Three-dimensional printing versus conventional machining in the creation of a meatal urethral dilator: development and mechanical testing
BioMedical Engineering OnLine(2020)
摘要
Background Three-dimensional (3D) printing is a promising technology, but the limitations are often poorly understood. We compare different 3D printing methods with conventional machining techniques in manufacturing meatal urethral dilators which were recently removed from the Australian market. Methods A prototype dilator was 3D printed vertically orientated on a low-cost fused deposition modelling (FDM) 3D printer in polylactic acid (PLA) and acrylonitrile butadiene styrene (ABS). It was also 3D printed horizontally orientated in ABS on a high-end FDM 3D printer with soluble support material, as well as on an SLS 3D printer in medical nylon. The dilator was also machined in stainless steel using a lathe. All dilators were tested mechanically in a custom rig by hanging calibrated weights from the handle until the dilator snapped. Results The horizontally printed ABS dilator experienced failure at a greater load than the vertically printed PLA and ABS dilators, respectively (503 g vs 283 g vs 163 g, p < 0.001). The SLS nylon dilator and machined steel dilator did not fail. The steel dilator is the most expensive with a quantity of five at 98 USD each, but this decreases to 30 USD each for a quantity of 1000. In contrast, the cost for the SLS dilator is 33 USD each for five and 27 USD each for 1000. Conclusions Low-cost FDM 3D printing is not a replacement for conventional manufacturing. 3D printing is best used for patient-specific parts, prototyping or manufacturing complex parts that have additional functionality that cannot otherwise be achieved.
更多查看译文
关键词
Three-dimensional printing, Urology, Urethral stricture, Intermittent urethral catheterisation
AI 理解论文
溯源树
样例
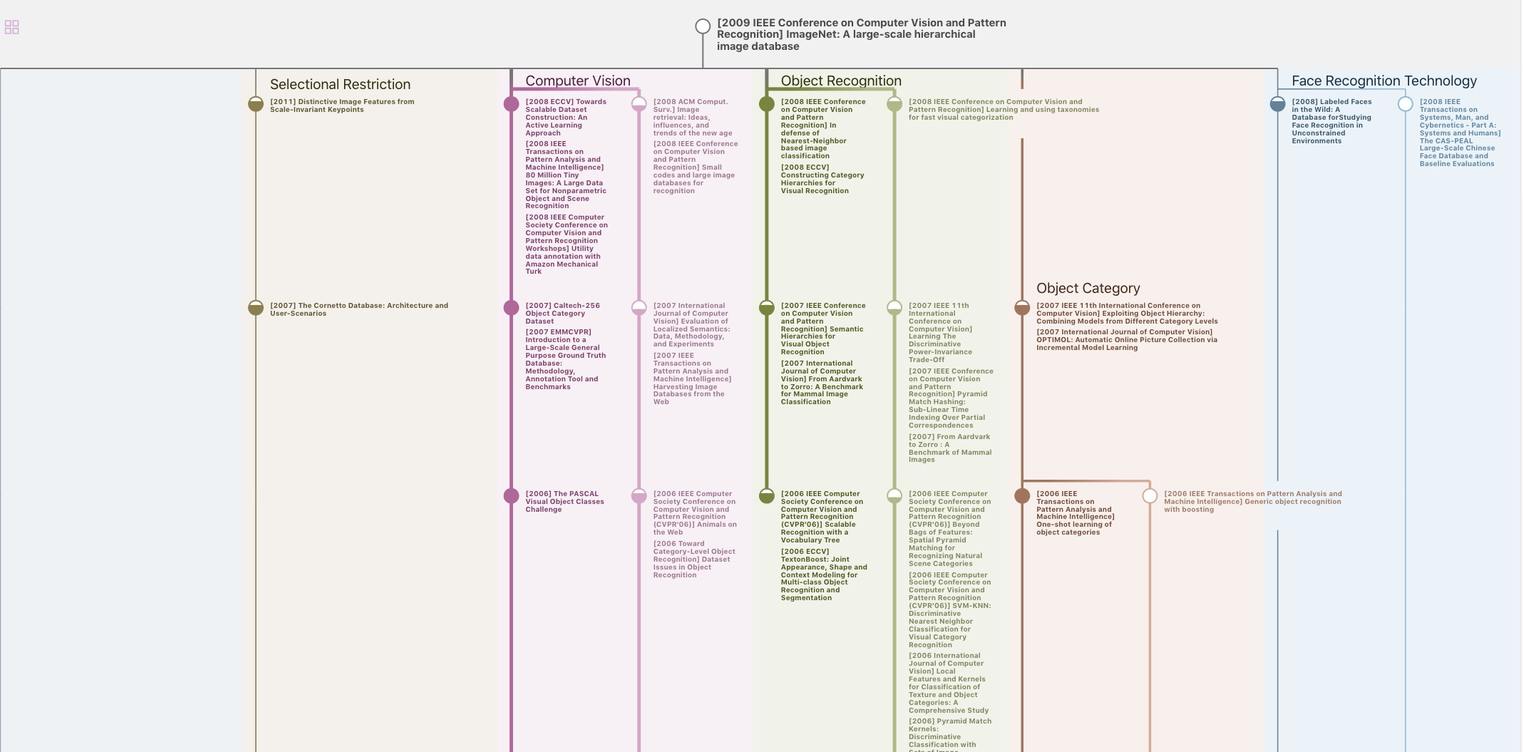
生成溯源树,研究论文发展脉络
Chat Paper
正在生成论文摘要