Application of Ultrasonic and Eddy Current Testing for Inspection of Rolls
semanticscholar(2016)
摘要
The work rolls used for hot and cold rolling of steel strips are subjected to severe mechanical and thermal stresses resulting in rolling contact fatigue, wear and plastic deformation on the roll bodies. The arduous service condition often leads to generation of thermal and mechanical cracks on roll surfaces and may vary from micro to macro levels in the form of discrete or continuous networks. These service induced cracks are required to be completely removed by roll grinding taken up in between service campaigns. However, in absence of Non Destructive Testing (NDT) of rolls, it is almost impossible to detect and remove any surface or sub-surface crack which may be generated during rolling. The cracks which remain undetected eventually propagate and join each other to cause fracture of the roll surfaces, leading to spalling or catastrophic failures in subsequent service campaigns. The roll failure not only brings about loss of costly roll materials but also results in severe loss of mill productivity as well. With a view to reduce the incidences of in-service roll failures, a program was initiated by RDCIS to carry out roll inspection with a unique combination of portable Ultrasonic and Eddy Current flaw detectors. A proper understanding of the nature and extent of the service induced cracks coupled with the use of suitable methodology was exploited to produce results which were suitably interpreted and converted to that of practical significance. Appropriate selection of probes and frequencies for Ultrasonic and Eddy Current inspection with their application on roll surfaces to produce authentic and reproducible defect signals, roll surface preparation and implementation of a suitable inspection methodology constituted the scope of the present work. Application of Ultrasonic and Eddy Current method of inspection of work rolls in Hot Strip Mill of Bokaro Steel Plant resulted in reduction of roll spalling by ~55% as compared to the incidences of roll spalling during the periods without NDT assisted roll grinding. The instances of roll spalling in Cold Rolling Mill of Bokaro Steel Plant was also reduced by ~22% with NDT assisted roll grinding as compared to the occurrences of roll spalling during the period when roll inspection with Ultrasonic and Eddy Current was not available to shop.
更多查看译文
AI 理解论文
溯源树
样例
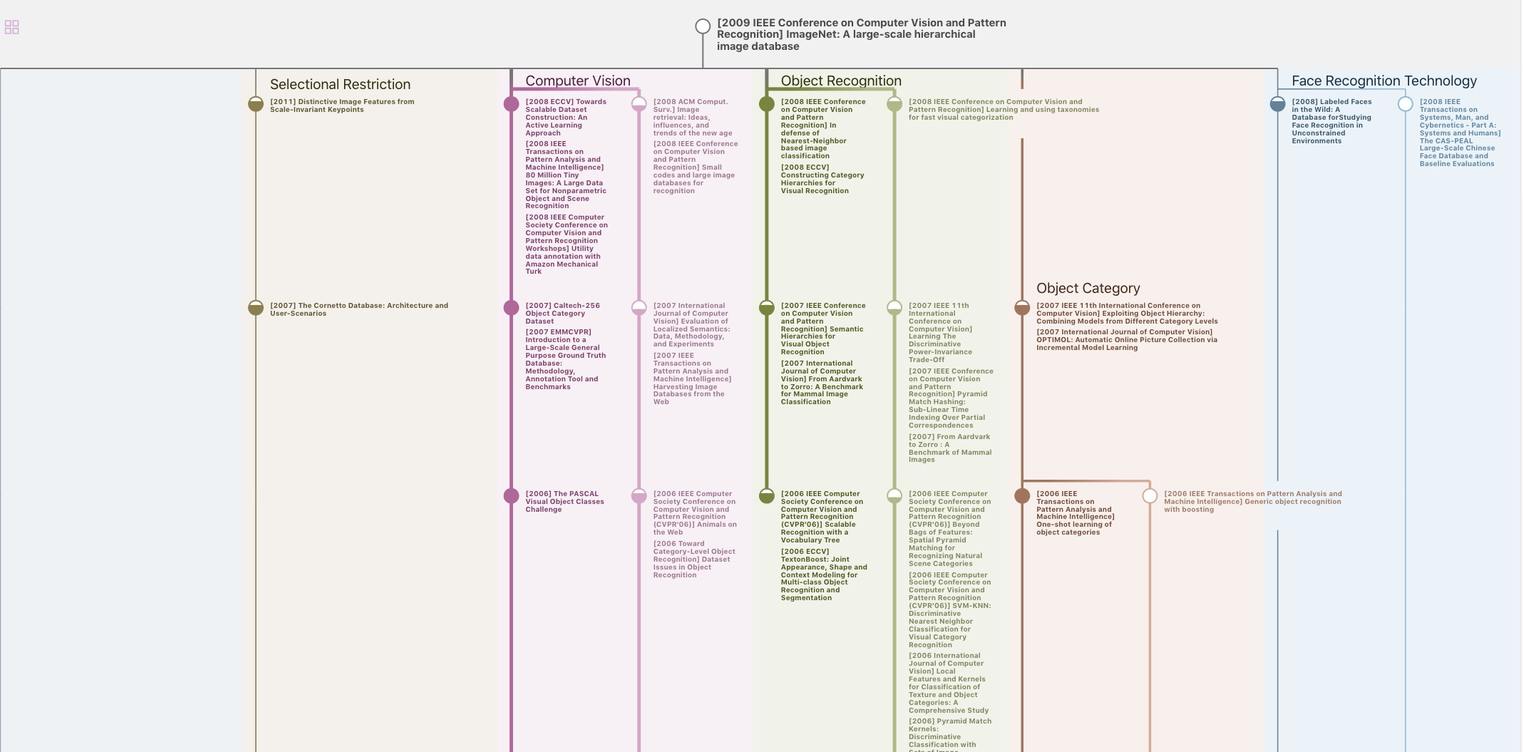
生成溯源树,研究论文发展脉络
Chat Paper
正在生成论文摘要