Optimization Based Motion Simulation of Industrial Manipulator for Small Working Space
ADVANCES IN MANUFACTURING TECHNOLOGY XXXI(2017)
摘要
In this paper, we simulate the industrial manipulator for small working space such as the welding robot for box girder in the offshore plant. Mechanical structure of the robot arm is built using Denavit-Hartenberg method for kinematic analysis. The total degrees of freedom is six and they are all rotational joints. Reachability, continuity and collision avoidance is calculated and checked through the optimization process. Recursive Lagrange's formulation is used for the dynamic equilibrium constraints. Design variables are the joint angle profiles which is parameterized using B - spline function approximation. Objective function is the joint torque square which is proportional to the mechanical energy. Constraints are imposed for joint angle limits, joint torque limits of motor capacities, the position and the velocity of end effector, and collision avoidance condition. The information for joint positions, velocities, and accelerations are recovered and simulated with robotics software to check the detail motion.
更多查看译文
关键词
Motion simulation,industrial robot manipulator,optimization
AI 理解论文
溯源树
样例
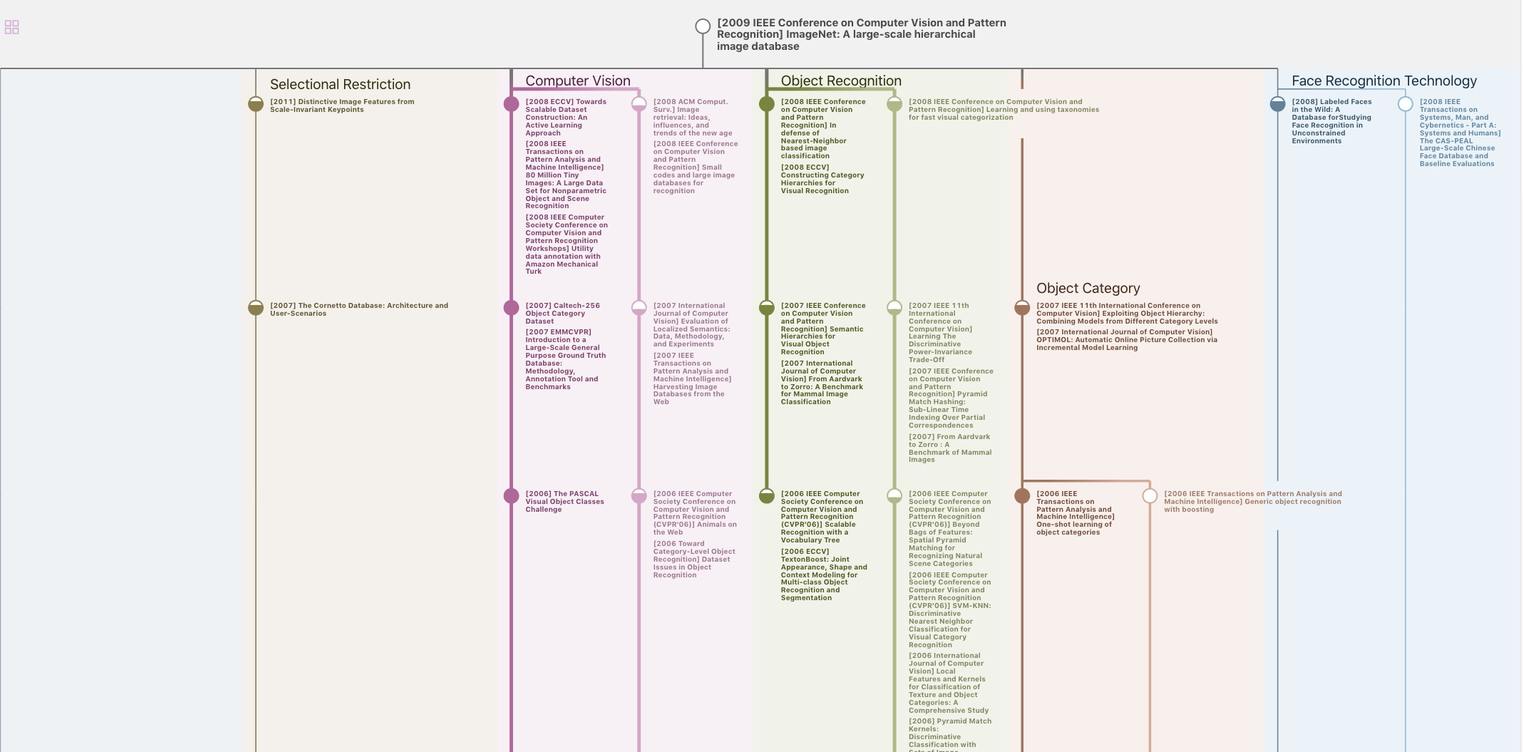
生成溯源树,研究论文发展脉络
Chat Paper
正在生成论文摘要