Microstructure Evolution During Controlled Rolling Of An Nb-Ti Microalloyed Steel
STEEL RESEARCH INTERNATIONAL(2021)
摘要
The microstructural evolution of an Nb-Ti microalloyed steel with the application of coiled tubing is studied in detail during hot rolling followed by accelerated cooling and simulated coiling by means of optical microscopy complemented with electron backscattered diffraction and transmission electron microscopy. It is found that the main microstructural characteristics, i.e., grain size, grain morphology, and texture, vary during different thermomechanical steps, largely in finish rolling. Finish rolling at 850 degrees C, in the nonrecrystallization region, activates the deformation-induced ferrite transformation (DIFT) mechanism and leads to the appearance of gamma-fiber, and {332} and {113} components. Decreasing the finish rolling temperature to 750 degrees C promotes this mechanism and results in finer final microstructure consisting of low angle grain boundaries. However, it is found that to obtain a homogenous microstructure with gamma-fiber texture, the final rolling temperature should be high enough for the sufficient occurrence of static recrystallization in ferrite just after finish rolling. More deformation in the nonrecrystallization region, especially for the last rolling steps, strongly affects the DIFT mechanism and leads to fine-grained microstructure. Refining of ferrite to the grain size of 3.5 +/- 0.5 mu m results in 65% enhancement of yield strength and reduction of strain hardening by 25%.
更多查看译文
关键词
coiled tubing steel, controlled rolling, mechanical properties, microstructure, texture
AI 理解论文
溯源树
样例
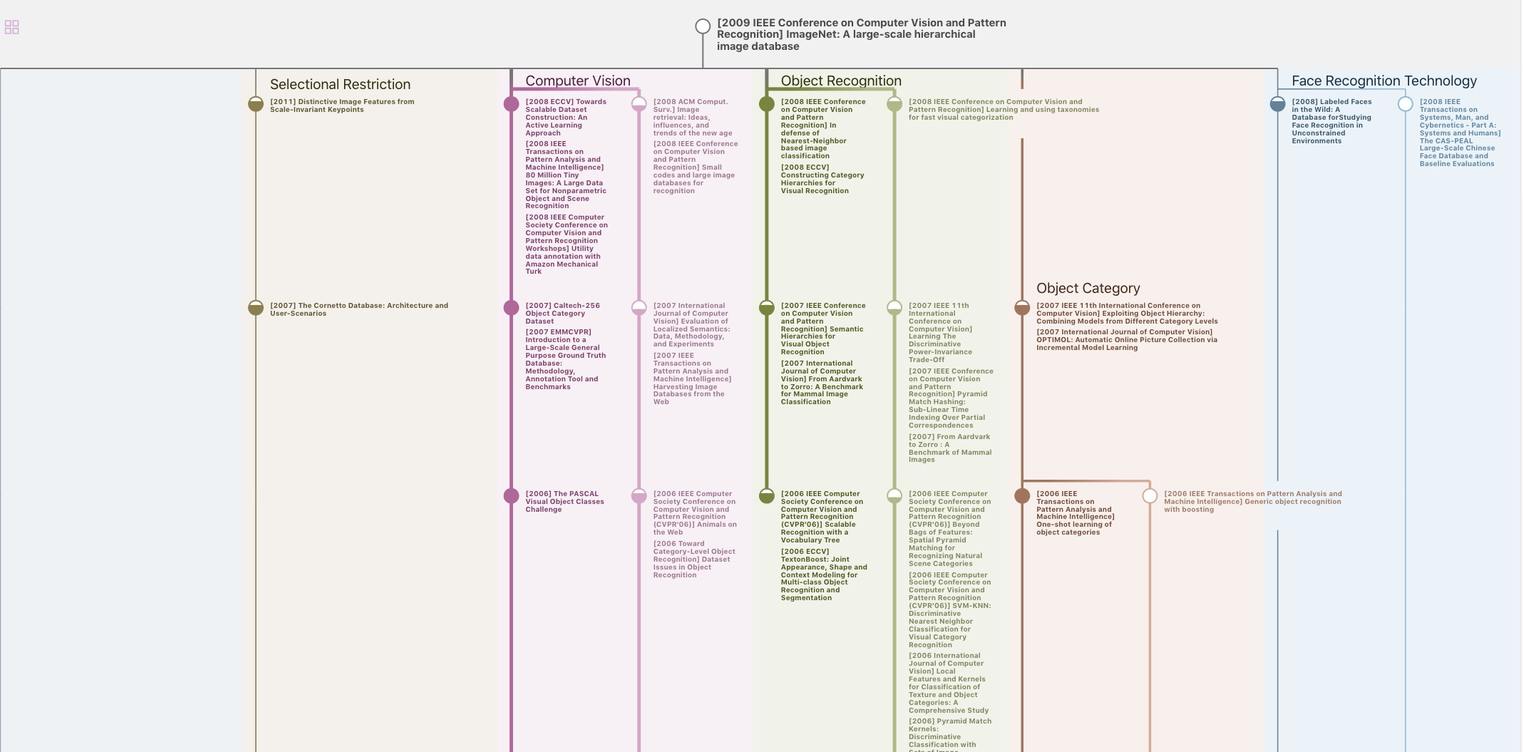
生成溯源树,研究论文发展脉络
Chat Paper
正在生成论文摘要