键词
Wire electric discharge machining,Magnetic field,Kerf,Successive discharges,Workpiece surface
AI 理解论文
溯源树
样例
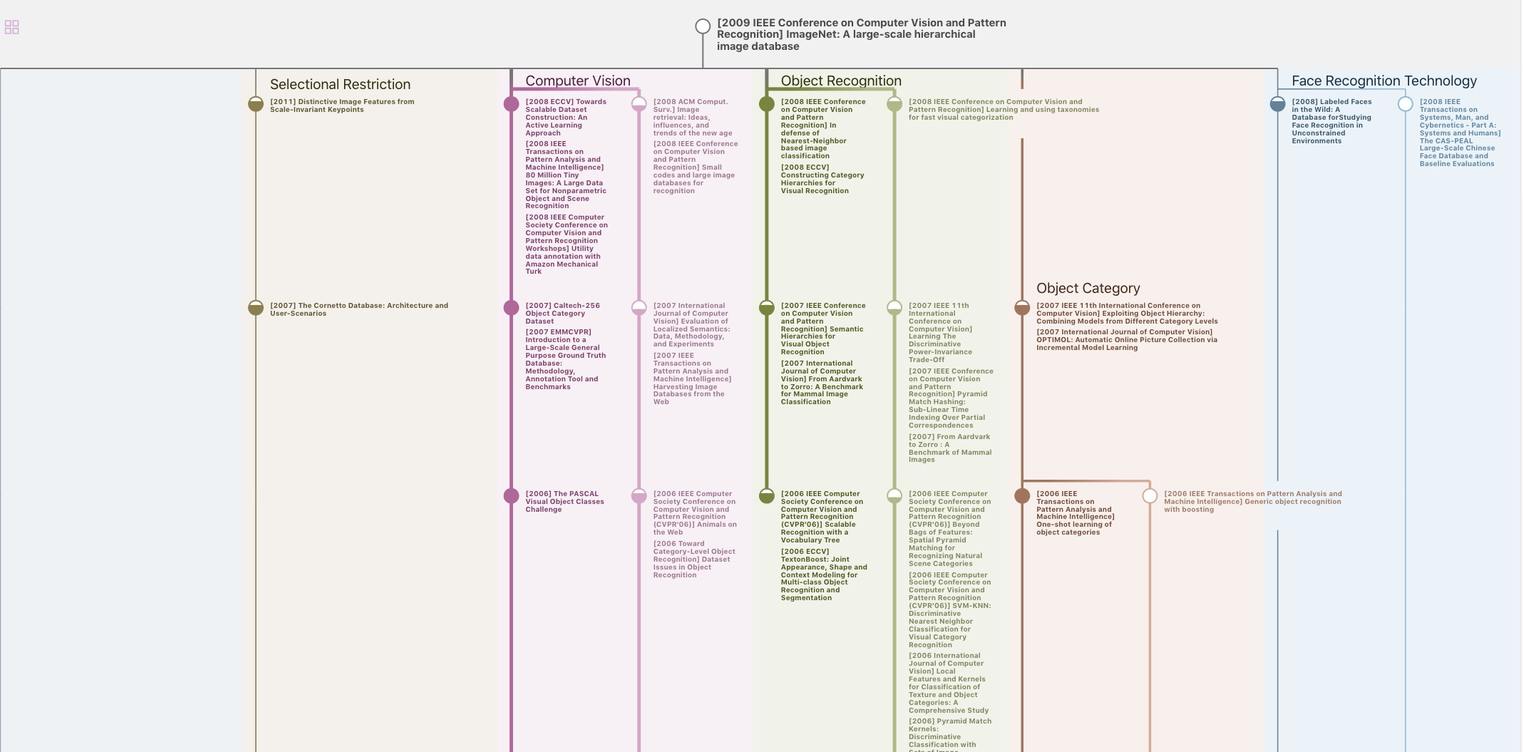
生成溯源树,研究论文发展脉络
Chat Paper
正在生成论文摘要