HARDWARE IN THE LOOP VALIDATION OF GNC FOR RVD/RVC SCENARIOS
GUIDANCE AND CONTROL 2013(2013)
摘要
The big challenge of new technologies, particularly related to GNC systems, is to achieve a TRL (Technology Readiness Level) high enough before flying in order to minimize the failure risks. Most of GNC related technologies need, in fact, to fly as experiment before being declared as validated for space use as mission baseline. In flight experiment opportunities are, nevertheless, expensive and very limited in terms of number of opportunities. This is especially true for new mission concepts in Europe such as Formation Flying or Rendezvous and Docking/capture. ESA HARVD activity (High integrity Autonomous RendezVous and Docking control system for MSR Capture scenario and Earth servicing missions), has been developed by an industrial team led by GMV, and includes a design and validation strategy that, using an incremental validation approach concept, starts by Model In the Loop (MIL, based on Matlab/Simulink), passes through SW In the Loop (SIL, non real-time), arrives to Processor In the Loop (PIL, real-time) and finalizes with Hardware in the Loop (HIL) with camera and Lidar HW breadboards in the loop with air-to-air signal transmission and space-representative relative motion generated by specific robotic devices synchronized with the GNC real-time host system and processor. Representative illumination conditions are guaranteed by the use of Fresnel lights. This paper describes briefly the above-mentioned Design, Development, Verification and Validation (DDVV) approach and focuses mainly on the integration of the PIL real-time test bench with the specific dynamic test bench devices (called platform and including two robotic arms, one of them hosted on a linear axis with motion capability up to 15 meters), the performance of the tests (several scenarios including the use of scaled mock-ups of MSR mission Sample Canister, the MSR Mars Ascent Vehicle and the IBDM Demo mission target spacecraft including a model geometry representative of the IBDM docking mechanism) and the obtained dynamic tests results (including a video of some of the cases) and lessons learnt. In addition, comparison of HIL test results with PIL/SIL/MIL results serve to validate the PIL/SIL/MIL test benches/simulator environment, to demonstrate the coherency of the DDVV approach and its use for later (and faster) design iterations (if needed).
更多查看译文
AI 理解论文
溯源树
样例
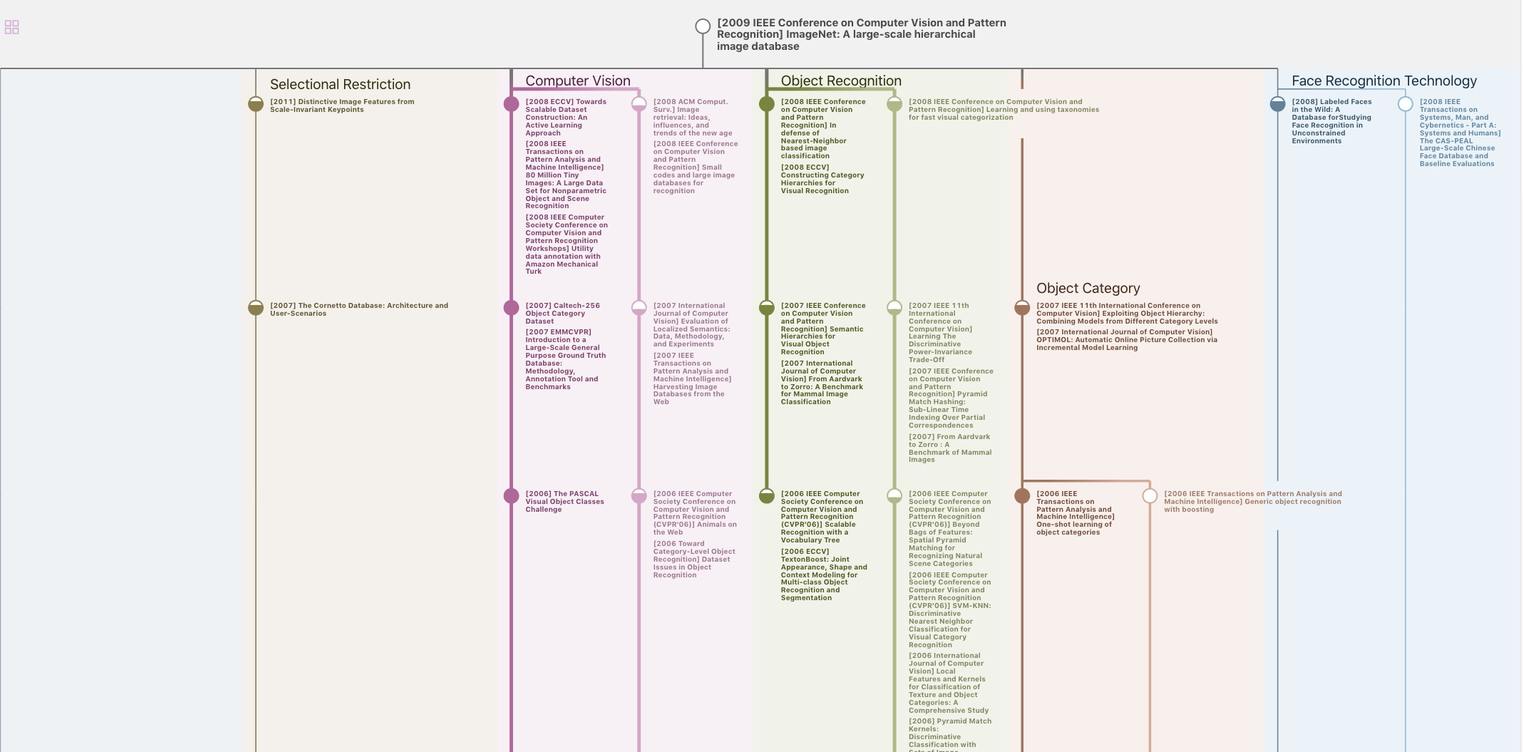
生成溯源树,研究论文发展脉络
Chat Paper
正在生成论文摘要