Performance and upgrade of the fast beam condition monitor at cms
semanticscholar(2015)
摘要
The Fast Beam ConditionMonitor (BCM1F) is a diamond based particle detector inside CMS. It consisted of 8 singlecrystal chemical vapor deposition (sCVD) diamond sensors on both ends of the interaction point, and was used for beam background and luminosity measurements. The system has been operated with an integrated luminosity of 30 fb−1, corresponding to a particle fluence of 8.78·10−13 cm−2 (24GeV proton equivalent). To maintain the performance at a bunch spacing of 25 ns and at the enhanced luminosity after the LHC Long Shutdown LS1, an upgrade to the BCM1F is necessary. The upgraded system features 24 sensors with a two pad metallization, a very fast front-end ASIC built with 130 nm CMOS technology, and new back-end electronics. A prototype of the upgraded BCM1F was studied in the 5GeV electron beam at DESY. Measurements were done on the signal shape as function of time, the charge collection efficiency as a function of voltage, and the amplitude as a function of the position of the impact point of the beam electron on the sensor surface. The preliminary results of this test-beam experiment and the status of the newly upgraded BCM1F will be presented. BCM1F DURING OPERATION BCM1F is a particle counter with nanosecond time resolution based on single-crystal chemical vapor deposition (sCVD) diamonds. Due to the linear dependence between detection probability and luminosity as shown in Figure 1, it is possible to use BCM1F as a luminosity monitor as well as a background monitor [1, 2]. During the first LHC running period from 2008-2012 BCM1F delivered online background and luminosity measurements as feedback for the CMS and LHC operation [3,4]. Since the data acquisition for BCM1F is decoupled from the main CMS DAQ, it could measure luminosity even before physics data was taken. ∗ maria.hempel@desy.de † brian.lee.pollack@cern.ch Figure 1: Particle detection probability as a function of luminosity. MOTIVATION FOR THE BCM1F UPGRADE The BCM1F modules are located around the beam pipe at a distance of 5 cm from the beam center. A particle fluence of 8.78·10−13 cm−2 (24GeV proton equivalent) at this position led to radiation damage of the laser diodes, which were used in the front-end electronics to convert the diamond sensor signal to an optical signal. Figure 2: Decrease of the amplification measured by an ADC amplitude spectrum. MOPD03 Proceedings of IBIC2014, Monterey, CA, USA ISBN 978-3-95450-141-0 134 Co py rig ht © 20 14 CC -B Y3. 0 an d by th er es pe ct iv ea ut ho rs Collider Specific Instrumentation The observation of the amplitude spectrum measured by an Analog-to-Digital converter (ADC) showed a decrease in the amplification as a function of integrated luminosity, as illustrated in Figure 2. This decrease in amplification lead to inefficiencies because smaller signals could not be detected. Additional inefficiencies occurred due to very large signals in the sensors, as shown in Figure 3. Figure 3: Amplitude as a function of time for large input signals. These signals caused the front-end electronics to saturate for around 100 ns and signals could not be detected during this time. After the saturation, the amplitude shows an overshoot for a few μs. All signals that arrived during this time are detected with less efficiency. Additionally, the proton bunch spacing for the future LHC run will be 25 ns, comparable to the peaking time of the amplifier. This potentially leads to pile-up of subsequent signals. BCM1F FRONT-END UPGRADE All BCM1F components are upgraded in order to match the demanding requirements corresponding to higher luminosity and smaller (25 ns) bunch spacing. Figure 4: Upgraded BCM1F layout with 12, 2-pad sCVD sensors on each side of the CMS interaction point. Distance between the CMS interaction point and sensors is 1.8m Firstly, the number of sensors is increased from 8 to 24 sCVD in order to improve the acceptance of the background measurements. The new BCM1F layout is illustrated in Figure 4 and contains 12 sensors on each side of the interaction point. The distance between the sensors and interaction point will be the same as in the first running period at 1.8m. Each sensor has a two pad metallization as shown in Figure 5 in order to decrease the count rate. The width of the gap between the two pads is between 5 and 25 μm. Figure 5: Two pad metallization of sCVD sensors. A new dedicated front-end ASIC, developed at CERN in collaboration with the University of Science and Technology AGH Krakow, is based on 130 nm CMOS technology and includes a fast trans-impedance preamplifier with an active feedback, a shaper stage and a fully differential output buffer. A better charge-to-voltage conversion of 50mV/fC is obtained (previously was 20mV/fC). Measurements done in the laboratory show a FWHM of less than 10 ns as shown in Figure 6. Figure 6: The ASIC output signal for various feedback and bias settings as a function of time for an injected test charge, which corresponds to one minimum ionizing particles. In order to characterise the impact of overshoots, a very large signal was fed into the front-end ASIC and the response was measured. As can be seen in Figure 7, the amplitude shows fast baseline recovery after about 30 ns. The upgraded carriage design, as shown in Figure 8, has two main parts: the C-shape, each of which holds 6 sensors and their corresponding front-end ASICs, and the flexible regions where the optical board will be placed. This design allows the placement of the analog opto-hybrid board (AOH) to be further away from the beam center (16 cm as opposed to 5 cm), which reduces the radiation load to the lasers. A C-shape assembled with the electronic parts is shown in Figure 9. The six square gold pads will hold the sensors and supply the bias voltage. Proceedings of IBIC2014, Monterey, CA, USA MOPD03 Collider Specific Instrumentation ISBN 978-3-95450-141-0 135 Co py rig ht © 20 14 CC -B Y3. 0 an d by th er es pe ct iv ea ut ho rs Figure 7: The ASIC output signal as a function of time for large (150 fC) injected input signals. Figure 8: Upgraded carriage design with the C-shape and flexible parts that hold the sensors, front-end ASICs, and the optical board. TESTS OF FRONT-END PARTS Sensors and analog optical hybrid boards (AOHs) were characterised in the laboratory. The performance of a prototype detector, comprising of a sensor, front-end ASIC, AOH, and fast digitizer was measured in a test-beam. Measurements in the Laboratory The leakage currents were measured for the sensors as a function of bias voltage. A result is shown in Figure 10. The currents are in the pA range as expected, due to the very high band gap for diamonds 5.4 eV. The charge collection efficiency (CCE), defined as the ratio between the measured charge and expected charge of the diamond at a given bias voltage, was measured. Figure 11 shows, as an example, the CCE as a function of bias voltage. A maximum CCE of around 95% above 40V was obtained. Figure 9: C-shape with mounted electronics. Figure 10: Measured leakage current as a function of bias voltage for an sCVD diamond sensor. Figure 11: Measured CCE and charge collection distance (CCD) as a function of bias voltage for a sensor. In order to determine the turn-on voltage and the linearity of the response of the laser, the output signal was measured as a function of the input voltage. The results are shown in Figure 12. Linearity up to 1.2V input voltage is observed. Figure 12: Response of the laser as a function of signal strength.
更多查看译文
AI 理解论文
溯源树
样例
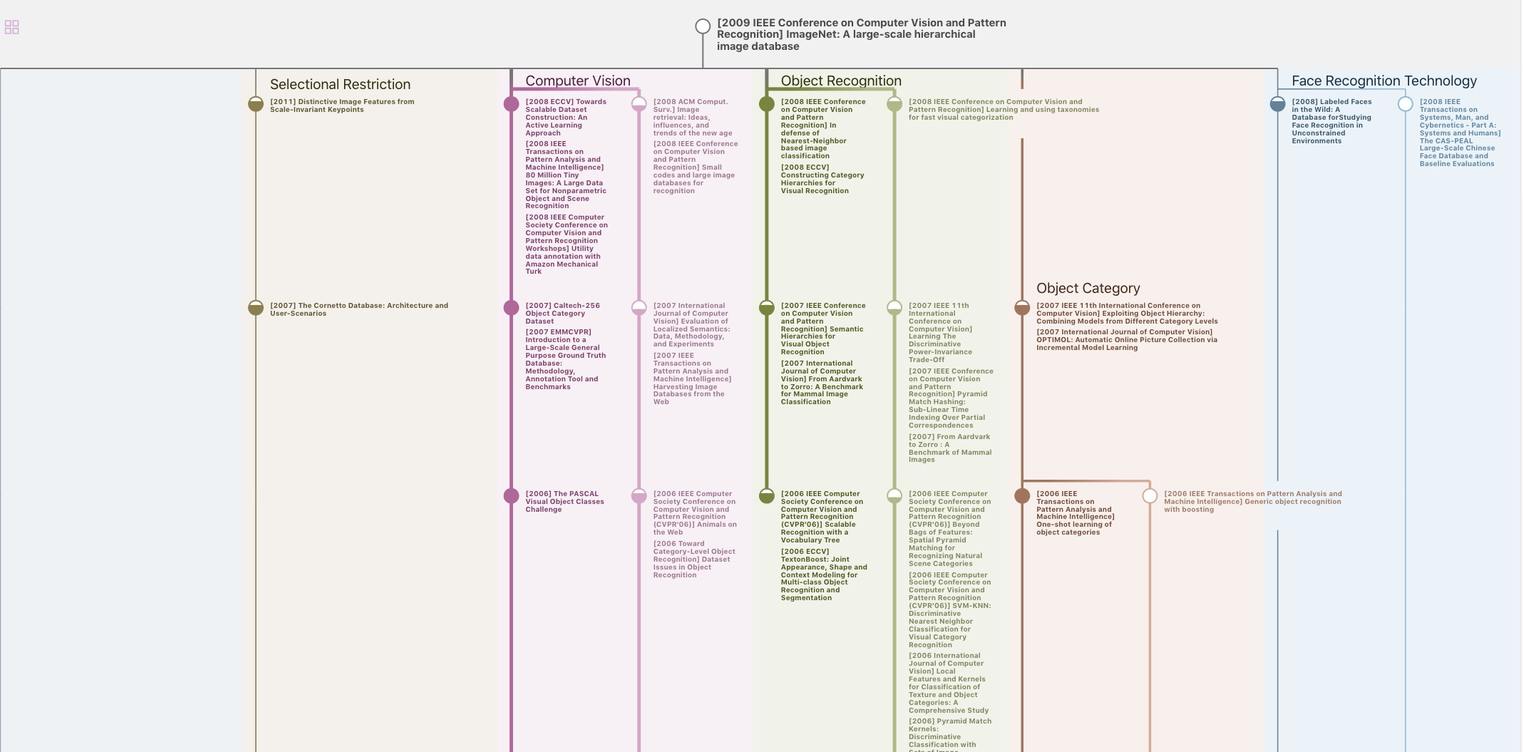
生成溯源树,研究论文发展脉络
Chat Paper
正在生成论文摘要