Evaluation of through-thickness residual stresses in conventional and narrow grooved stainless steel welds
PROCEEDINGS OF THE INSTITUTION OF MECHANICAL ENGINEERS PART L-JOURNAL OF MATERIALS-DESIGN AND APPLICATIONS(2020)
摘要
Thick AISI 304L stainless steel plates were welded using the gas metal arc welding process, and through-thickness residual stresses were evaluated by finite element simulation and the deep hole drilling technique. 3D moving heat source-based thermo-mechanical models were implemented to evaluate through-thickness residual stresses. The effects of the weld groove geometries and external restraints on the pattern of through-thickness residual stresses were studied. The maximum magnitude of locked-in residual stresses was recorded beneath the top surface, at a depth of around 6 mm. In comparison to conventional weld groove, the narrow weld groove configuration exhibited a 20-40% reduction in peak residual stresses. A significant rise in residual stresses was observed in constrained welds. The effect of the yield strength of the filler material on the evaluation of the through-thickness residual stress distribution in the course of finite element modeling was illustrated. The evolution of through-thickness residual stresses was also assessed concerning each weld pass.
更多查看译文
关键词
Welding simulation,residual stress,thermo-mechanical analysis,deep hole drilling,thick multipass welding
AI 理解论文
溯源树
样例
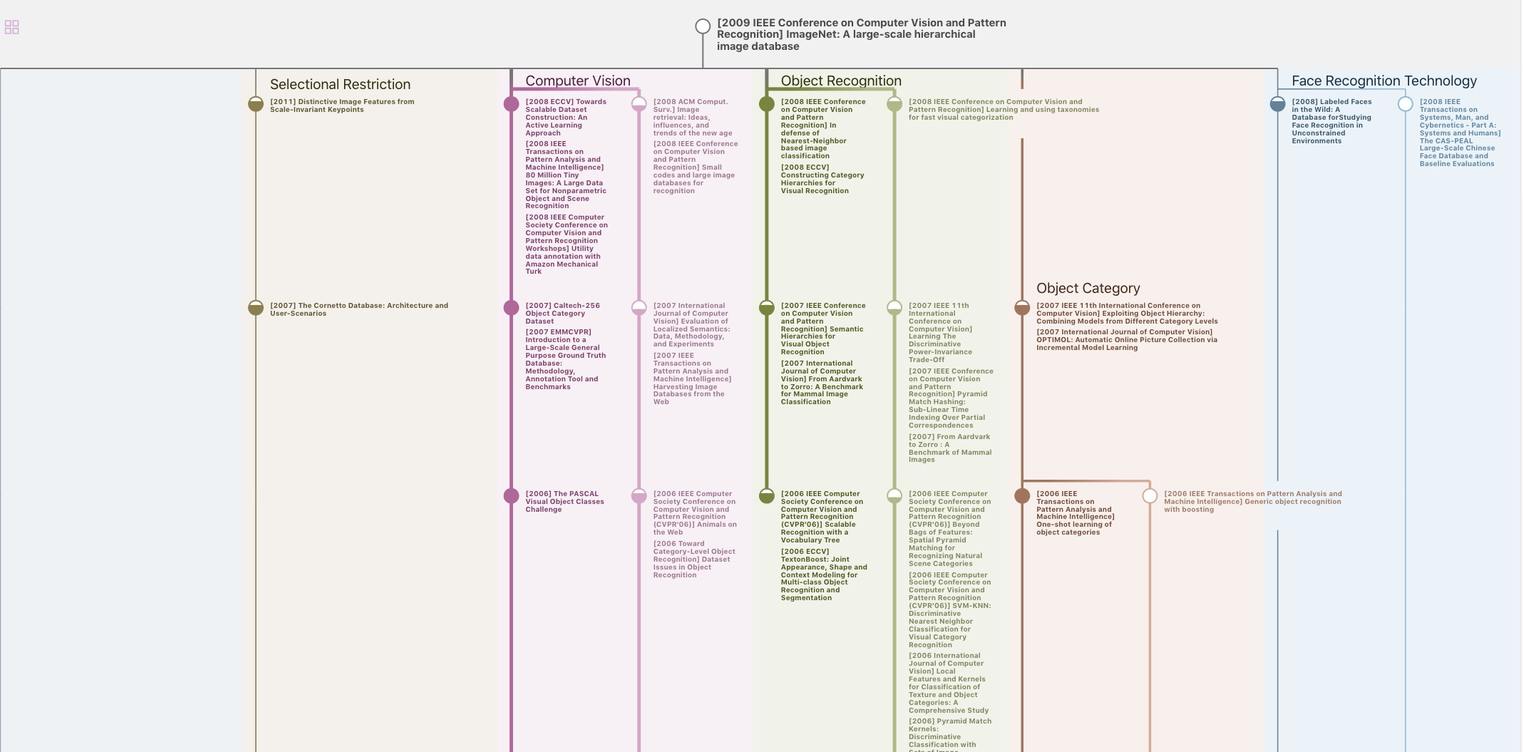
生成溯源树,研究论文发展脉络
Chat Paper
正在生成论文摘要