Modeling of stiffness characteristic on evaluating clamping scheme of milling of thin-walled parts
The International Journal of Advanced Manufacturing Technology(2021)
摘要
As one of the vital technological factors influencing the machining quality, machine tool fixture has been regarded as an important research object by scholars at home and abroad. In this paper, a new method for rapid evaluation of clamping scheme was presented based on the study of machining deformation of aerospace complex thin-walled parts. Firstly, Through the modal analysis of the thin-walled parts, the weak links of the structure and the direction of the large vibration displacement of the nodes are found. Then, the maximum displacement and natural frequency of the main vibration direction under different clamping schemes were obtained after intercepting several nodes and analyzing through FE software. The optimal clamping scheme was obtained through the result comparison. Finally, based on the existing research results, a mathematical model of evaluating the complexity of fixture characteristics was constructed. In this model, the stiffness values of multiple joints were considered, and the characteristic machining stiffness and the average value ∆ K were obtained so as to evaluate the deformation resistance of the thin-walled parts. The influence of different clamping schemes on machining quality was quantitatively evaluated by the index. On the basis of the proposed method, a case study of aerospace thin-walled parts was conducted, and then the rapid evaluation and optimization of the milling clamping scheme for thin-walled parts were realized.
更多查看译文
关键词
Thin-walled part,Clamping scheme,Average stiffness,Processing complexity coefficient
AI 理解论文
溯源树
样例
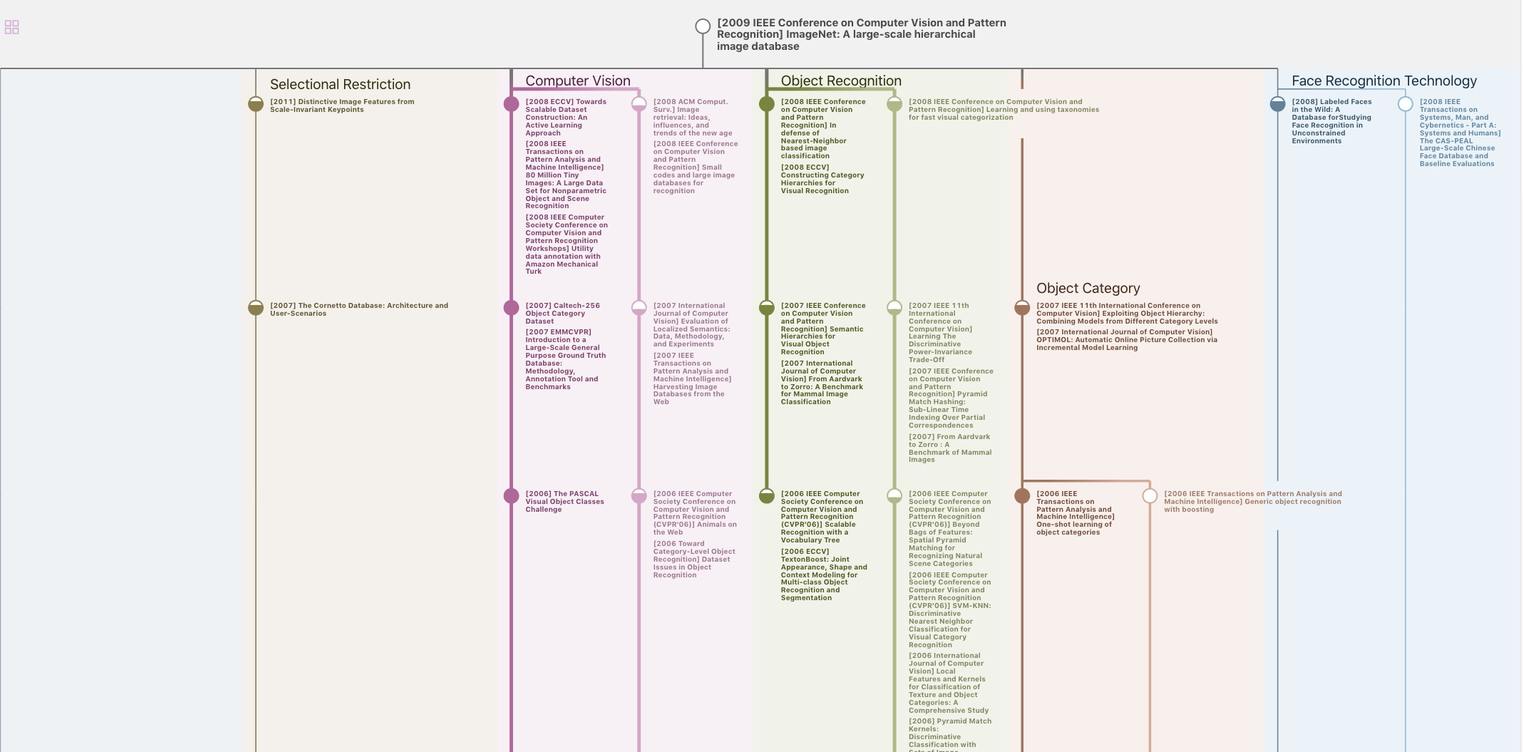
生成溯源树,研究论文发展脉络
Chat Paper
正在生成论文摘要