Additive Manufacturing for Next Generation Microwave Electronics and Antennas
semanticscholar(2019)
摘要
The paper will discuss the integration of 3D printing and inkjet printing fabrication technologies for microwave and millimeter-wave applications. With the recent advancements in 3D and inkjet printing technology, achieving resolution down to 50 um, it is feasible to fabricate electronic components and antennas operating in the millimeter-wave regime. The nature of additive manufacturing allows designers to create custom components and devices for specialized applications and provides an excellent and inexpensive way of prototyping electronic designs. The combination of multiple printable materials enables the vertical integration of conductive, dielectric, and semi-conductive materials which are the fundamental components of passive and active circuit elements such as inductors, capacitors, diodes, and transistors. Also, the on-demand manner of printing can eliminate the use of subtractive fabrication processes, which are necessary for conventional microfabrication processes such as photolithography, and drastically reduce the cost and material waste of fabrication. The utilization of 3D and inkjet printing to fabricate integrated circuits interconnects and antennas is an interesting avenue for research due to the customized nature of certain applications such as automotive radar and 5G wireless solutions. This paper will explore different ways of interfacing with monolithic microwave integrated circuits (MMICs) using additive manufacturing methods including printed vias, ramp interconnects, and wire bonds. With these structures, microwave properties such as matching and losses can be improved due to the ease of printing tailored interfaces that match with each individual device. It will also include demonstration of fully additively-manufactured antennas exhibiting excellent bandwidth and circular polarization, something that is expensive and difficult to achieve with traditional manufacturing methods. Finally, the paper will also introduce future directions for additively-manufactured electronics, including the packaging of high-power devices, cooling functionality, and using exotic materials for electromagnetic interference shielding and flexibility. INTRODUCTION Additive manufacturing has been gaining a lot of traction in the past decade as it promises very fast prototyping and low-cost manufacturing. Components that typically have month long lead times can be fabricated in mere days or even hours. Every year, additional 3D printable materials are being introduced to the market, and with that 3D printing can be utilized for new applications. One area of additive manufacturing is inkjet printing, which is a drop on demand method of printing large areas of devices with high accuracy, where metal, dielectric and semiconducting inks can be deposited quickly on almost all surfaces. Inkjet printing is extremely fast and low cost and can be utilized for applications at mm-wave frequencies allowing for fast prototyping and roll to roll manufacturing [1]. Additionally, the drop on demand nature of inkjet printing facilitates a low temperature (<200C) process as the metal is directly deposited on top of the substrate instead of using high temperature PVD systems. With this, flexible substrates are easily metallized without any bending or warping. Another area of additive manufacturing is 3D printing. 3D printers utilize a 3D model and a slicer to slice the model into very thin layers and recreates the model using these layers. Traditionally 3D prints were fabricated using fused deposition model (FDM) where a polymer filament, usually PLA or ABS plastics, was melted and extruded to make the model layer by layer. However new stereolithography (SLA) systems, where the model is built onto a platform in a photoactive resin bath, are generally able to achieve very high (10um) resolution print layers. Another big benefit of SLA printing is its surface roughness, which is on the order of hundreds of nanometers [2]. These two factors allow for 3D SLA printed parts to be utilized in high frequency mm-wave applications. This paper will delve into several topics in high frequency designs using both 3D and inkjet printing. Designs for fully inkjet printed RF passive components such as capacitors and inductors will be presented. These devices are critical to RF systems and are used in various ways including impedance matching and DC/RF chokes. These devices can be easily manufactured in the same process, in the same inkjet printer, saving time and cost. Other passive devices such as die interconnects will be discussed. These fully additive manufactured interconnects, which replaces wire bonding, are a revolutionary way of designing smart packaging, the inclusion of many different functionality in one smart package. Next advanced 3D printed antennas are presented. These specific antennas demonstrate complex structures that are difficult or impossible to fabricate using traditional manufacturing techniques and drastically reduce the time of prototype to production. These antennas introduce advantageous features, such as high bandwidth or ease of integration with other components. Finally, the paper will explore future topics for research. INKJET PRINTED PASSIVE COMPONENTS Typically, in an RF system, baluns, capacitors and inductors are utilized as in signal conditioning, impedance matching, coupling/choking applications. These devices are critical to RF applications and should have low loss and high quality (Q) factor. Typically, lumped components in standard surface mount packages, such as 0603, are placed and soldered onto circuit boards. However, these packages are tall and bulky and can snap off when bent on flexible substrates. Inkjet printed capacitors and inductors are planar structures, conformal, and low loss which can withstand bending when printed on flexible substrates such as LCP. Additionally, components which generally take many fabrication steps, such as metallization and dielectric deposition can be completed in one inkjet printing process. The additive, drop-on-demand aspect of fabrication is also low waste, which can save drastic costs when printing in massive quantities. Metal Insulator Metal Capacitors Metal insulator metal (MIM) capacitors are the most basic single layer capacitors. These capacitors are two metal electrodes separated by a dielectric, both of which can be inkjet printable. For metal conductive layers, silver nano particle (SNP) was printed and for dielectric insulator layers, polyvinylpyrrolidone(PVP) was printed for thin films (>0.5m), or production epoxy based negative photo resist for thick films(>3m). These allow for various controls of capacitance values, as printing thicker or thinner dielectrics or changing the electrode area, granting full control of design specifications based on the end application. Flexible MIM capacitors fabricated on polyimide substrates show self-resonance frequency(SRF) of >1GHz[3], while MIM capacitors with 1.6m – 1.8m thick PVP dielectric and SNP metal electrodes were fabricated on silicon substrate as shown in Fig.1 has SRF of 1.2GHz, a maximum Q factor of 25, with a capacitance per area of 33pF/mm [4]. Fig. 1. Inkjet printed MIM capacitors on silicon wafers Baluns and Inductors Inductors and baluns are similar spiral structures. Baluns are usually used in signal conditioning applications to change balanced signals into unbalanced and vice versa. Transformer based baluns incorporate three windings in 5-layer structures as shown in Fig. 2a and b respectively [5]. The transformer balun demonstrates the complex structures that can be fabricated using additive inkjet printing. Inductors have a similar winding structure since they require long conductive traces to get appreciable inductance values. 1.5 turn inductors were fabricated with SNP ink as the conductive metal and epoxy based negative photo resist ink as the dielectric layer separators and shows a Q factor of 21 at 1 GHz [6]. Both applications are inherently multilayer structures, but these demonstrations show the ease of inkjet printing multilayer RF components which can operate at high frequencies and the level of integration that can be achieved by utilizing inkjet printing to reduce processing steps. Fig 2. Inkjet printed 5-layer RF balun schematic (a) and fabricated sample on LCP (b). (a) (b) INTERCONNECTS Interconnects are essential packaging components for the practical implementation of any microelectronic device in a functional electronic system. Specifically, first-level interconnects are responsible for interconnecting a microelectronic chip, or die, with its packaging substrate. In a modern wireless system, this packaging substrate can take the form of a metallic leadframe for traditionally packaged off-the-shelf components, a laminate-based interposer for signal fanout and redistribution, or a printed circuit board (PCB) where a chip is integrated directly with other packaged components on the primary host substrate. These packaging methods typically achieve first-level interconnection through bond wire or flip-chip technologies depending on several design factors, including signal pad location, thermal path management, and the routing of signals below an interconnected device. Wire and ribbon bonding are rapid, low-cost, and mature methods for realizing these chip-to-board interconnects, however increased parasitics and mechanical stability are highlighted concerns that must be considered in a practical setting [7]. With the recent growth of additive manufacturing technologies for the development of wireless components, packages, and systems, the first-level interconnect is a prime candidate for investigating the integration of inkjet and 3D printing fabrication methods to realize fully-printed 3D RF interconnect transitions. The use of additive manufacturing technologies for the interconnection process has the potential to offer several improvements from traditional wire bonding soluti
更多查看译文
AI 理解论文
溯源树
样例
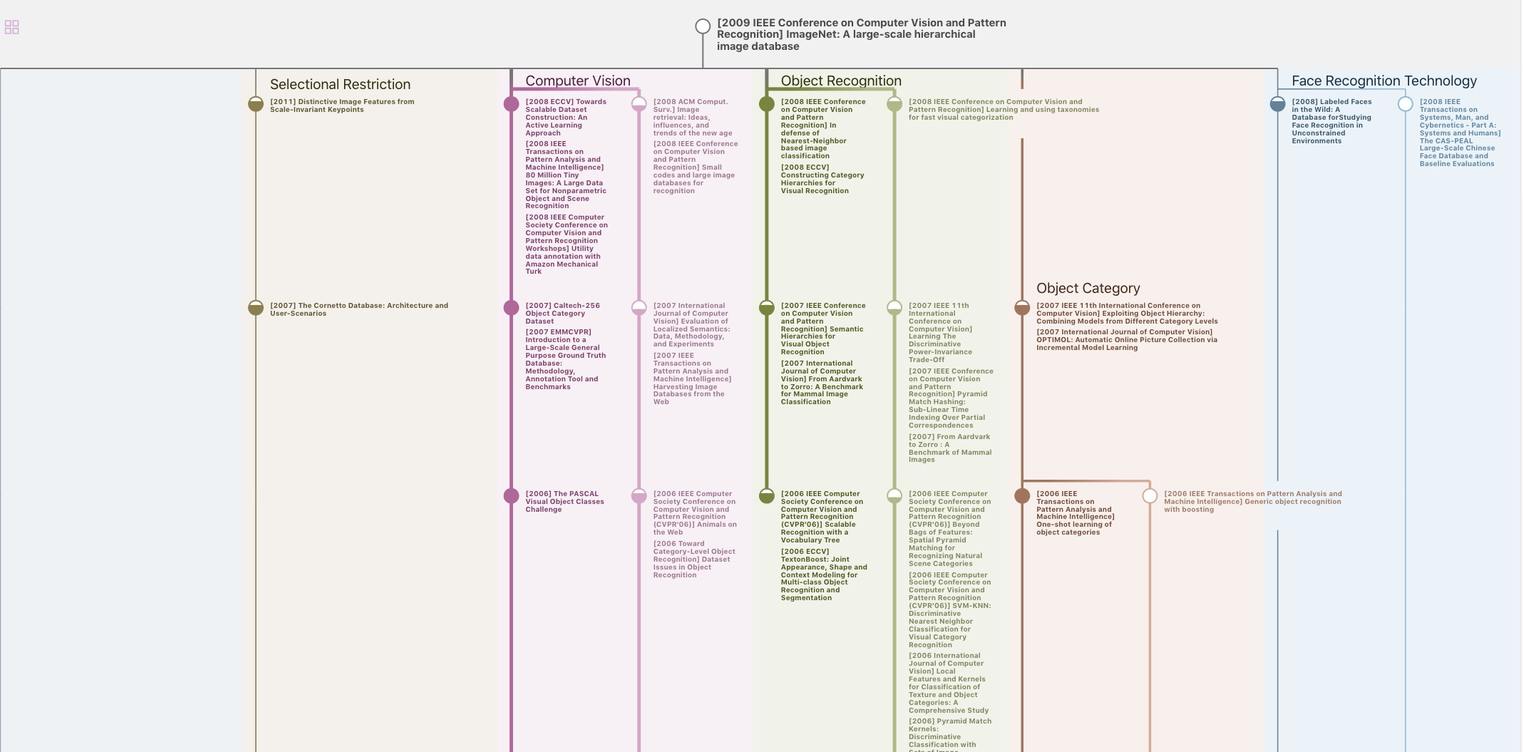
生成溯源树,研究论文发展脉络
Chat Paper
正在生成论文摘要