CFD analysis of Heat transfer and friction factor characteristics ina circular tubefitted with Parabolic-cut twisted tape inserts
semanticscholar(2013)
摘要
This paper reports the Computational Fluid Dynamics (CFD) modellingstudy on heattransferand friction factor of aconstant heat-fluxed tube equipped with Parabolic-cut twisted tape inserts in the laminar flow regime using a commercial CFD package(FLUENT-6.3.26). Two geometry parameters of the Parabolic-cut twisted tape have been considered in this study,a twist ratio and cut depth. The simulation has been carried out for twist tapeswith twist ratio (y=2.93, 3.91and 4.89) andcut depth(w =0.5, 1 and 1.5 cm). The CFD predicted resultsmatched with the literature correlations for plain tube for validation, with the discrepancy of lessthan ±8%for Nusselt number and ±6.5 % for friction factor.The results have also revealed that the Nusselt number and the frictionfactor in the tube with Parabolic-cut twisted tape (PCT) increase with decreasing twist ratios (y) andcut depth (w). Key word: Heat transfer augmentation, Friction factor, Parabolic-cut twisted tape,Fluent, CFD simulation. INTRODUCTION The augmentation techniques of heat transfer are widely applied to improving the performance of heat exchangersin chemical industries and air conditioning systemsto reduce the size and costs of the heatexchangers, these techniques are classified as active and passive techniques. The active techniques require external forces, e.g. electric field, surface vibration or Jet impingement. The passive techniques require special surface geometries or swirl/vortex flow devices.Many of experimental works on heat transfer augmentation using twisted tape as swirl/vortex flow deviceshave beenreported in the literature(Saha, Gaitonde et al. 1990; Manglik 1993; Naumov 1994; Wang 2002; Ujhidy 2003; Jaisankar, Radhakrishnan et al. 2009; Guo, Fan et al. 2011; Ibrahim 2011; Wongcharee and Eiamsa-ard 2011).Whereas, fewliteraturesare available in CFD modeling of heat transfer using twist tape inserts(Sivashanmugam 2008) reported the modeling of heat transfer augmentation in a circular tube fitted with helical twist insert in a laminar and turbulent flow using CFD. (Mugam 2009)conducted CFD simulations of heat transfer characteristics of Al2O3nanofluid in a circular tube fitted with helical twist inserts under constant heat flux using Fluent version 6.3.26.Different concentrations of Al2O3 nanoparticles(0.5%, 1.0% , 1.5%) and twist tape inserts with different twist ratio (y = 2.93, 3.91, 4.89)have been used for the simulation. The predicted results obtained by simulation compared with the literature value of water for plain tube helical tape inserts. (Pathipakka and Sivashanmugam 2010)proposed CFD simulation of heat transfer and friction factor behavior for the circular tube fitted with right-left helical twist insert with 100 mm spacer. The simulated Nusselt number and friction factor are compared with the experimental data with good agreement. (Shabanian, Rahimi et al. 2011) have carried out an experimental and CFD modeling on heat transfer and friction factor characteristics in air cooled heat exchanger using butterfly twist tape insert. They found that the insert configuration has a main effect on the new number, friction factor and thermal performance factor,the maximum thermal performance factor was obtained by the butterfly insert with an inclined angle of 90°. The results verified using CFD simulation with good agreements between the predicted and measured values of Nu number and friction factor values. In the present study, a new configuration of twist tape inserts is reportedflowusing CFD simulation, to predict the Nusselt number and friction factor in laminar flow regimes based on experimental data mentioned in (Pathipakka and Sivashanmugam 2010). This study can be used as guideline for experimental works. Physical model: The geometry of the Parabolic-cut twisted tape (PCT) insert is illustrated in Fig. 1. Twist tape of thickness (t) of 0.08 cm and width (W) of 2.545 cm with relative twisted ratios (y = 2.93, 3.91 and 4) fits in a tube with a diameter (D) of 2.54 cm and length (L) of 180cm. Different cut depth (w = 0.5, 1 and 1.5 cm) is used for each twisted tape. Steel and aluminium are selected as the material of construction of the tube and twisted tape, respectively. Water is selected as the working fluid and the thermophysical properties assumed to be Aust. J. Basic & Appl. Sci., 7(7): 69-76, 2013 70 temperature independent. The thermo-physical properties of water and materials used for simulation are shown in Table 1. The Reynolds number (Re), Nusselt number (Nu) and the friction factor (f) are defined by the following equations: Re uD ρ μ = (1) hD Nu k = (2) 16 Re f = (3) Where ρ is the density, u is velocity, μ is dynamic viscosity and k is the thermal conductivity of the fluid. his the heat transfer coefficient and Dis the inner diameter of the tube. Fig. 1: Parabolic-cut twisted insert Table 1: Thermo-physical properties of materials at 298 K Materials Density (Kg/m) Specific heat (J/kg K) Thermal conductivity (W/m K) Viscosity (Pa s) Water 998.2 4182 0.6 0.001003 Steel 8030 502.48 16.27 Aluminium 2719 871 202.4 Numerical Simulations: Three dimensional steady state laminar flow under constant heat-fluxed tube, fitted with twist tape inserts are particularized by the following model equations: 3.2.1 Continuity equation for an incompressible fluid. .( ) m p S t ρν ∂ +∇ = ∂ (4) 3.2.2. Conservation of momentum.
更多查看译文
AI 理解论文
溯源树
样例
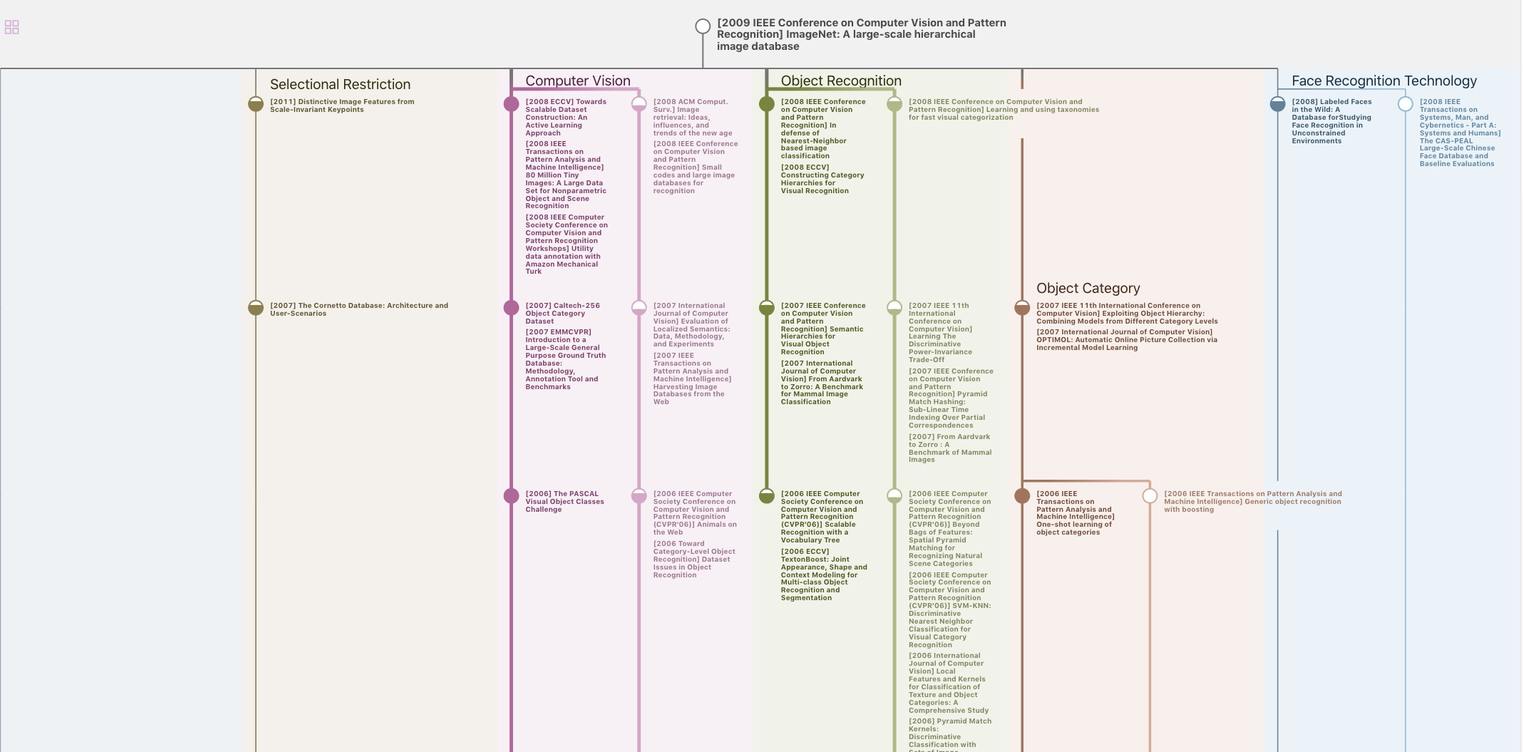
生成溯源树,研究论文发展脉络
Chat Paper
正在生成论文摘要