Central Tube Erosion Investigation Of Torque Impactor In The Deep Shale Gas Formation
Energy Sources Part A-recovery Utilization and Environmental Effects(2020)
摘要
To figure out erosion mechanism of the torque impactor and optimize the structure of such tools, CFD (computational fluid dynamics) simulation model of the central tube is established. Results show that the location of the most serious erosion and the maximum erosion rate (4.80 x 10(-4) (kg/(m(2)center dot s)) are consistent with the actual situation. Solid particles retained in the central tube are distributed unevenly. When drilling fluid velocity increases from 26 to 32 m/s, the maximum erosion rate of the central tube increases from 3.89 x 10(-4) to 6.60 x 10(-4) (kg/(m(2)center dot s)). As the mass flow rate of the solid particles increases from 0.2 to 0.8 kg/s, the maximum erosion rate increases from 5 x 10(-4) to 28 x 10(-4) (kg/(m(2)center dot s)). With increasing of particle diameter from 0.2 to 1.2 mm, the maximum erosion rate increases from 5.98 x 10(-4) to 48 x 10(-4) (kg/(m(2)center dot s)) and shows different upward trend in different intervals of particle diameters. As the solid particle shape coefficient increases from 0.4 to 1, the maximum erosion rate decreases from 14 x 10(-4) to 1 x 10(-4) (kg/(m(2)center dot s)). Grey correlation coefficient method indicates that the most relevant to the erosion rate is the drilling fluid velocity, followed by the particle shape coefficient, the particle diameter, and the solid particle mass flow rate.
更多查看译文
关键词
Deep shale gas,torque impactor structure,CFD simulation,erosion rate,gray correlation coefficient method
AI 理解论文
溯源树
样例
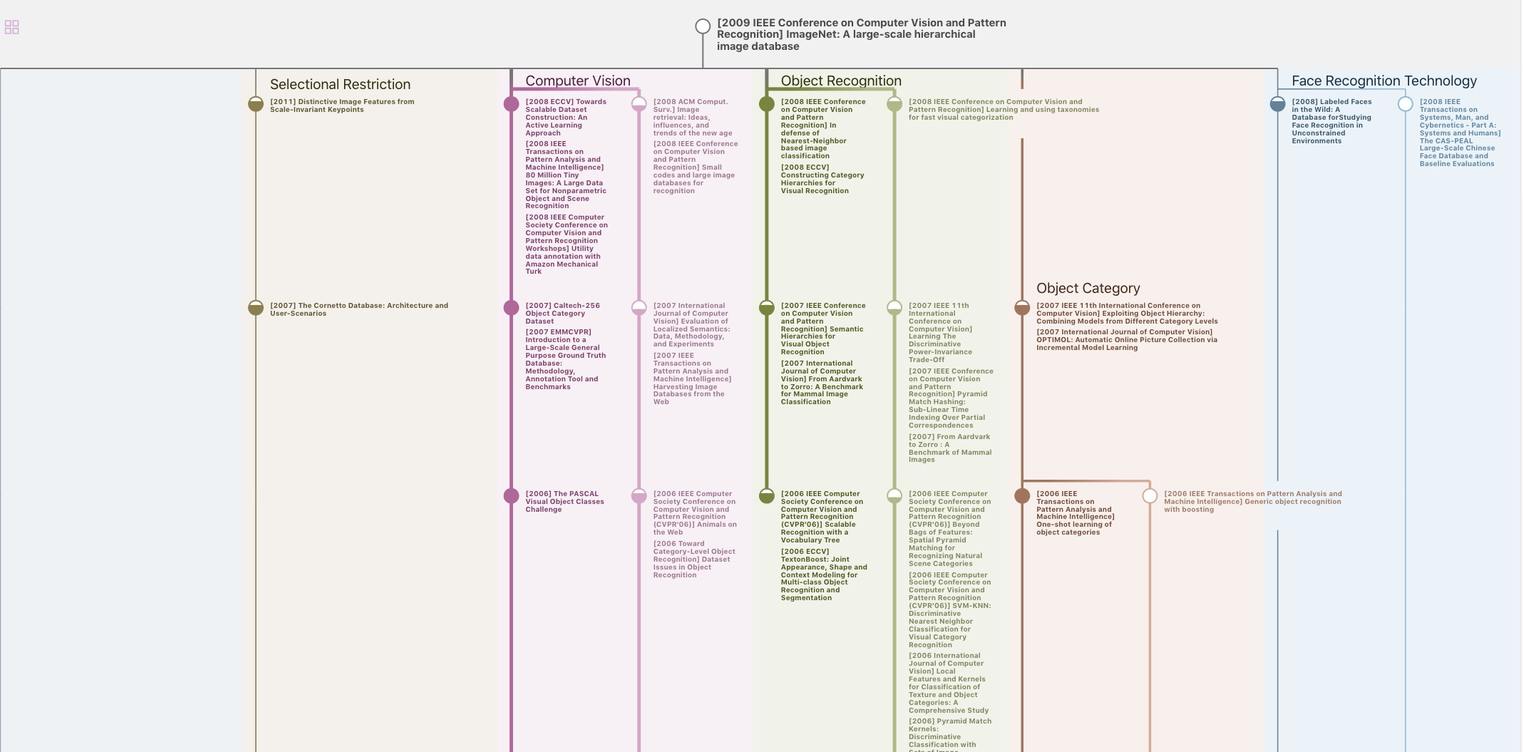
生成溯源树,研究论文发展脉络
Chat Paper
正在生成论文摘要