Development and Evaluation of a Mechanistic Tablet Coating Model
semanticscholar(2016)
摘要
D. Niblett, S. C. Porter, I. Gabbott, G. Reynolds, T. Morgan, K. Karan, J. Greenamoyer, R. Hach University of Manchester, Ashland Specialty Ingredients, AstraZeneca Purpose Aqueous film coating still remains a complex process in which the process parameters selected can have a major impact on ultimate product quality. In this study, a wide range of processing parameters was performed in order to verify and test and verify a model, that was partly mechanistic and partly empirical, that can ultimately link processing parameters to those quality outcomes. Methods A broad range of processing conditions (summarized in Table1) were examined, involving a 22 experiment statistical DoE approach, where all coating trials were conducted using an O’Hara LabCoat IIX coating pan fitted with a 15” coating pan insert (2.5 kg tablet charge). A standard HPMC-based film coating formulation (AquariusTM Prime) was applied at 15 w/w solids in all cases. At the conclusion of all coating runs, the coating processes were examined for overall coating process efficiency, and coated tablet samples were analyzed for surface roughness (Nanovea surface roughness analyzer) and gloss (TRICOR Model 805A Surface Analyzer). Coated tablets were also visually assessed for evidence of logo bridging and edge chipping defects. The results obtained from analysis of coating process conditions and coated tablet quality results obtained were ultimately used to test and validate an existing model that follows the determination of the tablet surface velocity profiles, spray application and drying conditions, spray coverage and surface drying conditions through theoretical and experimental methods. [1] [2] Equations taken from literature were validated through experimental methods such as Particle Imagery Velocimetry (PIV). Results Typical examples of the results obtained are summarized in Table 1. No cases of edge chipping were observed, but typical examples of the range of logo bridging defects observed are highlighted in Figure 1. Simplification of operating parameters through characterization by dimensionless quantities, primarily dimensionless spray flux, Ø (spray coverage) [3] and the dimensionless drying time, Ƭ (active drying phenomena; unique to this study) was found to be a good way to characterize those operating parameters, and enabled safe zones of operation to be developed by analyzing defect responses. These results indicate that the coating process conditions employed were capable of generating an extensive range of film-coated tablet quality attributes and process capabilities. For perspective purposes, coating roughness values in the range of 5-6 μm are typical of most commercial film-coated tablets, with the lower values representing smoother tablets. Additionally, gloss values in the range of 100-120 typify most film-coated products, while coating process efficiencies of >90 are usually desired.
更多查看译文
AI 理解论文
溯源树
样例
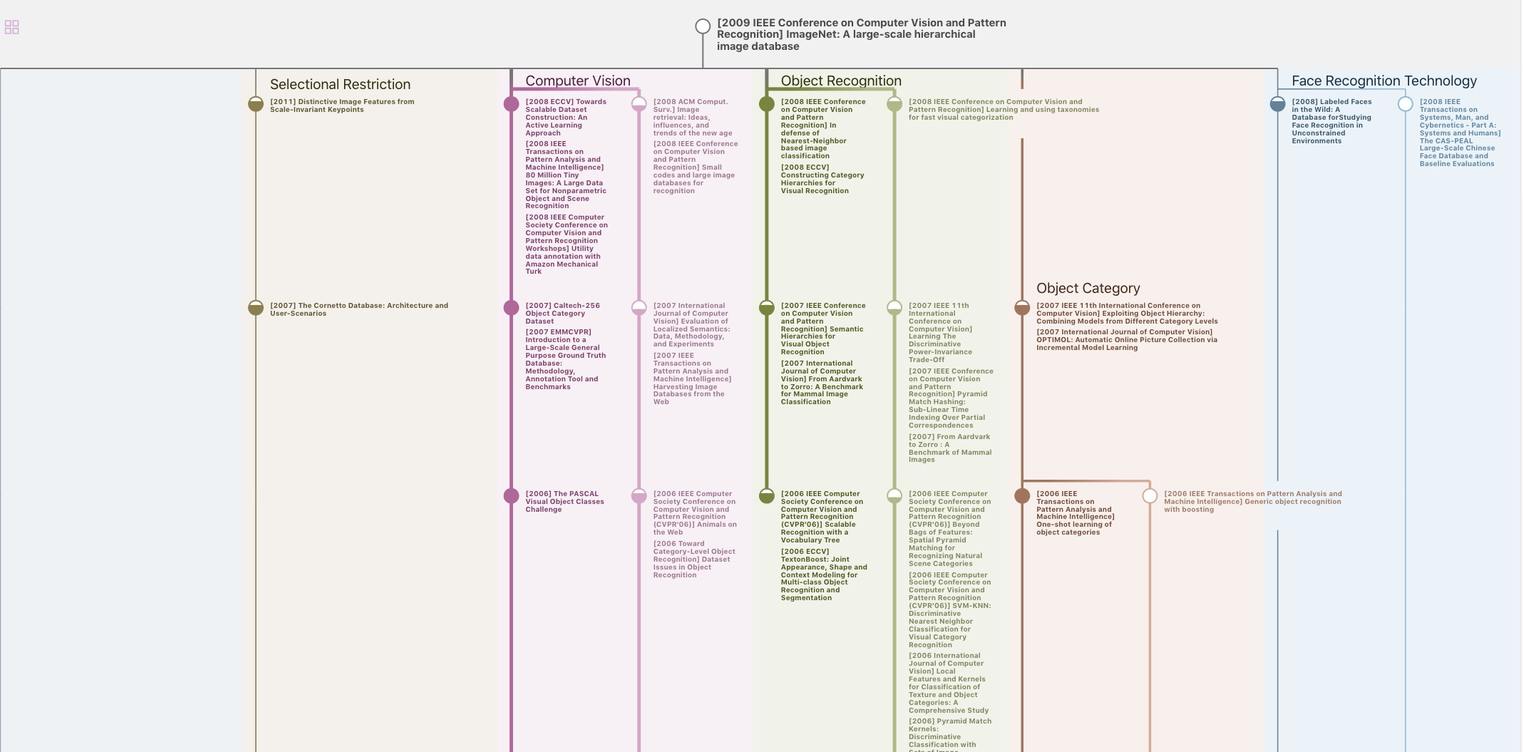
生成溯源树,研究论文发展脉络
Chat Paper
正在生成论文摘要