Digital Twin Modeling For Temperature Field During Friction Stir Welding
JOURNAL OF MANUFACTURING PROCESSES(2021)
摘要
New development on the modeling approaches is generally required to fusing the sensor data to the computational model in order to build up digital twins for the manufacturing processes. In this paper, we propose a modeling approach for building a digital twin for friction stir welding (FSW) based on a sensor-based numerical simulation. In the proposed approach, a novel iterative cyber-physics fusion algorithm is proposed to calculate the in-process 3D temperature field during FSW by fusing the measured temperature data to a ?moving heat source? analysis. Two FSW cases of commercial aluminum alloys AA2024 and AA6061 are analyzed to test the proposed modeling approach. It is demonstrated that the real-time calculating of the in-process 3D temperature field during FSW is highly feasible. When a timestep of 2.0 s is adopted, the proposed approach shows good reliability, as the average error between the measured and the calculated temperatures is less than 4 ?C. More importantly, it is found that the calculation time for the whole welding process is shown to be less than the physical welding time. This allows that the sensor-based numerical simulation and the physical FSW process can be synchronized with a second-level temporal precision, which provides a viable cyber-physics fusion approach for digital twin modeling for the FSW process.
更多查看译文
关键词
Friction stir welding, Digital twin, Temperature field, Numerical simulation
AI 理解论文
溯源树
样例
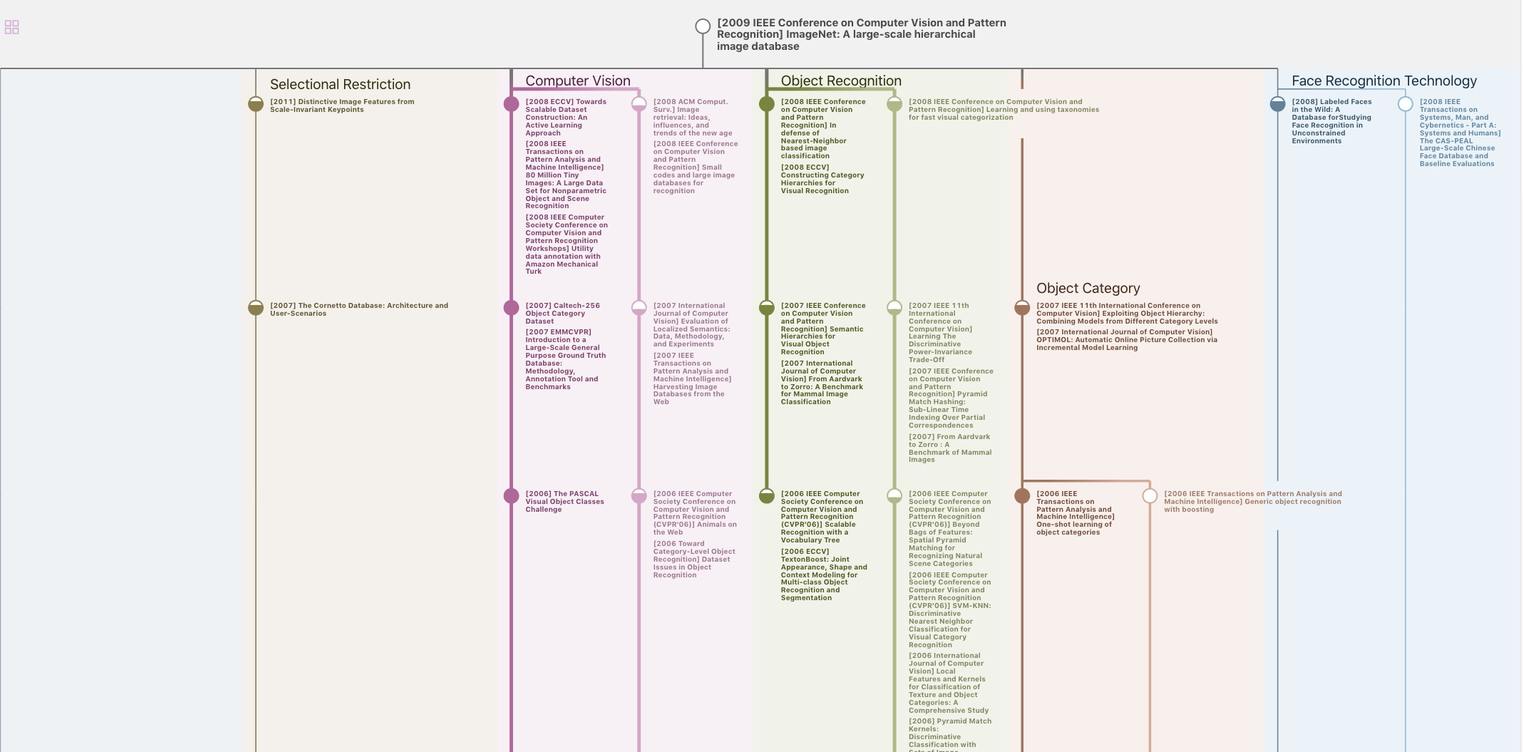
生成溯源树,研究论文发展脉络
Chat Paper
正在生成论文摘要