Characterization of kinematic hardening with a hydraulic bulge test
Procedia Manufacturing(2020)
摘要
Abstract The increase of the mapping accuracy in numerical simulations of sheet metal forming processes is an important field of research today. In this context, the modelling of the kinematic hardening plays a major role when it comes to nonlinear strain paths during the forming process. The kinematic hardening leads, beside other effects, to a lower increase of the hardening after a change of the linear strain path. Characterization of the Bauschinger coefficient, an indicator of the portion of kinematic hardening, is normally done with cyclic tension-compression tests. The testing setup is quite challenging in the strain measurement and the specimen handling due to the small geometry and the risk of buckling during compression. Thus, a hydraulic bulge test with an optimized geometry is used for the characterization of the kinematic hardening with a strain path change for the materials DC06 and DP600. According to literature, DC06 has no significant kinematic hardening, while the high strength steel DP600 is sensitive to this hardening mechanism. The strain path change is realized by a secondary element in the die. In the beginning of the test, a conventional circular die induces an equi-biaxial strain. After this preforming step, an elliptical geometry is used to induce plane strain in the specimen. The resulting strain path changes from equi-biaxial to plane strain. The flow curves out of the experiment show the kinematic hardening effect after the strain path change for the DP600 while no change is observable for the DC06. Numerical simulation with the identified kinematic factor should lead to a better mapping accuracy regarding the springback behavior.
更多查看译文
关键词
Material characterization,Kinematic hardening,Load path change,Bauschinger Coefficient,Hydraulic bulge test
AI 理解论文
溯源树
样例
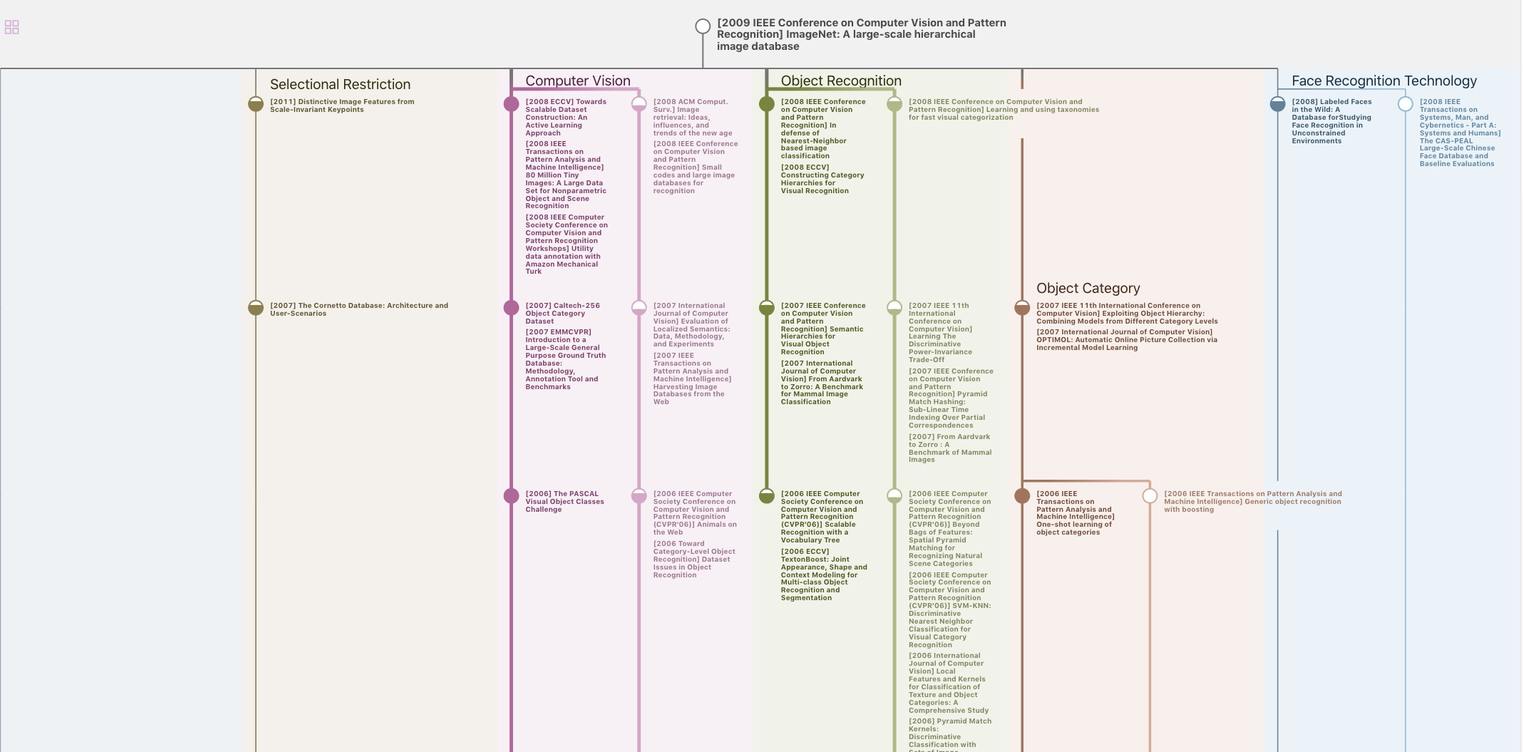
生成溯源树,研究论文发展脉络
Chat Paper
正在生成论文摘要