Comparison Of Analytical, Empirical, And Finite-Element Modeling Of Weld Metal Cooling As Function Of Plate Orientation, Thickness, And Heat Input
JOURNAL OF MANUFACTURING PROCESSES(2021)
摘要
Common shipbuilding practice for calculating weld metal cooling rate uses an equation derived from experiments conducted on plates considered semi-infinite (in length and width dimensions) in terms of thermal conduction. Similar assumptions are made with the classical two-dimensional (2D) and three-dimensional (3D) analytical models for weld metal cooling. These assumptions inherently limit the classical models' ability to correctly evaluate common shipbuilding welding configurations, such as initial layers in deep groove joints, root passes, and plate edge build-up welds. Unlike the empirical and analytical equations, finite-element analysis (FEA) methods enable transient heat source simulation with consideration given to plate geometry, joint orientation, and temperature-dependent material parameters. This study uses FEA methods to predict weld metal cooling rates for plate edge build-up scenarios on thickand thin-plate steel under various heat inputs. The FEA results were verified using physical testing and compared to the empirical and analytical cooling rate calculations. The FEA method predicted a much slower cooling rate than the empirical and analytical models for all variations of plate orientation and heat input investigated in this work. These results demonstrate that analytical and empirical methods, while useful for rapid screening and quality assurance-type assessments of cooling rates, can only be relied upon when they are applied to welding conditions similar to those under which they were derived. Improper application of simplified weld cooling models can have important structural implications when weld metal strength is inferred from the calculated cooling rates.
更多查看译文
关键词
Welding, Edge build-up, Computational simulation, FEA, SYSWELD, Steel
AI 理解论文
溯源树
样例
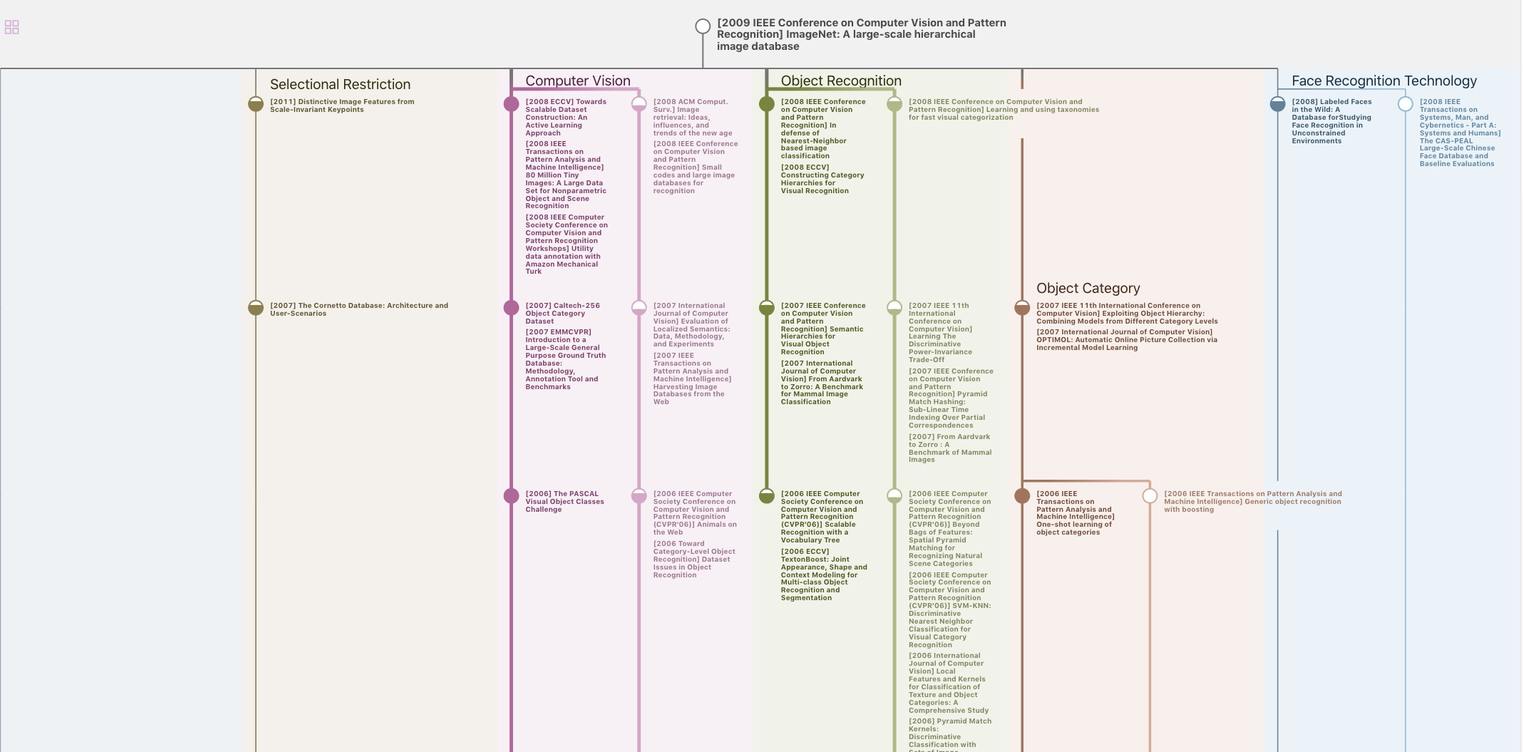
生成溯源树,研究论文发展脉络
Chat Paper
正在生成论文摘要